ElectricEd
100 W
Wacko! I received a 408 threaded side cover from Crystalyte Europe recently as a spare. When I had a closer look it seemed to be a bit heavier than usual and had some surface corrosion on the threaded boss. Hmm. Out with the magnet...
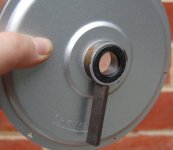
Adding to that, there's a seal inserted into the boss. How good is that?
No more sheared off clusters.
One less place for water to get in.
Keep it up Mr Crystalyte. These are the sort of product developments that will get you to the top and keep you there. Well done!
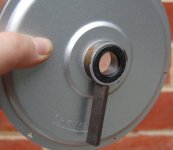
Adding to that, there's a seal inserted into the boss. How good is that?
No more sheared off clusters.
One less place for water to get in.
Keep it up Mr Crystalyte. These are the sort of product developments that will get you to the top and keep you there. Well done!