This thread is to discuss (and test) the difference between mounting the main electrolytic capacitors in controllers vertically vs horizontally, relative to the PCB, so that their leads are the shortest possible, causing the least resistance (and inductance) path between the PCB power planes and the capacitors' internals, enabling them to more easily do the job they're there to do--fill in for the battery during the instantaneous switching loads of PWM motor control.
I started the question over on this thread:
http://endless-sphere.com/forums/viewtopic.php?f=2&t=13638&start=15
and am copying my original comments plus a couple of relevant quotes from others here in this opening post.
If there's any way you can seat those main filter caps vertically on the board, you should try it. (yeah, I know they won't fit in the case if you do this, unless you drill holes for the caps to stick out)
Those cap leads are almost certanly only steel, plated with copper and tinned, so they don't conduct electricity *or* heat very well compared to the copper traces on the board. At high power draws in the controller, having the caps' leads a fraction of what they are now should make a difference to performance.
If you can get caps that have formed copper/alloy leads not made of steel, it'd be even better. Or at least ones with thicker plating on them, and thicker leads overall.
When I have tested my 2QD brushed controller with various cap configurations, it performs better under heavy loads with the cap vertically right on the board with the leads as short as possible than mounted as I typically see in photos of ebike controllers, sideways, parallel to the board with long leads down to the PCB.
The waveform at the controller output is smoother, a bit, using the same size cap with vertical mounting, at the higher current draws. AFAIK it's because the cap leads aren't creating as much resistance when they're shorter, so not preventing them from doing their jobs as much.
I first even looked into this because of info at the 4QD site about it, and finding that under some conditions it's actually possible to heat the cap leads enough to melt the solder holding them into the board, when they're that long (hasn't happened to me, but did at 4QD to the designer during early versions of his controllers).
Another thing to consider is using smaller uF caps, but more of them, so that the current flow in and out of each one is less. They'll heat up less, and so will the leads. It will still matter for the leads to be as short as possible, but less than if all that current has to flow thru fewer sets of leads.
Of the few larger controllers I've looked at, such as my Curtis 1204, all use multiple smaller caps in parallel, mounted vertically to the board. Some glue the caps down to the board at the base of each cap, and also really fit them tight against the PCB so they can't flex from vibration. AFAICS the Curtis just has glue between caps, but there are so many that they probably damp the vibrations enough to not worry about it much, plus the whole board bottom is secured to a couple of bus bars that help prevent the PCB from flexing (along with the twin heatsinks the MOSFETs are on).
I'm fairly sure it's not a cost thing, because most of the time when I've looked for low-ESR caps to replace blown ones in various power supplies, bigger ones don't cost enough more than little ones to justify using a lot of little ones unless there is some engineering reason to do so.
I'm not sure I have the capability to do the kind of testing needed to show the difference between both ways, plus my controller is just a brushed DC unit, and so would be significantly different in operation than these BLDC controllers (though I suspect not that much different in actual results between the two types for this issue).
If I do manage to be able to test this, and find anything different between the two methods, I'll post my results in this thread. Anyone else willing to methodically test this is welcome to post their results here as well.
If any kind of mechanical problems result from the vertical mounting, I'd like to see those reports, too.
My own (modded) 2QD has only the single cap on it right now, vertically mounted flush to the PCB, with the cap partly outside the controller box and tightly held in place by the hole it passes thru (is a good friction fit, so no vibration movement of the can).
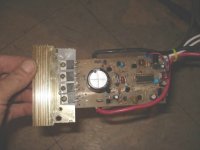
I started the question over on this thread:
http://endless-sphere.com/forums/viewtopic.php?f=2&t=13638&start=15
and am copying my original comments plus a couple of relevant quotes from others here in this opening post.
If there's any way you can seat those main filter caps vertically on the board, you should try it. (yeah, I know they won't fit in the case if you do this, unless you drill holes for the caps to stick out)
Those cap leads are almost certanly only steel, plated with copper and tinned, so they don't conduct electricity *or* heat very well compared to the copper traces on the board. At high power draws in the controller, having the caps' leads a fraction of what they are now should make a difference to performance.
If you can get caps that have formed copper/alloy leads not made of steel, it'd be even better. Or at least ones with thicker plating on them, and thicker leads overall.
When I have tested my 2QD brushed controller with various cap configurations, it performs better under heavy loads with the cap vertically right on the board with the leads as short as possible than mounted as I typically see in photos of ebike controllers, sideways, parallel to the board with long leads down to the PCB.
The waveform at the controller output is smoother, a bit, using the same size cap with vertical mounting, at the higher current draws. AFAIK it's because the cap leads aren't creating as much resistance when they're shorter, so not preventing them from doing their jobs as much.
I first even looked into this because of info at the 4QD site about it, and finding that under some conditions it's actually possible to heat the cap leads enough to melt the solder holding them into the board, when they're that long (hasn't happened to me, but did at 4QD to the designer during early versions of his controllers).
SpeedEBikes said:I suppose a quick hack solution leaving the caps in place would be to solder some fat copper wire along the leads. Kind of like how people sometimes build up the traces on the boards...
methods said:Doc has tried that. I dont like it for a few reasons. One reason is that it makes it so that you cant move the caps around anymore - makes them stiff which makes them brittle. It is also a lot of work and somewhat risky and difficult in the tight confines.
I suspect that it is the inductance of the long leads more than the resistance that affects performance.
Solutions include mounting smaller caps vertically...
I suppose I could mount 470uF caps vertically and then try to jam a few 1000uF in there to make up the total difference.
The reality is this is now I specified the controllers to come in so I probably wont be re-working them.
The way I see it there are ceramic caps in parallel and I would rather have 4,700uF of slightly higher ESR electrolytics than 2,000uF of lower ESR electrolitics.
I think the ceramics in parallel really help.
Good suggestion though. Maybe someone can do a test and if the results are astounding (like 5% or 10%) improvement then we can think harder about it.
Another thing to consider is using smaller uF caps, but more of them, so that the current flow in and out of each one is less. They'll heat up less, and so will the leads. It will still matter for the leads to be as short as possible, but less than if all that current has to flow thru fewer sets of leads.
Of the few larger controllers I've looked at, such as my Curtis 1204, all use multiple smaller caps in parallel, mounted vertically to the board. Some glue the caps down to the board at the base of each cap, and also really fit them tight against the PCB so they can't flex from vibration. AFAICS the Curtis just has glue between caps, but there are so many that they probably damp the vibrations enough to not worry about it much, plus the whole board bottom is secured to a couple of bus bars that help prevent the PCB from flexing (along with the twin heatsinks the MOSFETs are on).
I'm fairly sure it's not a cost thing, because most of the time when I've looked for low-ESR caps to replace blown ones in various power supplies, bigger ones don't cost enough more than little ones to justify using a lot of little ones unless there is some engineering reason to do so.
I'm not sure I have the capability to do the kind of testing needed to show the difference between both ways, plus my controller is just a brushed DC unit, and so would be significantly different in operation than these BLDC controllers (though I suspect not that much different in actual results between the two types for this issue).
If I do manage to be able to test this, and find anything different between the two methods, I'll post my results in this thread. Anyone else willing to methodically test this is welcome to post their results here as well.
If any kind of mechanical problems result from the vertical mounting, I'd like to see those reports, too.
My own (modded) 2QD has only the single cap on it right now, vertically mounted flush to the PCB, with the cap partly outside the controller box and tightly held in place by the hole it passes thru (is a good friction fit, so no vibration movement of the can).
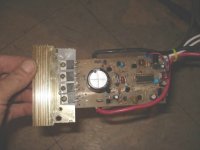