spinningmagnets
100 TW
This isn't necessarily the best way for me to do it, or even a good way for anyone to do it, but here it is...
I acquired some high-amp LTO cells. This chemistry has a low 2.4V nominal voltage so it takes 5S X 2.4V = 12.0V. I am using 6S so in case of the failure of a BMS, I can charge the cells directly from a car's 14V alternator with no BMS during an emergency.
This chemistry provides an exceptional number of cycles, measured in the thousands, and it also performs well in very cold weather (it snows here in Kansas). It is also known to be able to be drained down to near zero volts, and it can still be charged up with confidence, without fear of a Lithium fire.
These are from Kokam in South Korea. Asia is experiencing a surge in the purchase of electric buses and also hybrid buses. The hybrid cells must provide the full vehicle amps from a smaller pack (compared to a pure EV vehicle), so they are all very high C-rate. Even when the cells are not fully loaded to their max ability, the highest C-rate construction allows them to run cooler under all conditions.
Having multiple internal tabs of the thickest construction will take up some of the room that could be used to fill the cell with more active material, so these cells give up some capacity in exchange for very high current, without getting too hot.
Anybody can order pouch cells in any size, shape, or chemistry...along with the highest possible C-rate. All you have to do is pay up front for $500K's worth. Fortunately, an existing size fits my application, so I only needed to buy six.
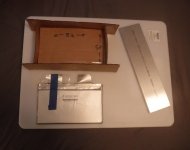
In the pic above, the white board underneath is a plastic kitchen cutting board that is 9mm thick (a hair under 3/8ths inch), made from High Density Poly Ethylene / HDPE, 15-inches by 20" / 38cm X 50cm ($13 at Walmart).
The positive tab on the cell has a section of plastic ziplock bag over it, and held in place by low-stickiness blue painters tape (doesn't leave a sticky residue).
The Cardboard Aided Design shape helps me calculate the sizes I need to cut to make the case. The battery tabs will slide through thin slots I will cut into the head-board. The aluminum bar is for making the tab clamps, 1/2" X 3" and a foot long ($15 on ebay).
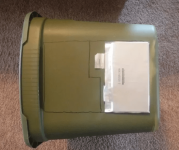
The pic above shows me cutting 1.5mm thick plastic cell separators/insulators from the sides of a plastic storage tub.
The flat lid will be used as the plastic bench cover for the pack assembly.
I acquired some high-amp LTO cells. This chemistry has a low 2.4V nominal voltage so it takes 5S X 2.4V = 12.0V. I am using 6S so in case of the failure of a BMS, I can charge the cells directly from a car's 14V alternator with no BMS during an emergency.
This chemistry provides an exceptional number of cycles, measured in the thousands, and it also performs well in very cold weather (it snows here in Kansas). It is also known to be able to be drained down to near zero volts, and it can still be charged up with confidence, without fear of a Lithium fire.
These are from Kokam in South Korea. Asia is experiencing a surge in the purchase of electric buses and also hybrid buses. The hybrid cells must provide the full vehicle amps from a smaller pack (compared to a pure EV vehicle), so they are all very high C-rate. Even when the cells are not fully loaded to their max ability, the highest C-rate construction allows them to run cooler under all conditions.
Having multiple internal tabs of the thickest construction will take up some of the room that could be used to fill the cell with more active material, so these cells give up some capacity in exchange for very high current, without getting too hot.
Anybody can order pouch cells in any size, shape, or chemistry...along with the highest possible C-rate. All you have to do is pay up front for $500K's worth. Fortunately, an existing size fits my application, so I only needed to buy six.
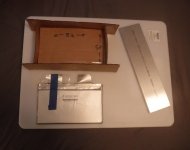
In the pic above, the white board underneath is a plastic kitchen cutting board that is 9mm thick (a hair under 3/8ths inch), made from High Density Poly Ethylene / HDPE, 15-inches by 20" / 38cm X 50cm ($13 at Walmart).
The positive tab on the cell has a section of plastic ziplock bag over it, and held in place by low-stickiness blue painters tape (doesn't leave a sticky residue).
The Cardboard Aided Design shape helps me calculate the sizes I need to cut to make the case. The battery tabs will slide through thin slots I will cut into the head-board. The aluminum bar is for making the tab clamps, 1/2" X 3" and a foot long ($15 on ebay).
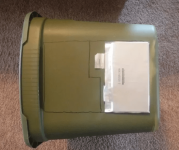
The pic above shows me cutting 1.5mm thick plastic cell separators/insulators from the sides of a plastic storage tub.
The flat lid will be used as the plastic bench cover for the pack assembly.