Hi @Comrade,
You haven't mentioned yet which model of motor you have, but it looks like it may be an Aikema AKM-128CST, or an AKM-100CST. Is it one of those models please?
I've got lots of experience with those motors and the problem is not in the axle, or the bearings, the problem exists in poor fitting of the freehub carrier into the side cover.
The CST series motors have a central part of the freehub, around which the freehub body rotates, which is press-fitted, or in some motors it is screwed into the side cover. There was probably a small piece of metal swarf in the hole when they pressed it into the side cover causing your part to be fitted at a slight angle. This part holds not one, but two bearings in the drive side, if this part is misaligned then the bearings exert a strong cyclical bending force on the axle, the direction of which rotates with the motor, causing the wobble that you see with each rotation.
It is very important to fix this because the axle in these motors is not just one long piece of steel threaded rod, it is actually split into two short stub-axles which are each bolted to opposite sides of the aluminium motor core just inside each side cover. Any flex that you are seeing at the drop-out is also happening to the motor core and the axle is only held by three machine screws at that end!
TL;DR, you need a new side cover which comes with a new freehub assembly.
Luckily they are really cheap at around $15. Buy one, or ask Topbikekit to send you one free of charge. They are very easy to replace it yourself and if the motor is brand new they probably won't require any special tools. Before you email TBK about it, first make sure you can unscrew the side cover youself. Remove the locknuts and try and unscrew the whole side cover anti-clockwise.
Side covers:
AKM-128CST Side Cover
http://www.topbikekit.com/akm128cst...with-cassette-base-for-replacement-p-858.html
AKM-100CST Side Cover
http://www.topbikekit.com/akm100cst...with-cassette-base-for-replacement-p-859.html
I have one of these motors apart on my desk at the moment and I am happy to explain more if you want to PM me.
Thanks,
Oli.
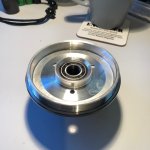