12p3phPMDC
1 kW
- Joined
- Mar 16, 2009
- Messages
- 462
Inspired by the Miles' epicyclic retrodirect with the opposing spragues and
these picture examples, I want to explore the idea of eCVT using two motors
and two independent controllers.
The system would use the planet carrier as the output, the ring and sun gears
as inputs. It would then have two opposing spragues on the ring and sun gears
so that when torque is supplied from one motor, lets say on the ring, the sun sprague
locks and the carrier is driven. Vice versa, if the sun gear is fed torque from the other
motor, the ring sprague locks, and the planet carrier is driven.
You could probably build the system without spragues (see examples), but
It seems the stall torque and current would be high and cause heating problems.
Therefore the spragues would simplify the control at the expense
of regen. But you get dual redundant operation, i.e. if one motor fails
the other could still drive the system.
I have 62 tooth GT pulleys that would be perfect for a pressfit over
the ring gear of a 75mm Matex Planetary. Copying the overhead lift example,
I would then do a reduction off the ring drive motor to the 62 tooth GT pulley.
I would then do a direct drive out of one motor and feed the sun gear.
The reductions would need to be matched so
that the torque inputs from the two motors would be matched.
Sun to Carrier Reduction: Rs (fixed for given plantetary)
Ring to Carrier Reduction: Rr (fixed for a given planetary)
Motor to Ring Reduction: Rmr (adjustable from off the shelf pulleys)
The total ring reduction would be Rr*Rmr. Set to equal to the Sun to carrier reduction, Rs
and solve for Rmr. That way the torques from each motor relative to the carrier would be closely
matched at the same motor speed.
View attachment 1
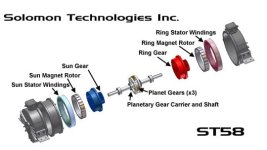
these picture examples, I want to explore the idea of eCVT using two motors
and two independent controllers.
The system would use the planet carrier as the output, the ring and sun gears
as inputs. It would then have two opposing spragues on the ring and sun gears
so that when torque is supplied from one motor, lets say on the ring, the sun sprague
locks and the carrier is driven. Vice versa, if the sun gear is fed torque from the other
motor, the ring sprague locks, and the planet carrier is driven.
You could probably build the system without spragues (see examples), but
It seems the stall torque and current would be high and cause heating problems.
Therefore the spragues would simplify the control at the expense
of regen. But you get dual redundant operation, i.e. if one motor fails
the other could still drive the system.
I have 62 tooth GT pulleys that would be perfect for a pressfit over
the ring gear of a 75mm Matex Planetary. Copying the overhead lift example,
I would then do a reduction off the ring drive motor to the 62 tooth GT pulley.
I would then do a direct drive out of one motor and feed the sun gear.
The reductions would need to be matched so
that the torque inputs from the two motors would be matched.
Sun to Carrier Reduction: Rs (fixed for given plantetary)
Ring to Carrier Reduction: Rr (fixed for a given planetary)
Motor to Ring Reduction: Rmr (adjustable from off the shelf pulleys)
The total ring reduction would be Rr*Rmr. Set to equal to the Sun to carrier reduction, Rs
and solve for Rmr. That way the torques from each motor relative to the carrier would be closely
matched at the same motor speed.
View attachment 1
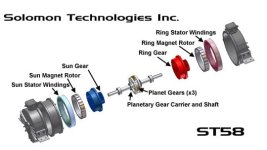