Good day, first time posting. I have an FX-15 fat tire bike from BPM Imports, and it is my only mode of transport to and from work.
It runs on a 48v 13AH battery. Ito was using the bike in snow, and probably overloaded the controller with stall load. I believe the unit is recoverable with some input from those more familiar because of the way it blew. I turned on the bike, went in for gloves and helmet, and came out to find it powered off.
First thought was that it timed out, but no such luck. No power on to be had. I brought the bike back in the garage, and tinkered with the controller wires. Bad move, as I moved the POS battery wire it let out a shorting sound. I immediately removed the battery. I proceeded to open up the controller and found the POS battery wire was completely disconnected. I blew a hole right thru the PCB. I suspect that no components failed, but the solder joints became overheated, leading to an open circuit. The short only happened when I moved the wire.
My question is
'how is this wire intended to be tied in?'
You can see the capacitor prong,(actually both prongs.) note also that the NEG battery wire has also become unsoldered.
As for the crater left in the board, I was considering a slice of a MIG welder contact tip to slide over the cap prong, then fill - but without bridging across any wrong contacts.
I will be ordering a replacement controller, probably upgrading to a 35 A 1000 watt box, and perhaps an LCD8H. But right now I just need a quick fix.
Seems like a simple fix once connection is confirmed. TIA, Bob
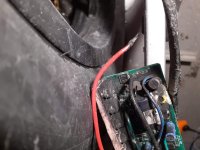
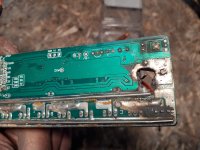
It runs on a 48v 13AH battery. Ito was using the bike in snow, and probably overloaded the controller with stall load. I believe the unit is recoverable with some input from those more familiar because of the way it blew. I turned on the bike, went in for gloves and helmet, and came out to find it powered off.
First thought was that it timed out, but no such luck. No power on to be had. I brought the bike back in the garage, and tinkered with the controller wires. Bad move, as I moved the POS battery wire it let out a shorting sound. I immediately removed the battery. I proceeded to open up the controller and found the POS battery wire was completely disconnected. I blew a hole right thru the PCB. I suspect that no components failed, but the solder joints became overheated, leading to an open circuit. The short only happened when I moved the wire.
My question is
'how is this wire intended to be tied in?'
You can see the capacitor prong,(actually both prongs.) note also that the NEG battery wire has also become unsoldered.
As for the crater left in the board, I was considering a slice of a MIG welder contact tip to slide over the cap prong, then fill - but without bridging across any wrong contacts.
I will be ordering a replacement controller, probably upgrading to a 35 A 1000 watt box, and perhaps an LCD8H. But right now I just need a quick fix.
Seems like a simple fix once connection is confirmed. TIA, Bob
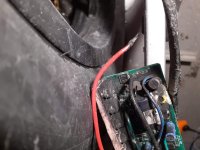
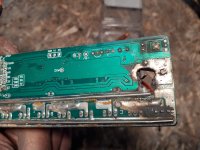