cjr
10 mW
I've been reading and reading and reading... and learning some, have narrowed things down some, but still need some help. I'm looking to build a pedal assist system with the CA3, and a torque sensing bottom bracket to go on a fully suspended trike. I need it to take a 9 gear freewheel or cassette, and I understand that the Q100, Mac 500W, and the Bafang 36v/500W CST will all do one or the other. I am a women in my mid-50s, in decent shape. Seems that my situation is different than many here, I weigh a lot less than most of you, I always pedal, but I need both hill ability and speed. Performance needs are:
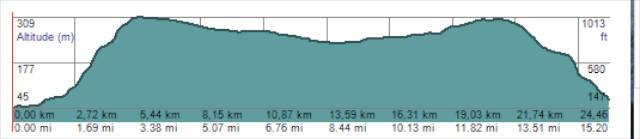
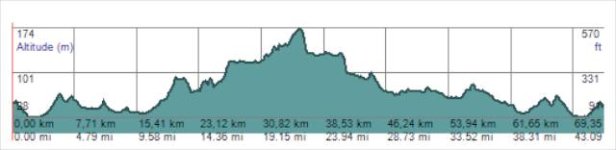
- Weight of trike and rider: 180lbs w/o motor, battery etc. Probably another 5-10lbs of stuff
Provide some assist up to 17MPH on flat windless terrain w/moderate pedaling
Provide some assist up to 25-26MPH with moderate pedaling on slight downhill/tailwind
Able provide some assist and handle a speed of 5-10 mph on a 6% climb for 3 miles, after that it is rolling terrain for the remaining 10-20 miles of that ride.
Normal Range would be 15-35 miles, with perhaps a spare battery for longer rides. Today's ride was 45 miles, but that was about the longest I think we'll be doing anymore. 15-30 miles is more likely.
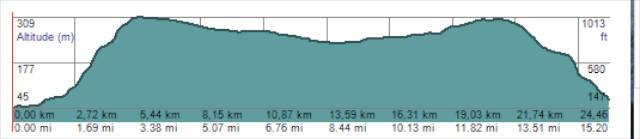
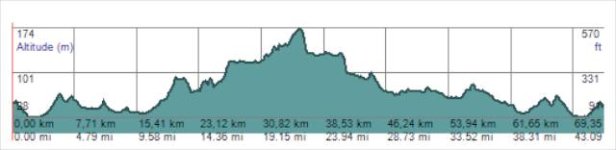