Hey Yall,
I am trying to find high torque, low speed hub motors for my quad bike project. Looking at videos of the mxus 3000, It looks like they spin way faster than I need. i want this buggy to be comfortable climbing hills slowly. Are there any geared hub motors?
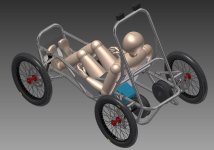
please see picture. And here is my build thread:
https://endless-sphere.com/forums/viewtopic.php?f=10&t=74352
Thank you!
I am trying to find high torque, low speed hub motors for my quad bike project. Looking at videos of the mxus 3000, It looks like they spin way faster than I need. i want this buggy to be comfortable climbing hills slowly. Are there any geared hub motors?
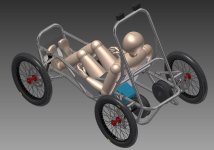
please see picture. And here is my build thread:
https://endless-sphere.com/forums/viewtopic.php?f=10&t=74352
Thank you!