Hardcarve1
100 W
Just though I would share details of my build as I have wanted to convert from my ICE to electric.
I have been using Staton drives on my commuter bikes for a few years now with thousands of K's of trouble free travel. I wanted to do the same with electric but I must have reliabilty as my trip to work and back is 50Km.
Having lots of years behind me in RC heli''s I though may as well go the RC path. I know using RC gear is not as reliable as hubs but the more that work out the problems the quicker we will all be on RC style bikes.
I have been using a NuVinci hub for a while now and find it very reliable and friendly to use and the way Staton mods them to be driven from the gear box I thought I would stay with the setup.
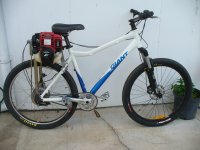
As I only have limited funds each month I have had to progress slowly and while waiting did my design for the gearbox. At first I wall going to mount all the electronics & batteries around the gearbox like this.
View attachment Electric power head.pdf
To make to HXT fit the gearbox I had to make an engine adapter plate that I had laser cut from 5mm aluminium along with a new shaft. The gearbox needed to have the imperial bearings form the old clutch machined to suit the new metric bearings for the shaft. I was lucky to find just the right bearing at VXB.com that did the job.
While I had the motor apart I put new ceramic bearings in as well as epoxy all the magnets in.
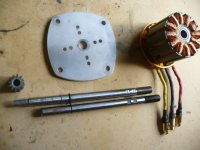
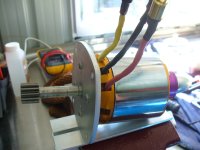
I have been using Staton drives on my commuter bikes for a few years now with thousands of K's of trouble free travel. I wanted to do the same with electric but I must have reliabilty as my trip to work and back is 50Km.
Having lots of years behind me in RC heli''s I though may as well go the RC path. I know using RC gear is not as reliable as hubs but the more that work out the problems the quicker we will all be on RC style bikes.
I have been using a NuVinci hub for a while now and find it very reliable and friendly to use and the way Staton mods them to be driven from the gear box I thought I would stay with the setup.
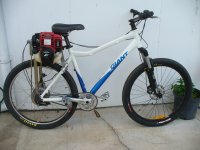
As I only have limited funds each month I have had to progress slowly and while waiting did my design for the gearbox. At first I wall going to mount all the electronics & batteries around the gearbox like this.
View attachment Electric power head.pdf
To make to HXT fit the gearbox I had to make an engine adapter plate that I had laser cut from 5mm aluminium along with a new shaft. The gearbox needed to have the imperial bearings form the old clutch machined to suit the new metric bearings for the shaft. I was lucky to find just the right bearing at VXB.com that did the job.
While I had the motor apart I put new ceramic bearings in as well as epoxy all the magnets in.
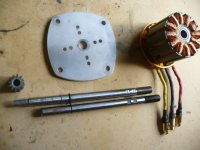
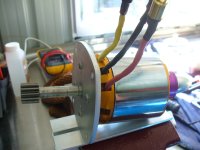