Joey
100 W
This started out as a simple project but has turned into quite a saga. I have decided to document the experience as well as some lessons learned.
My original goal was to build an e-bike starting with (1) a steel-framed hardtail with a decent front suspension, (2) a BMC rear hub motor from EVTECH, and (3) a 36V Headway LiFEPO battery pack from ebikes.ca. I also purchased a stock EVTECH 20A 36V controller and half-twist throttle, but planned to transition to a beefier controller as additional funds became available. As time progressed, the only items that remained from original plan were the bike and hub motor.
The bike I chose is a steel frame Giant Boulder which comes with a 21-speed trigger shifters and v-brakes. I upgraded the front fork to a RockShox Dart 2 and a mechanical disc brake.
I waited a bit too long to order the battery pack (I was saving up funds) so that when I finally placed the order, the only LiFEPO packs left in stock were the dredges. After waiting several weeks, and hearing non-commital statements about continued QC testing, I finally cancelled the order.
I wanted to utilize a battery system with either a proven track record and/or a decent warranty. My first e-bike utilized a eZee hub kit with 36V Li-Mn battery. I has worked very reliably for 900+ miles, but I was beginning to observe a noticeable loss of capacity after 4 months of use on that battery, and it's voltage was sagging significantly toward the end of my daily commute. If I was to stick with a 36V battery I wanted it to be LiFEPO. I was willing to tolerate noticeable voltage sag If I started with a higher voltage, e.g. 48V.
I eventually purchased 8 Milwaukee V28 Li-Mn batteries and four 1-hour chargers from toolup.com. I also purchased a 24-72V 35A Crystalyte analog controller, half-twist throttle, and Cycle Analyst from ebikes.ca. I then checked out jondoh's "milwaukee v28 cable how to video" and purchased eight of the connectors that he recommended and began assembly of Joey's ebike #2. Although I had eight batteries at my disposal, I was only able to fit six of them with connectors in my rear trunk bag.
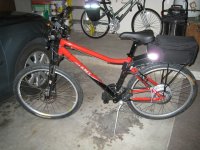
I apologize for the bright reflections in the photo. My camera flash bounced off the reflective stripe on the trunk bag and the pannier on my wife's bicycle in the background.
saga to be continued...
-- Joey
My original goal was to build an e-bike starting with (1) a steel-framed hardtail with a decent front suspension, (2) a BMC rear hub motor from EVTECH, and (3) a 36V Headway LiFEPO battery pack from ebikes.ca. I also purchased a stock EVTECH 20A 36V controller and half-twist throttle, but planned to transition to a beefier controller as additional funds became available. As time progressed, the only items that remained from original plan were the bike and hub motor.
The bike I chose is a steel frame Giant Boulder which comes with a 21-speed trigger shifters and v-brakes. I upgraded the front fork to a RockShox Dart 2 and a mechanical disc brake.
I waited a bit too long to order the battery pack (I was saving up funds) so that when I finally placed the order, the only LiFEPO packs left in stock were the dredges. After waiting several weeks, and hearing non-commital statements about continued QC testing, I finally cancelled the order.
I wanted to utilize a battery system with either a proven track record and/or a decent warranty. My first e-bike utilized a eZee hub kit with 36V Li-Mn battery. I has worked very reliably for 900+ miles, but I was beginning to observe a noticeable loss of capacity after 4 months of use on that battery, and it's voltage was sagging significantly toward the end of my daily commute. If I was to stick with a 36V battery I wanted it to be LiFEPO. I was willing to tolerate noticeable voltage sag If I started with a higher voltage, e.g. 48V.
I eventually purchased 8 Milwaukee V28 Li-Mn batteries and four 1-hour chargers from toolup.com. I also purchased a 24-72V 35A Crystalyte analog controller, half-twist throttle, and Cycle Analyst from ebikes.ca. I then checked out jondoh's "milwaukee v28 cable how to video" and purchased eight of the connectors that he recommended and began assembly of Joey's ebike #2. Although I had eight batteries at my disposal, I was only able to fit six of them with connectors in my rear trunk bag.
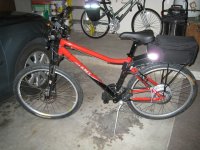
I apologize for the bright reflections in the photo. My camera flash bounced off the reflective stripe on the trunk bag and the pannier on my wife's bicycle in the background.
saga to be continued...
-- Joey