eee291 said:
I welded a 300 Cell Pack with the stock cables just fine.
You need to have the Welder above the Cells, similar to this:
Thanks for sharing, eee291.
Your set-up is a perfect welding station ! Add a pneumatic plunger, it will become a industrial welder.
+ Did you also mod the welding electrodes ? They look thinner. How do they weld ?
+ How thick nickel/copper can you weld with these new set-up of yours ?
+ How many Ah is your lead-acid batt ? How many welds does your battery last ?
Mine is a stationary unit with 6 ultra-caps with PSUs and plugging into wall-outlet. My intention is just a DIY home-use unit. I just don't have time/resource to do a top-notch unit like yours. That's why I ask whether tatus can extend the welding cables. I aware that longer cables might affect higher R & L but tatus should be the one who knows the best about his machine. I just request as a user.
But if needs arise, may be I might follow your footsteps !
spinningmagnets said:
I haven't built this yet, so I'm a little embarrassed to suggest anything, but...Here is my plan for a welder stand. The two arms swing back to store alongside the center platform, so it is easier to store when I'm not using it.
My goals were several. One of them is to make the electrode cables as short as possible, since I want to explore the higher energy levels on the kWeld. Long cables seem to sometimes have an issue with inductance, which I don't really understand.
View attachment 2
spinningmagnets, your design sure looks interesting. Do you have to use 2 hands to push down the 2 welding arms together ? Then when you let go, both arms will swing back up ?
Anyway, I still like the idea of longer welding cable. Another 50-cm longer on each will make a lot of differences to me. I just don't like the welding unit to move since mine is quite bulky with the welder unit, caps bank, 2 PSUs, 2 regulators, heatsink and etc. The existing unit give me a little inconveniences after welding already. You know what I mean...
View attachment 1
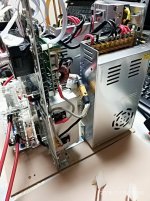