The fact is, kWeld can do the .2 pure nickel well, but ONLY with the supplied electrodes.
My beef with the supplied electrodes is (as good as they weld just after they arrive or you re-dress the tip) lack of repeatability.
For consistent results, electrode gap, pressure and tip shape/size must not vary and it is impossible to achieve this hand-holding them for each weld.
Re-dressing them properly takes a lathe and cannot be done with the electrodes mounted in a welding head because if you file the tip it gets bigger and bigger quite fast.
Speaking of which, I bit the bullet and bought a so-so-quality pneumatic one in the far East (picture below) and installed Sunstone's Copper Glidcop Electrodes EL125BATT. Also tried the next size up they sell.
Now, these electrodes, having a cylindrical shape with flat tips, can very easily be re-dressed to perfection while mounted in the pneumatic head.
Since I have a lathe, I have made electrodes from different copper alloys, of different tip diameters and I am still having trouble with those that produce a good weld nugget because they stick to the weld.
Have tried tungsten of different diameters and sources and played with a wide range of pressure from very light to very strong and everything in between.
The kicker is, if I weld .15 pure nickel with the kWeld (and many of the electrodes mentioned above), I get an excellent weld in a pretty much sticking-free operation.
Aha, you say, it is the thicker .2 strips that are the problem. While this may be indeed the problem, I have purchased 3 different rolls of this material and done both, the salt and grinding wheel spark test and they all appear to be made of pure nickel.
For power source I have purchased the following from Hobbyking:
2 x Turnigy Graphene Panther 5000mAh 3S 75C
4 x Turnigy Bolt 5400mAh 3S 11.4.2V 65~130C
4 x Turnigy nano-tech 5000mah 3S 65~130C Lipo Pack
As well as an Optima Yellow Top Deep Cycle Battery, Group Size 31T, 900 CCA, which I cannot use because it trips the kWeld's over-current protection.
At the end of the day, as I increase the current to my kWeld, the stickiness begins to subside but I can't go past the 2000A built-in protection, hence my asking the question yesterday.
I have a feeling that if I could increase the power to around 2400A I would hit the jackpot and win a perfect, consistent welding nugget.
Now, I am not doing this for a commercial application (I know it sounds like I am) I just like to optimize things and get them as close to perfect as I can. I love the challenge and enjoy the time spent at the shop building stuff and testing it.
You should see the weld head I built from scratch before I purchase the pneumatic one. (I thought that was the component responsible for my troubles but it wasn't)
Plenty more info to provide on this subject if anyone cares to read it: Just ask and I shall respond.
Thanks!
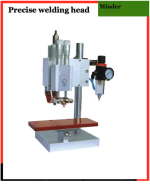