izeman
1 GW
i was working at the motor today, and my colleague didn't take care and after the last hole drilled that drill hit the windings.
i can't say if there is a short (have to measure that), and can't really say if they are weakened a lot.
so if i sealed it with laquer/epoxy and reuse it (after checking for a short) what could i expect? will this winding burn through as it's too thin now for the current running through the motor? or will it run as normal?
the pictures are as good as my DSLR could make them:
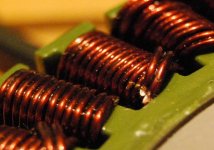
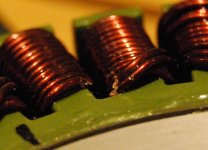
i can't say if there is a short (have to measure that), and can't really say if they are weakened a lot.
so if i sealed it with laquer/epoxy and reuse it (after checking for a short) what could i expect? will this winding burn through as it's too thin now for the current running through the motor? or will it run as normal?
the pictures are as good as my DSLR could make them:
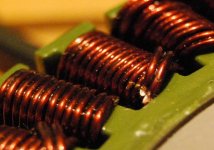
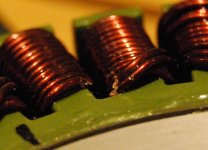