le jamias contente (the Never satisfied) is overdue for a hub motor technology upgrade. it is a 114 years old, the first car to break 100km/h speed record and it was an EV!Let's see, what other configurations might be at least some fun with a 100hp hub?
I would much prefer to drive around in le jamias contente , than that over stylized rubbish red "AERO".
le jamias contente has a wind in the hair, Whylie Coyote sitting on the acme rocket look i prefer and probably similar drag to the AERO.
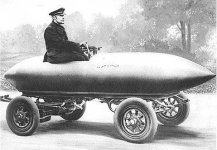
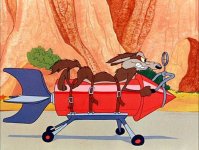
Although lots of unsuspended weight is not ideal, our hub motor bikes rear wheel weighs over 10kg on a 40kg machine or 25%, But to be fair its more like 10kg of unsuspended weight on the rear out of a total of 130kg all up weight and 9" of travel. Motorcross bikes have similar ratios but 12" of travel and they go on some of the bumpiest roads imaginable. So unsuspended weight is not ideal but is an often over stated performance hit, especially in regards to shopping trolley type cars operating on smooth suburban type roads with only 4.5" of suspension travel, full droop to full bump. The ford F series is the biggest selling vehicle, in the worlds largest market for over 30 years! and its stupid(virtually unchanged) live rear end would weigh more than these up scaled bike hub motors. Nascar also uses same junk etc.
Like our bikes cars real estate area is at a premium. Imagine the new design flexibility with no need for an engine bay and radiator grill.(radiators have a drag coefficient of around 1.0 or equivalent to a house brick). I'm not saying hub motors are the ultimate electrically(they have to be bigger than an equivalent high revving geared motor) but it does mean vehicle manufactures can mass produce hub motor corners and bolt them to any body shape.
dg said
We already run abs wires, high pressure hydraulic brake lines etc. and drive shafts. Running some cables is a lot simpler/lighter than running mechanical joints that need to transmit lets see, standard car 300Nm motor, 3:1 1st gear reduction, 4:1 diff gear equals 3600Nm! That has to be heavy/expensive.It also requires running power cable out along the suspension arms where they are exposed and easily damaged. This design seems to create more problems than it solves.
Just some thoughts.
Zappy