John in CR
100 TW
I need to fabricate a swingarm suspension pivot for a current build. I'm using a sealed bearing rear hub with a thick 14mm axle as a motor/pedal power combining jackshaft, and for what I believe a really good reasons, I want to make the rear swingarm pivot around the jackshaft axle. Here's a pic of what I have, but I don't like it, and I need advice.
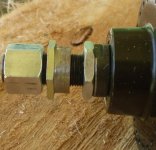
The 14mm axle is threaded with 1mm threads, for which tap and die tools would have to be ordered, and I'd rather avoid the time and expense since this is supposed to be an easy economy build. The swingarm is made from 1/4" steel plate, and the motor along with a bolt on steel piece between the motor and tire will join the 2 arms.
I turned a nut with the lathe into the bushing in the pic, and I was just going to do a metal on greased metal pivot. The nuts, including that longer nut, have a bit of play on the axle, so I see that rapidly becoming a floppy loose pivot and maybe even start as one. The idea of a bushing that threads right onto the axle is now shit canned.
My metalwork experience is limited to a bit of poor welding and lots of grinding, plus a few hours getting to play with a lathe and milling machine, so I've never made anything like a pivot. I haven't even seen many pivots to know a good one vs a poor one. I have 12-15mm of axle to work with at the ends, and both ends are tapped with a threaded hole that looks to be 3 or 4mm and maybe 10mm deep.
My current thought is to turn the axle ends down to 12mm diameter to accept a bearing. If I can find bearings capable of side loads in that small size, then I can install a bolt just beyond the largest sprocket to draw the 2 arms of the swingarm tightly to the bearings. If I can't find such bearing, my next choice would be needle bearings and next roller bearings, and use a bolt with loctite in the axle end hole for a bearing retaining washer. In this latter case I'm unsure what prevents sideways movement through the bearings other than leaving a lip on one side of the arm when I cut the hole for the bearing. Is that one side sufficient?
Any better ideas, suggestions, pitfalls? I'm just looking for longevity and no squeaking with a pivot that has a primary force on it of the motor. If I double up the material of the arms to 1/2" at the pivot, should I just turn and polish the axle and swingarm holes for a metal on metal pivot with grease? Would it be far better to weld some ends onto the axle and fab up something with more like a 1" width and a plastic or rubber bushing like on motorcycle swingarms?
John
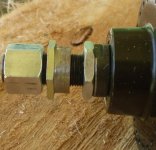
The 14mm axle is threaded with 1mm threads, for which tap and die tools would have to be ordered, and I'd rather avoid the time and expense since this is supposed to be an easy economy build. The swingarm is made from 1/4" steel plate, and the motor along with a bolt on steel piece between the motor and tire will join the 2 arms.
I turned a nut with the lathe into the bushing in the pic, and I was just going to do a metal on greased metal pivot. The nuts, including that longer nut, have a bit of play on the axle, so I see that rapidly becoming a floppy loose pivot and maybe even start as one. The idea of a bushing that threads right onto the axle is now shit canned.
My metalwork experience is limited to a bit of poor welding and lots of grinding, plus a few hours getting to play with a lathe and milling machine, so I've never made anything like a pivot. I haven't even seen many pivots to know a good one vs a poor one. I have 12-15mm of axle to work with at the ends, and both ends are tapped with a threaded hole that looks to be 3 or 4mm and maybe 10mm deep.
My current thought is to turn the axle ends down to 12mm diameter to accept a bearing. If I can find bearings capable of side loads in that small size, then I can install a bolt just beyond the largest sprocket to draw the 2 arms of the swingarm tightly to the bearings. If I can't find such bearing, my next choice would be needle bearings and next roller bearings, and use a bolt with loctite in the axle end hole for a bearing retaining washer. In this latter case I'm unsure what prevents sideways movement through the bearings other than leaving a lip on one side of the arm when I cut the hole for the bearing. Is that one side sufficient?
Any better ideas, suggestions, pitfalls? I'm just looking for longevity and no squeaking with a pivot that has a primary force on it of the motor. If I double up the material of the arms to 1/2" at the pivot, should I just turn and polish the axle and swingarm holes for a metal on metal pivot with grease? Would it be far better to weld some ends onto the axle and fab up something with more like a 1" width and a plastic or rubber bushing like on motorcycle swingarms?
John