Here is my update on > 45mph ebike after 4700 miles. ~4500 on the image with CA below
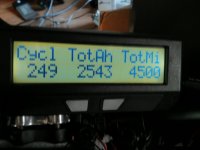
This will be a long post, but I think it is warranted for all those who want to get into this hobby for the long run.
Here is the original build link and It has since then change quite a bit.
http://endless-sphere.com/forums/viewtopic.php?f=4&t=33528&hilit=temperature+K2
Where to start?...
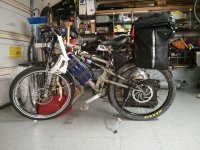
------------------
BATTERY:
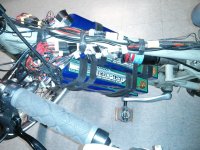
I bought 8 sticks of 10s 25-50C Nanotech back in late 2011. This gave me 74V20Ah battery. I religious charge this pack to 82V (4.1V per cell) and never discharge more than 72V (3.6V per cell) at idle. Moreover, I balance charge EVERY TIME. Balance charging gives me two benefits: 1) The cells are balanced everytime. 2) I get to see which cells are acting up and which cells are fine.
After 1.5 years or so, I can say Lipo is NOT a good battery for the long run. As of now I am at 255 cycles. It is spring now and the batteries are doing a bit better. But in the winter, it sagged from 82V to 76V if I was drawing 50A. Keep in mind, 50A < 3C. Yet this thing was sagging > 0.2V per cell. Totally UNACCEPTABLE! When it was new, it would go from 82V to 79V at 50A and in the cold. Moreover, even with balancing everytime, I now have one weak cell which discharges faster than others. But for some reason, it also come back up faster than the others. In any case, Lipo is NOT the way to go. Look for other chemistry which are still high C but last longer in terms of cycles and usages.
I was hoping to get 10K miles out of this battery before crazy sagging problem. As of now, I don't know how much longer it will last, but capacity is definitely reduced. I use to be able to draw 16Ah out of the pack when new, but now it is more around 13Ah. Summer is coming around and maybe it will help a bit, but who knows. At this rate, I doubt it will help much.
Just for comparison, the specs of these batteries from hobbyking are: 250 cycles or more. Assuming 80% DOD on my 20Ah, this is 16Ah. 16Ah*250 = 4000Ah passing through the battery before it is 80% capacity. Even with the care and maintenance, I am at 2543Ah or a bit more than 1/2 of the batteries specs and it is already giving problems. Meaning their 250 cycles to 80% at 80% DOD is total bull-crap! I suspect similar with other lithium cells. I mean yes they have data on those batteries to prove it, but they do NOT have real-world day to day uses data. Those data can only come when you let user use it over a long period of time.
Here is how I mounted them batteries:
http://endless-sphere.com/forums/viewtopic.php?f=3&t=37597&hilit=battery+mount
Yes yes, I know I should wrap it up, but at this rate, by the time I do, the battery will be shot!
BATTERY conclusion:
If you want something for the long run, Lipo is NOT the way. Some members here might say just keep it between 3.6V and 4.1V per cell and you will be in for the long run. NOPE! You will might get a few more cycles, but not much. And by I mean few, I mean 5-10 cycles! For high power ebikes, voltage sag is everything and once it sags like my battery, it usually means it's time to let it go.
------------------
BIKE FRAME:
This was my 2nd ebike build. The first was a Hybrid bike and at > 30mph speed on USA streets, things started to break down. I wont bore you with the details, but it suffice to know I needed to go to a FS frame.
If you are going to build anything > 20mph and as heavy as an ebike, you definitely need to go FS. Some members might say, it is sufficient to use THICK tires or seat shocks. I say NOPE! You need both and more! Show me a scooter, motorcycles that doesn't have Full Suspension!
Not only do you need Full suspension, you need good torque arms. I wasn't going to risk my body at > 45mph to have my dropout break. So something super thick and mounted properly is required. And if you are running regen you definitely need more insurance. I ended up using what DoctorBass recommended (DP420 black) AND screw holes because without the screw holes, the Epoxy would break during hard regen. Now I have both, the screw holes and the DP420 black to support each other. The DP420 helps the secure the screws which in turns helps the DP420. It is a pretty solid design. So far, >3K miles without incident.
While you are at it, you would need Nord-lock washer. I was using regular washer before and it would keep getting loose after a few rides no matter how hard I twisted it. Now it's bullet proof. I have not since unscrewed my nord-lock 4 months now since the last tire change.
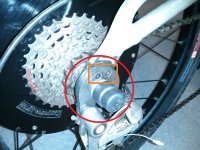
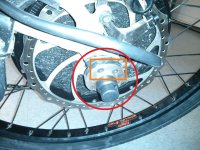
BIKE FRAME Conclusion:
1) GET A FULL SUSPENSION FRAME. Ideally a MTB or Downhill.
2) Get torque arm. A strong one like and bi-directional if you want to run regen and fast acceleration. Some torque arm are only good one direction.
3) Secure the torque very well. Ideally it should never be removed.
4) Get Nord-Lock Washer.
------------------
TIRES:
View attachment 2
One of the worst things that can happen to any ebike is a flat. Though there are solutions out there, they are expensive and might not fit the bill of a high power ebike. Some examples are tubeless tires, carbon struts tires, etc. All of them are expensive and cannot be easily mounted on a hub motor.
So I went ahead and took some advice from few fellow members to put old used tires inside of new tires. But I went a step further.
Currently here are the layers in my bike tires: (Layer 1 is outside, 5 is inside)
1: MAXXIS hookworm 26x2.5
2: Swahable Big Apple Ballon 26x2.15
3: Tuffy 26x2-2.5 Lining
4: SunLite Thorn resistance 26x2.15 tube WITH sealant
5: Double thick rim tape. (essentially using one rim tape or another). <--- This is critical. For some reason Velocity Pyshco rims have this extra elevated center rib which cuts/wear into the tubes. With single rim tape, this caused a flat after a few hundred miles ride. Hopefully the double rim tape and thorn resistance tube helps deals with this problem.
As you can tell, I really hate flats. My ebike is 90lbs with everything on it. Moreover, the battery is exposed so transporting it safely is difficult. Essentially my only hope is to use push it somewhere to repair the tires.
After about 1000 miles with the setup above, I have not had a flat since. I have found many staples, glass shard, etc. punctured in my tires layer 1. But I have not gotten a flat!
TIRES Conclusion:
Make your tires as flat proof as possible. Try what I have above and do more!
------------------
WHEEL:
I got my wheel build at Ilia at ebikessf.com. I don't know if he still is building wheels because he removed that advertisement from his website.
My first motor was built with 13 gauge spoke broke after 2-3K miles due to the way Ilia put them on the rims. He since perfected his method on the physco rims. I then got him to put on 12 gauge spokes on a new motor and I have not a spoke breakage since. Only time will tell if I will get more spoke breakage.
Another thing about rims is make sure it's solid. I have seen other rims break "cough cough Bionx" under stress. Especially if not on a FS frame.
WHEEL Conclusion:
GET 12 Gauge spokes and a downhill rims. Make sure it is build properly. I have heard of stories where people got 12 Gauge spokes but still broke because they had some noob "cough cough crystalyte" put on the spokes. Spend the extra money for less headache down the road.
------------------
MOTOR:
View attachment 1
I originally had the HS3548. It was fast. But the sensors blew and I didn't like running it on a sensorless controller. More about sensorless controller below. Moreover, there were other problems with the wheels. I mean it was the 1st Gen HS3548 so it was bound to have problems. I upgraded to a HS3545 motor also from Ilia. Supposively this one had NSK bearings and Honeywell SS41 sensors. So it should be better. So far, after 2-2.5K miles, I have not had problems since. It is also fast, though not as fast as the HS3548. It also comes with a Temperature probe. I hacked my arduino to get it to work with this temperature sensor. See the following post for the the temperature hack.
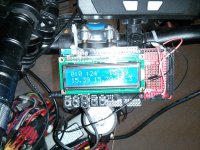
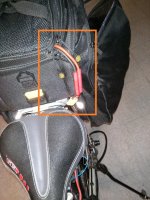
http://endless-sphere.com/forums/viewtopic.php?f=3&t=43442&hilit=+temperature
I guess I could upgrade to Cromotor or the Crystalyte H40xx or the 54xx series. but money is tight these days and the HS3545 has and hopefully will be serving me well for many more miles.
With the temperature feedback, I found the sweet spot for power on flats on my HS3545 is 2-2.5KW power input at 74V. On hills, it is around 1-1.5KW WITHOUT pedal assist and 1.5-2KW WITH pedal assist. Normally the temperature gets to 120 degree C and pretty much settles until I run out of battery. Anymore above those specs listed before will result in burnt motor.
MOTOR Conclusion:
Get the best motor you can afford. Going 45mph or above requires some serious motors. The Cystalyte HS35xx should be the minimum you need to run > 45mph speeds
------------------
CONTROLLER:
I started with the 1st Gen 18FET Lyen controller. I asked Lyen to modify my controller for 74V (20s) or 88.8V (24s) Lipo. Since then, I have only used it on 74V mode. This controller has been flawless since mile 0! I can truly say this controller is one damn good controller. I had a BMC 50V controller and it crapped out on me around 3K miles.
I modified the parameters a bit to make it work at higher settings and got rid of the low-voltage cut off because the CA does this for me. I also enable regen to save my brakes. Since it was modded to handle up to 88V, I was able to regen even when I am at 82V. Normally, if not modded, the regen only kicks in after your battery voltage drops below 79V.
The only problem I ever had with this controller was some capacitor/wire coming loose. Around 4.5K miles, the controller refused to turn on (5V regulator wire was disconnected from joint). I just had to open it up and resolder and glue some parts down. And it works perfectly afterwords. Perhaps even better because before some caps where gone and thus the throttle would be twitchy. Now the startup is much smoother like when it was new.
As reliable as these controllers are, I highly recommend carrying a sensorless controller as a backup. I carry a Crystalyte 12FET 74v-88V sensorless controller as a backup. They are cheap, but can get you out of tough situations. For instance, There was this one time when the sensor blown. I just popped in the sensorless controller and it got me home, albiet slower.
The problem with sensorless controller and high power is it gets hot real fast. At same power input (~1.5KW) the sensorless controller would get much much hotter than the sensored one. Maybe it has to do with my High speed wind motor, but overall sensorless is a pain. Startup is jerky and you need to be moving. Power seems weaker at the same power input... And YES I have calibrated both controller's shunt in the CA. So I know it's similar power inputs.
CONTROLLER CONCLUSION:
Get a decent SENSORED controller. And always invest in a sensorless controller as a backup.
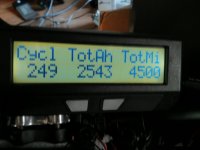
This will be a long post, but I think it is warranted for all those who want to get into this hobby for the long run.
Here is the original build link and It has since then change quite a bit.
http://endless-sphere.com/forums/viewtopic.php?f=4&t=33528&hilit=temperature+K2
Where to start?...
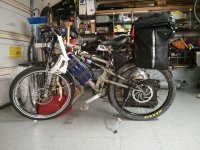
------------------
BATTERY:
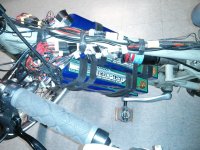
I bought 8 sticks of 10s 25-50C Nanotech back in late 2011. This gave me 74V20Ah battery. I religious charge this pack to 82V (4.1V per cell) and never discharge more than 72V (3.6V per cell) at idle. Moreover, I balance charge EVERY TIME. Balance charging gives me two benefits: 1) The cells are balanced everytime. 2) I get to see which cells are acting up and which cells are fine.
After 1.5 years or so, I can say Lipo is NOT a good battery for the long run. As of now I am at 255 cycles. It is spring now and the batteries are doing a bit better. But in the winter, it sagged from 82V to 76V if I was drawing 50A. Keep in mind, 50A < 3C. Yet this thing was sagging > 0.2V per cell. Totally UNACCEPTABLE! When it was new, it would go from 82V to 79V at 50A and in the cold. Moreover, even with balancing everytime, I now have one weak cell which discharges faster than others. But for some reason, it also come back up faster than the others. In any case, Lipo is NOT the way to go. Look for other chemistry which are still high C but last longer in terms of cycles and usages.
I was hoping to get 10K miles out of this battery before crazy sagging problem. As of now, I don't know how much longer it will last, but capacity is definitely reduced. I use to be able to draw 16Ah out of the pack when new, but now it is more around 13Ah. Summer is coming around and maybe it will help a bit, but who knows. At this rate, I doubt it will help much.
Just for comparison, the specs of these batteries from hobbyking are: 250 cycles or more. Assuming 80% DOD on my 20Ah, this is 16Ah. 16Ah*250 = 4000Ah passing through the battery before it is 80% capacity. Even with the care and maintenance, I am at 2543Ah or a bit more than 1/2 of the batteries specs and it is already giving problems. Meaning their 250 cycles to 80% at 80% DOD is total bull-crap! I suspect similar with other lithium cells. I mean yes they have data on those batteries to prove it, but they do NOT have real-world day to day uses data. Those data can only come when you let user use it over a long period of time.
Here is how I mounted them batteries:
http://endless-sphere.com/forums/viewtopic.php?f=3&t=37597&hilit=battery+mount
Yes yes, I know I should wrap it up, but at this rate, by the time I do, the battery will be shot!
BATTERY conclusion:
If you want something for the long run, Lipo is NOT the way. Some members here might say just keep it between 3.6V and 4.1V per cell and you will be in for the long run. NOPE! You will might get a few more cycles, but not much. And by I mean few, I mean 5-10 cycles! For high power ebikes, voltage sag is everything and once it sags like my battery, it usually means it's time to let it go.
------------------
BIKE FRAME:
This was my 2nd ebike build. The first was a Hybrid bike and at > 30mph speed on USA streets, things started to break down. I wont bore you with the details, but it suffice to know I needed to go to a FS frame.
If you are going to build anything > 20mph and as heavy as an ebike, you definitely need to go FS. Some members might say, it is sufficient to use THICK tires or seat shocks. I say NOPE! You need both and more! Show me a scooter, motorcycles that doesn't have Full Suspension!
Not only do you need Full suspension, you need good torque arms. I wasn't going to risk my body at > 45mph to have my dropout break. So something super thick and mounted properly is required. And if you are running regen you definitely need more insurance. I ended up using what DoctorBass recommended (DP420 black) AND screw holes because without the screw holes, the Epoxy would break during hard regen. Now I have both, the screw holes and the DP420 black to support each other. The DP420 helps the secure the screws which in turns helps the DP420. It is a pretty solid design. So far, >3K miles without incident.
While you are at it, you would need Nord-lock washer. I was using regular washer before and it would keep getting loose after a few rides no matter how hard I twisted it. Now it's bullet proof. I have not since unscrewed my nord-lock 4 months now since the last tire change.
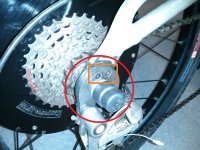
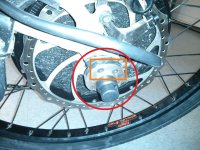
BIKE FRAME Conclusion:
1) GET A FULL SUSPENSION FRAME. Ideally a MTB or Downhill.
2) Get torque arm. A strong one like and bi-directional if you want to run regen and fast acceleration. Some torque arm are only good one direction.
3) Secure the torque very well. Ideally it should never be removed.
4) Get Nord-Lock Washer.
------------------
TIRES:
View attachment 2
One of the worst things that can happen to any ebike is a flat. Though there are solutions out there, they are expensive and might not fit the bill of a high power ebike. Some examples are tubeless tires, carbon struts tires, etc. All of them are expensive and cannot be easily mounted on a hub motor.
So I went ahead and took some advice from few fellow members to put old used tires inside of new tires. But I went a step further.
Currently here are the layers in my bike tires: (Layer 1 is outside, 5 is inside)
1: MAXXIS hookworm 26x2.5
2: Swahable Big Apple Ballon 26x2.15
3: Tuffy 26x2-2.5 Lining
4: SunLite Thorn resistance 26x2.15 tube WITH sealant
5: Double thick rim tape. (essentially using one rim tape or another). <--- This is critical. For some reason Velocity Pyshco rims have this extra elevated center rib which cuts/wear into the tubes. With single rim tape, this caused a flat after a few hundred miles ride. Hopefully the double rim tape and thorn resistance tube helps deals with this problem.
As you can tell, I really hate flats. My ebike is 90lbs with everything on it. Moreover, the battery is exposed so transporting it safely is difficult. Essentially my only hope is to use push it somewhere to repair the tires.
After about 1000 miles with the setup above, I have not had a flat since. I have found many staples, glass shard, etc. punctured in my tires layer 1. But I have not gotten a flat!
TIRES Conclusion:
Make your tires as flat proof as possible. Try what I have above and do more!
------------------
WHEEL:
I got my wheel build at Ilia at ebikessf.com. I don't know if he still is building wheels because he removed that advertisement from his website.
My first motor was built with 13 gauge spoke broke after 2-3K miles due to the way Ilia put them on the rims. He since perfected his method on the physco rims. I then got him to put on 12 gauge spokes on a new motor and I have not a spoke breakage since. Only time will tell if I will get more spoke breakage.
Another thing about rims is make sure it's solid. I have seen other rims break "cough cough Bionx" under stress. Especially if not on a FS frame.
WHEEL Conclusion:
GET 12 Gauge spokes and a downhill rims. Make sure it is build properly. I have heard of stories where people got 12 Gauge spokes but still broke because they had some noob "cough cough crystalyte" put on the spokes. Spend the extra money for less headache down the road.
------------------
MOTOR:
View attachment 1
I originally had the HS3548. It was fast. But the sensors blew and I didn't like running it on a sensorless controller. More about sensorless controller below. Moreover, there were other problems with the wheels. I mean it was the 1st Gen HS3548 so it was bound to have problems. I upgraded to a HS3545 motor also from Ilia. Supposively this one had NSK bearings and Honeywell SS41 sensors. So it should be better. So far, after 2-2.5K miles, I have not had problems since. It is also fast, though not as fast as the HS3548. It also comes with a Temperature probe. I hacked my arduino to get it to work with this temperature sensor. See the following post for the the temperature hack.
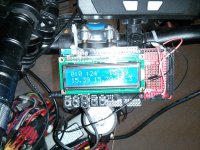
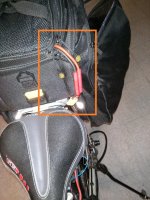
http://endless-sphere.com/forums/viewtopic.php?f=3&t=43442&hilit=+temperature
I guess I could upgrade to Cromotor or the Crystalyte H40xx or the 54xx series. but money is tight these days and the HS3545 has and hopefully will be serving me well for many more miles.
With the temperature feedback, I found the sweet spot for power on flats on my HS3545 is 2-2.5KW power input at 74V. On hills, it is around 1-1.5KW WITHOUT pedal assist and 1.5-2KW WITH pedal assist. Normally the temperature gets to 120 degree C and pretty much settles until I run out of battery. Anymore above those specs listed before will result in burnt motor.
MOTOR Conclusion:
Get the best motor you can afford. Going 45mph or above requires some serious motors. The Cystalyte HS35xx should be the minimum you need to run > 45mph speeds
------------------
CONTROLLER:
I started with the 1st Gen 18FET Lyen controller. I asked Lyen to modify my controller for 74V (20s) or 88.8V (24s) Lipo. Since then, I have only used it on 74V mode. This controller has been flawless since mile 0! I can truly say this controller is one damn good controller. I had a BMC 50V controller and it crapped out on me around 3K miles.
I modified the parameters a bit to make it work at higher settings and got rid of the low-voltage cut off because the CA does this for me. I also enable regen to save my brakes. Since it was modded to handle up to 88V, I was able to regen even when I am at 82V. Normally, if not modded, the regen only kicks in after your battery voltage drops below 79V.
The only problem I ever had with this controller was some capacitor/wire coming loose. Around 4.5K miles, the controller refused to turn on (5V regulator wire was disconnected from joint). I just had to open it up and resolder and glue some parts down. And it works perfectly afterwords. Perhaps even better because before some caps where gone and thus the throttle would be twitchy. Now the startup is much smoother like when it was new.
As reliable as these controllers are, I highly recommend carrying a sensorless controller as a backup. I carry a Crystalyte 12FET 74v-88V sensorless controller as a backup. They are cheap, but can get you out of tough situations. For instance, There was this one time when the sensor blown. I just popped in the sensorless controller and it got me home, albiet slower.
The problem with sensorless controller and high power is it gets hot real fast. At same power input (~1.5KW) the sensorless controller would get much much hotter than the sensored one. Maybe it has to do with my High speed wind motor, but overall sensorless is a pain. Startup is jerky and you need to be moving. Power seems weaker at the same power input... And YES I have calibrated both controller's shunt in the CA. So I know it's similar power inputs.
CONTROLLER CONCLUSION:
Get a decent SENSORED controller. And always invest in a sensorless controller as a backup.