Front Clutch Replacement
I’ve been running with both clutches seized ever since the extended romp with two-motors-as-one about a month ago. I’ll go into the whys and wherefores in a post soon, but they’ve been jammed for several hundred miles. This is not the first time that I have seized the rear clutch but it has always freed itself within 100 miles – but not this time. Pedaling two seized gear motors in DD mode is not huge fun and it's impossible to be stealthy on the bike paths by running one motor because the other is always dragging the rotor rpm up in 1:5 overdrive which is a little noisy. Thankfully, the rear clutch finally freed up of its own accord three days ago, leaving me with just the seized front. Since it was rainy the next day, I seemed a good time to do the repair.
The front motor is a BMC V2S and so has the ‘Green Gears’. I had in hand a replacement V4 ‘Blue Gear’ cluster and a MAC ‘Gray Gear’ cluster. The clusters are interchangeable. All clusters came from Ilia at
Ebikes SF with his usual friendly and speedy service. Here are some shots of the three clusters:
EDIT: clutch gear assemblies from BMC, eZee, and MAC are interchangeable owing to their common heritage...
View attachment 2
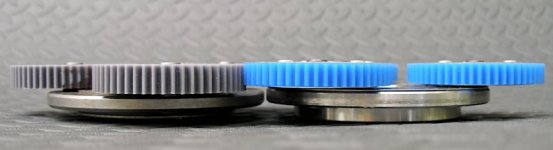
The three clusters use composite gears with different formulations/strengths. The MAC cluster is physically similar to the BMC V2 except that the gears are thicker. Oddly, the BMC ring and sun gears are of sufficient width to drive the MAC planetary gears. The BMC V4 eliminates the riveted components of the earlier design but introduces a plastic cage to retain clutch elements. The single piece design should make the V4 unit more rigid and jam-free than the V2 and MAC clutches but there have been reports of difficulties with the plastic element. The MAC cluster is about half the cost of the BMC V4 version. For no particular reason, I decided to replace the seized BMC Green Cluster with the MAC Gray Cluster.
EDIT: New MAC clutches are similar in design to the BMC V4 clutch and seem to be equally strong. They are a tight fit and relocating one of the gear cluster shims to the outer shaft near the bearing may be a good plan. They can be mounted up normally using the outer circlip.
For simple gear, bearing, and seal maintenance like this, there is no need to disassemble the 'inner motor' assembly which simplifies the service procedure in that there are no magnetic fields to overcome or to cause parts to fly together, nipping at fingers. There are good on-line treatments of disassembling hub motors, so I didn’t bother to take any snapshots. Here’s some references:
The whole process was pretty uneventful, but here’s a few points that might be of interest:
Instead of removing and later re-soldering the phase and hall connectors (Andersons and 5 pin JST), I sliced off the heatshrink and slipped the pins from the plastic shrouds (short curved dental pick for Andersons, thin straight dental pick for JST - (eBay - 'dental pick')). The pins fit easily through the various nuts and washers. Re-assembly just required cutting new heatshrink and refitting the connector shrouds.
Here’s a shot of the ‘inner motor’ from the sun gear side (brake rotor side). Before opening the motor, inspect the shoulder area shown and dress out any burrs/dings before disassembly that will cause binding as the bearing slides off the motor shaft. Do the same to the similar shoulder on the other end of the shaft. A little time on this can save needing a puller to dislodge a jammed bearing. Clean the motor shaft and wipe with a bit of grease/oil so the seals will slide off without damage.
View attachment 7
Here’s a close-up of the gears of the seized cluster. This gear has 2250 miles on it and runs smoothly and quietly. Considering the 1500W 35-40mph speeds and hard starts, I expected some damage - but nothing is visible and the teeth appear uniform and largely unworn. Very encouraging – pretty tough gear...
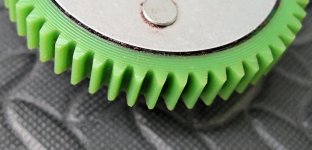
This motor has had a torn oil seal on the brake rotor side since last summer and this was a good opportunity to do a replacement. BMC choose to place the seal in a pocket under the bearing on the inside instead of making it a press-in from the outside. This shrouds the seal on the outside from damage, but necessitates pulling the bearing to change the seal. Removing such small bearings often damages them, so a seal swap is likely to require a bearing replacement as well (both were available on eBay). This motor had been built up from V1 and V2 parts and the hub (V1) had a sealed bearing while the cover plate (V2) had a shielded bearing. The damaged seal was in the hub side, but I replaced the sealed hub bearing with a shielded one since the separate oil seal seemed to make a sealed bearing unnecessary.
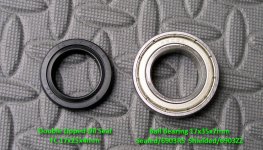
It turns out that the gear cluster shaft key was extremely loose and badly deformed. It appeared about 1mm undersized allowing the cluster to rotate a bit, slamming the key when riding with the clutch seized (regen-like two-directional torque for which it was not designed). Applying the trusty dial caliper to the keyways in the shaft and gear cluster showed a proper size of 5x5x11mm with rounded ends (the shaft keyway was cut with a 5mm end mill leaving the rounded ends). A quick trip to the local Power Equipment Store (snow/lawn care equipment, ATVs, etc - go anyplace that services metric engines) produced a 25mm length of 5x5mm key stock for less than a buck. One end was filed round to fit the recess, the keystock was cut to length, and the other end filed to shape. The new key was shaped with a few degrees of outward taper on the rounded ends so it would jam into the shaft recess snugly when tapped down to seat it. The mating section of shaft was coated with Permatex Anti-Seize Lubricant before sliding the cluster into place over the key and securing it with the snap-ring.
The rest of the reassembly was straightforward. Remember to string washers, nuts, and the torque arm on the wires before re-installing new heatshrink and the plastic connector shrouds.
Here’s some chemicals used in reassembly:
- The Mobilgrease 28 is recommended by BMC and is used to lube the gears: sun, planetaries, and ring. Wipe out the old grease to clear any contaminants.
- The White lithium grease is used to fill and lube the outer oil seals so they will slide down and spin on the shaft without damage or undue wear. The Lubriplate Marine Lube 'A' shown here is no longer available - it appears to have been replaced with Lubriplate Special Marine Grease (available in 14oz cans for under $10). This grease is extremely tacky, does not dry or cake, is salt and fresh water repellent, and retains lubrication properties even at close tolerances. Other greases can be used, but this is a first choice...
- Hylomar AF (Advanced Formulation) is a non-hardening sealant specially designed for machined aluminum components (See Industrial Supply Group). I have never seen this used on hub motors but I’m trying is as a substitute for the various RTV and other sealants commonly used. Hylomar AF stays gooey, requires only a very thin film, and can be cleaned up without solvents. I originally gooped the side cover down with Hylomar 2200 miles ago. When the motor was disassembled this time to replace the clutch, the cover came off easily without a puller, and the old sealant was simply wiped off to the bare metal with paper towel and Simple Green – no scraping, etc. So far, I am really liking this sealant – seals great and makes motor service a breeze.
- When assembling the motor, blue Permatex Threadlocker is squeezed into the hub holes and a VERY thin film of Hylomar put on the cover. The cover is slid down the shaft very close to the hub, the screws inserted and run in half way, then the cover is pressed home. This helps avoid getting sealant on the screw threads where it will interfere with the threadlocker.
- The Permatex Anti-Seize Lubricant is applied sparingly to the shaft before sliding the gear cluster into place.
Here are some tools to pull the motor apart – these or similar can be obtained from Harbor Freight for very reasonable prices:
- The big puller pushes the shaft and opposite cover plate out of the hub. As mentioned above, the Hylomar made this unnecessary this time, although I needed it to break the original RTV sealant loose on the first disassembly last year.
- The small puller is used to pull the gear cluster and can be used to pull a stuck bearing off the shaft. Depending on the tool, you might get away with the big puller for this.
- The bearing/bushing drivers are used to drive the seals and bearing home by applying pressure to the outer race – a full range SAE set is generally usable for metric installations. A properly sized socket is a workable substitute – be careful not to apply force to the inner race of the bearing.
As an alternative, you can break the cage (metal ring that keeps the balls separated) in the old bearing by drilling it, peel out the cage, squish the balls over to one side, and lever out the inner race. The outer race makes a respectable driver for flush mount bearings such as this - and since you always have an old bearing, you always have the right sized driver :wink:. For situations where it is necessary to drive a bearing deeper into a recess below the material surface, just dress down the outer surface of the DIY race driver with emery cloth for a clearance fit into the recess.
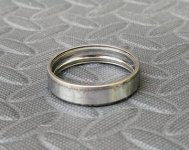
After reassembling the motor and remounting the wheel, I re-aligned the BB7 caliper – took 5 minutes (I
*like* these brakes

).
Fifty miles later all is working fine - the bike rolls easily and silently again (Yahoo!). The MAC gears whir a bit under power, but that’s not unexpected for straight-cut spur gears (and they are wider). I expect they will quiet down a bit when they’ve been run in.
EDIT: Vent Hole
- Okay - it's four years after this original post and I've been in these motors several times replacing clutches and bearings. I pretty much do everything as mentioned above except that I stopped sealing the covers. The Hylomar worked great - but - as Justin pointed out, once water gets in from heating/cooling or other means if will work devilment if it can't get out. I had a couple of instances of popping motors open to find a swamp inside. NFG. As J recommended, I vented the covers. I drilled them with 1/16" holes aligned with the inner case edge so water gets flung out. Since the covers were vented, it seemed pointless to seal the covers to the case, so...
Anyhow, even fording streams with the hubs to the axles, etc and the motors stay nice an dry.
While I was at it, I center punched a small alignment mark on the flange adjacent to the vent hole to make it easy to realign the cover to the case for reassembly
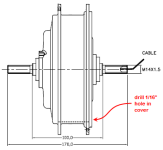