You say I don’t need to change the controller to match the battery - but it seems like I may have to as they are mismatched (90A controller vs 80A Battery BMS). Or?
.
Since I have this very expensive battery and a 1500w motor any advising on how to pick a controller that would work best / better would be appreciated.
Well, it depends on whether or not your controller needs more power than the battery can provide in order to do the job it does for you.
Below are a lot of thoughts that I am too tired to properly consolidate, and I apologize for making it sound more complicated than it is....
Knowing why the system stopped working would help, but unfortunately it's one of those situations where we just can't know unless it fails again and you can trace down why. (if you can draw yourself a complete wiring diagram it will help you trace down any problems you have now or in future).
If it was the battery shutting down it's output because it was overloaded, then you either need a better battery (higher current capability), or a "smaller" controller (lower current demand).
If you change the controller to match the battery's limitation, but the job the trike has to do for you needs more power than a smaller controller could provide, then it won't do the job as well as it would if it just had a battery able to handle the job.
If the controller is programmable, you might be able to just lower it's current limit to what the battery is meant to support. But you'd have to get any software to do that from the controller manufacturer, or from the trike manufacturer, as it will be specific to the controller brand and model, and probably also require a cable to a computer to access. (sometimes these things are accessible via a display that's wired to the controller as part of the system, but may need a password to access, and usualy need a manual to explain the settings as they typically don't have descriptions in the menus, just cryptic abbreviations or parameter numbers and values).
But before any of that: Did the system work fine for your usage and needs, other than range, before the battery swap? How long has been in use in the original configuration?
If so, you don't really need to change anything at all, other than perhaps toning down the current from the controller.
*Or*
if the BMS does shut down the system because of overload (you'll see this during acceleration, on hills, against headwinds, whenever the load on the motor is highest), you may be able to just change out the BMS (or reprogram it if it has that ability),
*if*
the cells can handle the higher load safely. To know that for sure, you have to find out which specific cells they used, and find a datasheet on them from the cell manufacturer.
It is likely that they could handle at least short periods of the higher current, and can probably handle it long term, because most EV-sized cells can continuously handle at least 1C, or 1 x the capacity of the pack, as Amps. Meaning, a 150Ah pack can usually handle at least 150A. Most can handle at least 2C, or 300A in this case. Even if it only does 300A momentarily, and 150A continuously, it is much more than you need.
It is probably only the BMS that is the limiting factor; it's probably just not physically capable of more because of the FETs in it, so it would have a current limit to protect them.
If the battery voltage doesn't sag much even when under the highest load (up to the point the BMS shuts off), the cells can handle the current.
If the voltage sags a lot the higher the load is, they may not be able to handle it, but it depends on how far they sag.
For context, I did run this battery choice by the vehicle and battery manufacturers in China and they both gave the thumbs up FWIW. Lol.
Unfortunately it's not uncommon for the people that "make" these things to not actually know anything about what they are building / selling, because they may not actually be the ones that designed them, and may not know how this stuff works--they may just build it and sell it.
If they did understand how these work, they would not have approved a battery only capable of 80A for a controller that could need to draw 90A.
(They also probably shouldn't use a "1500w" motor for a "2500w" controller that has voltage and current ratings that actually indicate 6500w capability...but it depends on the design intent for the system...if it was only intended for flat roads with no wind and slow speeds it would be ok, but if it has frequent accelerations from a stop or has to climb hills it could take so much power it could overheat the motor if it's really only able to handle that rated power. (this sort of thing with ratings vs actual ability is not a clear-cut exact thing, because not everyone uses the same method for determining the ratings, and some are not even "real" ratings, but just marketing numbers that sound good to them...and you can't know which are, arent', etc).
(They also would not have provided a charger that is that far over the max charging voltage the pack should ever see. But that's something else you still need to recheck, becuase if it does actually reach 73v, you don't want to keep using a charger that is too high a voltage for the pack; there are various failure modes of BMS along with cell aging that could chain in ways that allow significant overcharging of one or more cells.
And they should be concerned that the charger voltage reads that high, and not just blow off the possibility it could be a real reading with the possible consequences)
I’m not looking to go fast, I was just trying to get more range with the upgraded battery.
Well, you probably will, given that while Lithium (used within it's limits) provides it's full capacity for a good long while,
lead doesn't ever even give but maybe half of its' nameplate capacity in this type of usage, and the Ah you had in lead is probably less than what this pack advertises itself as.
Do you think my current controller is fine?
And yeah, the motor is probably way underpowered. Maybe I can upgrade to 2500W with this current controller? Honestly after some initial research I was lost trying to understand which motor to choose / gearing. Not many people have or work on these kind of vehicles!
If the system does what you need it to do, and doesn't give you problems, then you don't need to change anything.
If it does give you problems, then the most detailed description of those you can give, along with what you were doing and under what driving conditions, leading up to it and during the problem, will help us help you find out why
Also more context: this is a very heavy food cart trike. About 1700 lbs. .
Here it is for reference. It’s a coffee truck!
It's slightly bigger than my SB Cruiser heavy-cargo trike.
This thing replaces Delta Tipper...er, Tripper v1.0, whcih was cannibalized to build it. https://endless-sphere.com/forums/viewtopic.php?f=2&t=22720 It's mostly Dogman's fault ;) ...er, inspiration, as he suggested it as a joint build for his trip out here this year. Tiny and Yogi discuss...
endless-sphere.com
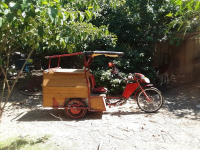
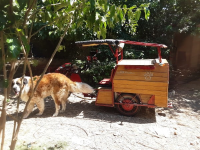
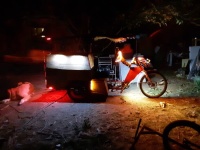
I appreciate the tree-planting (I have a big yard full of them I've been growing the last couple of decades, but this year's summer is so hot for so long they're not doing very well and are taking some severe pruning).
Where do yours get planted?