John in CR
100 TW
Since you want to get a lot out of a little, you'll want to motor temps. For 4 or 5 years I just used the feel my motor with my hand approach after stopping immediately after more and more demanding use...longer steeper hills. That's using much bigger motors, so your much smaller lighter stator will heat quickly, so closer monitoring is necessary. I very highly recommend using a Cycle Analyst V3 from Grin Tech, who pays for our wonderful forum. Once you use a CA you won't even want an EV without it, and a CA3 includes the ability to report temps and even do current limitation based on temp limits you set and thermal shutdown too. You need to plan ahead and get a 10k thermistor to install on your stator...I recommend on the stator instead of stuffed in the windings to avoid reporting of the short spikes that can occur in the copper before the heat moves to the stator steel.
Let me know by PM if you still have heat issues, because I have other ventilatated hubbie cooling ideas that I'm certain will help even though they're no yet proven because I haven't needed more. One thing I did start doing 5 years ago, even before I started using exterior centrifugal blades was to direct more air at my motor. My swingarm has 2 air scoops that direct more air toward the motor. I did it primarily for aesthetics, but functionally they definitely get more air to the motor, which has to help with cooling. I ran 16kw peak pushing my heavy load with a sealed hubbie for a year and a half in a mountainous region without a meltdown, so they sure didn't hurt. Here's the best pics I found on my computer to show what I did.
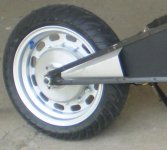
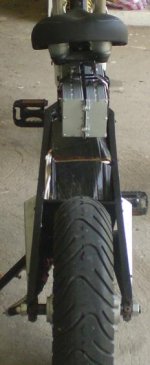
Let me know by PM if you still have heat issues, because I have other ventilatated hubbie cooling ideas that I'm certain will help even though they're no yet proven because I haven't needed more. One thing I did start doing 5 years ago, even before I started using exterior centrifugal blades was to direct more air at my motor. My swingarm has 2 air scoops that direct more air toward the motor. I did it primarily for aesthetics, but functionally they definitely get more air to the motor, which has to help with cooling. I ran 16kw peak pushing my heavy load with a sealed hubbie for a year and a half in a mountainous region without a meltdown, so they sure didn't hurt. Here's the best pics I found on my computer to show what I did.
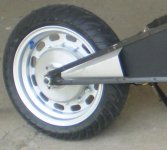
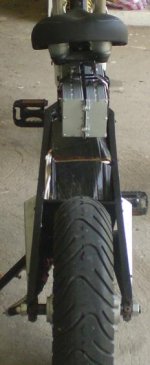