jasonbay13
1 µW
Hi all! i'm new here. below i have several questions and plenty random bits of info.
i'd been using a 36v deck motor from an electric mower but even short distances it would get hot. just a few minutes in the yard would make it hot. gearing had top speed ~30, downhill - no-load wattage was 200w. flat ground 20-25mph was 800-1000w. dont even bother uphill, it turns into a little oven.
being 2 pole, wouldnt that mean the motor would be most efficient at ~3600rpm depending on steel lamination thickness? i believe it was wired in lap winding with 28 comm bars and 28 slots 6 turn 1mm wire. the gap between rotor and magnet seems pretty big IMO and the thickness of the magnet puts even more distance from the rotor field to the back-metal, which if i read correctly reduces efficiency. but also brings me to the question as to how drone motors spin up to such high speeds and retain efficiency; is it the use of aircraft steel (even smaller laminations)?
i want to re-wind the motor and have the wire to do it but i'm unsure as to what actual differences there are of how i wire it. one book from the 20's i was reading said wave winding was impossible on a 2 pole motor but the internet now doesnt know from a quick google search.
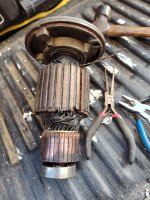

i got a 350w rated hub motor from a friend that i put new wires on after coming loose and ripping them to shreds. it now resides on the front of my transport and i have it hooked to a sensorless amazon controller. it works well enough to get me to the dentist with only a warm hub and nearly cold controller. it has 6w no-load draw and the most i can get out of the controller is ~1kw peak. what would cause the efficiency difference to be so big between a big heavy motor that doesnt have the oomph to get me up a hill without melting and a light hub motor rated at 350w able to power me up about as well?
weird thing happens with it though, if i give it too much load it will cut out entirely then start up again and if it hits the load too hard it cuts over and over. is that normal? sensorless operation? it also cuts out at 49v though it has written on it 36/48/72v clearly set for 72v range...
isnt the most efficient rpm the one that is equal to a formula that accounts the poles per phase and rpm to frequency that corresponds with the steel laminations?
and then isnt the air-core motors completely free of the burden on frequency-related inefficiencies? but if the tesla force provided by one watt is less in an air-core than a steel core, i'm confused.
about the speed of the hub motor, it seems to be 3600erpm relating to a rpm ~270. the controller has a speed selector switch and low does limit the speed some. i find that when on high i am unable to notice a difference except in the consumed wattage. flipping while on flat ground the wattage drops by as much as 200w. is that extra 200w actually being used to propel me and i just cant tell the extra 30% of power due to the part where it takes 4x as much power to go twice the speed? or is it decreasing the efficiency and turning into heat more than work?
on the topic of building my own motor i had bought 18 20x40 cylindrical neodymium magnets and was hoping they could be used in an axial-flux prototype, but i think i would need a lot more of them to make anything usable.
hopefully i've posted in the right place, and not to be too coherent-writing-nazi on me
thanks!
p.s.
also looking for good sources of motor and electronics information. almost everything i can find is from india or bulgeria and not in english and filled with wrong or bad info as found out by personal failures and doing thorough research on the specifics. the two books i found from the 20's and 40's have so much information in one place it's almost like i've discovered the internet! except the info in these books isnt readily available anywhere in a coherent manner on the internet that i've found.
i'd been using a 36v deck motor from an electric mower but even short distances it would get hot. just a few minutes in the yard would make it hot. gearing had top speed ~30, downhill - no-load wattage was 200w. flat ground 20-25mph was 800-1000w. dont even bother uphill, it turns into a little oven.
being 2 pole, wouldnt that mean the motor would be most efficient at ~3600rpm depending on steel lamination thickness? i believe it was wired in lap winding with 28 comm bars and 28 slots 6 turn 1mm wire. the gap between rotor and magnet seems pretty big IMO and the thickness of the magnet puts even more distance from the rotor field to the back-metal, which if i read correctly reduces efficiency. but also brings me to the question as to how drone motors spin up to such high speeds and retain efficiency; is it the use of aircraft steel (even smaller laminations)?
i want to re-wind the motor and have the wire to do it but i'm unsure as to what actual differences there are of how i wire it. one book from the 20's i was reading said wave winding was impossible on a 2 pole motor but the internet now doesnt know from a quick google search.
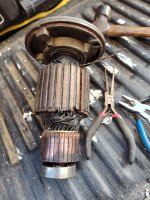

i got a 350w rated hub motor from a friend that i put new wires on after coming loose and ripping them to shreds. it now resides on the front of my transport and i have it hooked to a sensorless amazon controller. it works well enough to get me to the dentist with only a warm hub and nearly cold controller. it has 6w no-load draw and the most i can get out of the controller is ~1kw peak. what would cause the efficiency difference to be so big between a big heavy motor that doesnt have the oomph to get me up a hill without melting and a light hub motor rated at 350w able to power me up about as well?
weird thing happens with it though, if i give it too much load it will cut out entirely then start up again and if it hits the load too hard it cuts over and over. is that normal? sensorless operation? it also cuts out at 49v though it has written on it 36/48/72v clearly set for 72v range...
isnt the most efficient rpm the one that is equal to a formula that accounts the poles per phase and rpm to frequency that corresponds with the steel laminations?
and then isnt the air-core motors completely free of the burden on frequency-related inefficiencies? but if the tesla force provided by one watt is less in an air-core than a steel core, i'm confused.
about the speed of the hub motor, it seems to be 3600erpm relating to a rpm ~270. the controller has a speed selector switch and low does limit the speed some. i find that when on high i am unable to notice a difference except in the consumed wattage. flipping while on flat ground the wattage drops by as much as 200w. is that extra 200w actually being used to propel me and i just cant tell the extra 30% of power due to the part where it takes 4x as much power to go twice the speed? or is it decreasing the efficiency and turning into heat more than work?
on the topic of building my own motor i had bought 18 20x40 cylindrical neodymium magnets and was hoping they could be used in an axial-flux prototype, but i think i would need a lot more of them to make anything usable.
hopefully i've posted in the right place, and not to be too coherent-writing-nazi on me
p.s.
also looking for good sources of motor and electronics information. almost everything i can find is from india or bulgeria and not in english and filled with wrong or bad info as found out by personal failures and doing thorough research on the specifics. the two books i found from the 20's and 40's have so much information in one place it's almost like i've discovered the internet! except the info in these books isnt readily available anywhere in a coherent manner on the internet that i've found.