Mouse
1 mW
- Joined
- Jul 2, 2020
- Messages
- 19
Starting a conversion of a Chinese 125
Main Components are,
Direct Bikes 125cc Enduro
Two 48V 60Ah 2.8kWh 13s20p 18650 server backup battery packs.
Two 2kW Eltek Flatpack2 48V battery chargers.
Honda IMA IPU motor controler
Honda IMA flywheel motor, approx 20hp
I'm working to a very limited budget so almost all parts are used and some even come from the scrap pile.
The battery packs are very well built so I'm going to keep them as they are unless it is simply not possible to mount them sensibly. I'm hoping the batteries are actually good and give a fair proportion of their marked 2.8kWh (5.6kWh total). The batteries will be in series making a 96V 26s20p pack which leaves limited options for BMS systems. I've been experimenting with the diyBMS system https://github.com/stuartpittaway/diyBMSv4 which is really intended for power wall applications but is expandable and fully open source which I like. As the batteries will be in parallel and producing around 100V I will also have to be more careful with weather protection and insulation so will probably make an aluminium housing for the battery pack and power electronics.
I'm intending to use the Honda IMA power unit + motor with a Field Oriented Control FOC module / code developed by Johannes Hubner and Damien Maguire over at https://openinverter.org/forum/ which is also an open source project.
The biggest task at the moment is to make up some end plates for the motor as it comes without them.
As the chargers are capable of charging at 4kW which on a 5.6kWh battery is in the realms of fast charging so the end goal is to also have a Type 2 EV charge socket so I can travel further than the return range will allow and use roadside charge points.
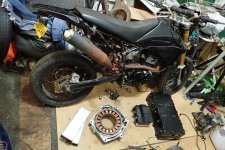
Main Components are,
Direct Bikes 125cc Enduro
Two 48V 60Ah 2.8kWh 13s20p 18650 server backup battery packs.
Two 2kW Eltek Flatpack2 48V battery chargers.
Honda IMA IPU motor controler
Honda IMA flywheel motor, approx 20hp
I'm working to a very limited budget so almost all parts are used and some even come from the scrap pile.
The battery packs are very well built so I'm going to keep them as they are unless it is simply not possible to mount them sensibly. I'm hoping the batteries are actually good and give a fair proportion of their marked 2.8kWh (5.6kWh total). The batteries will be in series making a 96V 26s20p pack which leaves limited options for BMS systems. I've been experimenting with the diyBMS system https://github.com/stuartpittaway/diyBMSv4 which is really intended for power wall applications but is expandable and fully open source which I like. As the batteries will be in parallel and producing around 100V I will also have to be more careful with weather protection and insulation so will probably make an aluminium housing for the battery pack and power electronics.
I'm intending to use the Honda IMA power unit + motor with a Field Oriented Control FOC module / code developed by Johannes Hubner and Damien Maguire over at https://openinverter.org/forum/ which is also an open source project.
The biggest task at the moment is to make up some end plates for the motor as it comes without them.
As the chargers are capable of charging at 4kW which on a 5.6kWh battery is in the realms of fast charging so the end goal is to also have a Type 2 EV charge socket so I can travel further than the return range will allow and use roadside charge points.
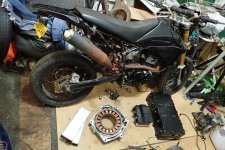