Well, it's been quite some time but I've picked up this project again a few weeks ago. As I was the one originally bringing up the Intersil chip, I thought I'd at least report my progress.
I've just ordered the revision 2 boards from OSH Park. 3 boards for US$20 shipped free world-wide is a bargain! Here are the top and bottom side renderings of the BMS node board. The PCB measures 42x50 mm, so 3.25 sq. in.
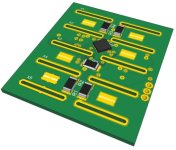
My system is designed to work with the LiPo pouch cells you can get from HobbyKing (5000mAh). The board is designed for a 5S/2P configuration with the cells sitting on either side of the board. Like this:
The tabs of the cells go through the slots in the board and get soldered together. The complete assembly is designed to then slide into extruded aluminium box profile, ending up with a battery 5S/10Ah module of roughly 300x55x45 mm. I use two of these mounted to the down tube of my e-bike. The connections are + and -, and a comms connection for daisy chaining modules together in series.
The software and PCB are working and these rev 2 boards have the changes from testing of the rev 1 boards. U1 is the Intersil chip and U3 is the PIC24 micro. I haven't added all the costs but including the PCB it should come in at a shade over US$10, which is not bad.
The summary features are:
- 5-cells in series, either LiPo or LiFePo4, 1P of 2P
- Auto-balancing with every charge
- LVC and HVC alarms (via comms)
- One temperature sensor per side of 5 cell pack, plus PCB temp sensor
- Optically isolated serial communication for daisy-chaining to master module, which controls the charging process
- No shunt resistors, i.e. discharge current is not monitored
- Stand-by current of less than 5uA per cell
Hopefully, I'll have the rev 2 boards back from OSH Park in a couple of weeks and will be assembling and testing them.