YoshiMoshi
10 W
I took a look into Matador's excel sheet. Some of the math I was able to conclude where it came from, but most of it I was.
I'm using the following spot welder:
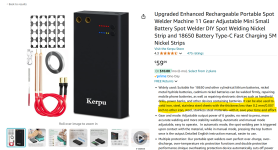
Would I be able to use this spot welder to spot weld 0.1 mm thick nickel strip and 0.1 mm thick copper strip together to a 21700 cell, and then sandwich another sandwiches ontop of this?
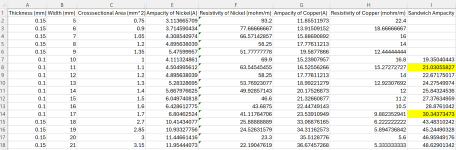
It looks like 0.1 mm thick nickel that is 11 mm wide and 0.1 mm thick copper that is 11 mm wide can be spot welded together to give me a total ampacity of ~21 A. I can then spot weld two additional sandwhiches together to give me 3 copper strips and 3 nickel strips spot welded to a cell, giving me an ampacity of about 63 A?
Is there a better way to do this? Thanks for any help!
1) Place 0.1 mm x 11 mm copper strip ontop of cell.
2) Place 0.1 mm x 11 mm nickel strip ontop of the copper strip
3) Spot weld the two strips of metal ontop of the battery.
4) Place 0.1 mm x 11 mm copper strip ontop of nickel strip.
5) Place 0.1 mm x 11 mm nickel strip ontop of the copper strip
6) Spot weld the sandwich to the other sandwich
7) Place 0.1 mm x 11 mm copper strip ontop of nickel strip.
8) Place 0.1 mm x 11 mm nickel strip ontop of the copper strip
9) Spot weld the sandwich to the other sandwich
I'm using the following spot welder:
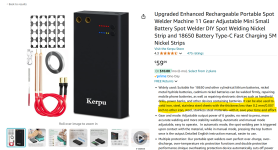
Would I be able to use this spot welder to spot weld 0.1 mm thick nickel strip and 0.1 mm thick copper strip together to a 21700 cell, and then sandwich another sandwiches ontop of this?
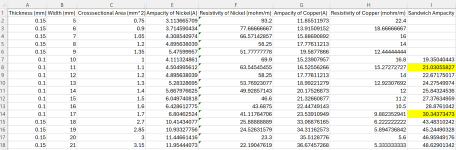
It looks like 0.1 mm thick nickel that is 11 mm wide and 0.1 mm thick copper that is 11 mm wide can be spot welded together to give me a total ampacity of ~21 A. I can then spot weld two additional sandwhiches together to give me 3 copper strips and 3 nickel strips spot welded to a cell, giving me an ampacity of about 63 A?
Is there a better way to do this? Thanks for any help!
1) Place 0.1 mm x 11 mm copper strip ontop of cell.
2) Place 0.1 mm x 11 mm nickel strip ontop of the copper strip
3) Spot weld the two strips of metal ontop of the battery.
4) Place 0.1 mm x 11 mm copper strip ontop of nickel strip.
5) Place 0.1 mm x 11 mm nickel strip ontop of the copper strip
6) Spot weld the sandwich to the other sandwich
7) Place 0.1 mm x 11 mm copper strip ontop of nickel strip.
8) Place 0.1 mm x 11 mm nickel strip ontop of the copper strip
9) Spot weld the sandwich to the other sandwich