Here's some details on my set-up
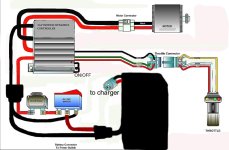
you can look at the previous photos of fried wiring to see where they fit into the scheme. This is the controller set up
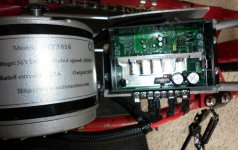
disregard the info on the motor label.
I'm not sure of the amp draw on the battery/motor/controller as I've not been able to measure accurately with the knowledge I possess on electronics. I know how to get a reading on the voltage from the battery using a multimeter, but to get a reading of amp draw while the motor is under full strain (when I'm on the bike!) and without a cycle analyst is beyond my abilities. Here's what the set-up on the bike without the battery attached underneath looks like,
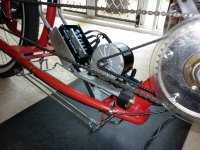
. and this is the bike all in one piece.
The battery voltage when fully charged is around 41V I need to get a bit of a tutorial on how to do an accurate reading of amp draw on battery, cell voltage, and how to set up an on-board meter (other than cycle analyst) that shows amp current draw, remaining amp hours left in battery...etc. I have that small meter that I've used in my charging set up but I couldn't work out how to use it for a monitor on the bike in motion. I have to go to work but let me know what else might be helpful to tell you about the set up and I'll post more when I come home tonight. Thanks and sorry about my limited knowledge, I'm always willing to have a go at things just to test myself and see if I can pull it off, this bike has been in my head waiting to come out for a very long time so I want to at least try to get it right.
Well I'm back in from work and got some info from the website about the motor, this was all they had on the Unite 24V 350W
No-load currency/A ≤2.0/1.4
No-load rate speed /rpm 3450
Rating Torque/N•m 1.22
Rating speed /rpm 2750
Rating currency/A ≤18.7/12.5
Efficiency/% ≥78
Motion Dynamics Controller specifications
12V-48V Input Voltage (Battery Bank) 12V-55V (Regulated Power Supply ONLY!)
•High Quality Aluminium casing!
• 0-100% Speed Regulation!
• Constant torque with Pulse Width Modulation (PWM)
• High Quality Industrial Design
• Efficient High Voltage Regulator
• On/Off Switch (Built in!)
• 3 Soft start settings (Off, Slow, Slower) ramps up to the desired speed once the controller is switched on, and unlike cheap controllers every time you switch it off and on (using the switch) it will ramp up to speed again!
• Max Current up to 100A* (25A model burst rate = 50A and 50A model burst rate = 100A for SHORT periods)
•25A or 50A Continuous duty
•2 Oz Double Sided PCB
• High Speed Mosfet driver averaging 1.6uS opening/closing times
• High Current 180A Mosfets with worlds lowest RDS On in TO-220!
• Low Battery Voltage cut-out (for 12V, 24V and 36V)
• Adjustable Frequency From 300Hz to 1.5Khz
Hope this helps to establish a clearer view of the set up, battery is as mentioned in previous post a 36V - 12 AH LiFepo4 from BMS batteries.
Regards
Hiconic