John in CR
100 TW
I finally got to put the new approach I tried on Hubmonster to the test with a mountain climb. It's a several mile route my son has shared with videos in the pics and videos section with his Clown Bike. He'll post a video of today's ride later, but to summarize I averaged 156wh/mile hitting a max speed of 59mph on what is a continuous climb other than one short dip. The upper half is the steepest with one 30% section that I stopped at the foot and accelerated up, and one stretch of over half a mile is a steady 18% grade. It's quite curvy so I was braking and accelerating repeatedly, so the load was harder than race conditions, and I hit the peak battery current of 220A after many of the curves with a minimum voltage of 74.9V, so 16.5kw pumping into the motor. In comparison, Zombiess's bike won the SoCal race consuming 88wh/mile.
The cooling effectiveness astounded me, because when we stopped at the top magnet backing ring was only 37°C and the stator couldn't have been much warmer, if at all, because there was no warm air was rising out of the exhaust holes. The covers themselves were cooler, though not quite the ambient of 22°C like the rest of the bike.
All my other ventilation attempts used perimeter exhaust holes in both covers. With Hubmonster I wanted to get more air flow through the magnetic gap due to the wide stator of 50mm. My approach was simply intake on one side, exhaust out of the other side with blades near the stator in both covers. The blades serve several purposes:
1. Ensure that the air inside the motor is spinning at full motor rpm.
2. Prevent the easiest air flow path along the smooth unobstructed side covers where it does no good by deflecting the spinning flow of air away from the cover directly at the stator where it is needed the most. This creates a more turbulent flow at the stator, and much better cooling...like blowing air into you bowl of hot soup instead of blowing across the top from the side.
Since I ride on the road at speed, this approach works fine with this large diameter motor (stator 265mm). It barely gets warm with plenty of full stop and slow speed launches, which are the hardest in terms of heat. Once I get a controller that can go to 300A, which this motor can definitely handle, if it gets warmer than I like when I go around hunting for motorcycles to embarass, I'll first add a cowling to funnel air at the intake, and if that's not enough I'll add a ring of larger intake holes for a less restrictive intake, go to 15 blades in each cover, and enlarge the exhaust holes, so I do have an upgrade path if it proves necessary at over 20kw.
Here are pics of the side covers. Note that the blades almost touch the stator. In fact, I had to open the motor twice when I first put it back together to bend some blades flatter that were rubbing against the widest point on the stator end-windings. The blades are both bolted and epoxied to prevent them from either coming loose and rattling or coming off completely and ruining the motor. The holes are angled, forward at the top of the rotation to "bite" into the air better for the left side intake holes in the thick part of the cover near the bearing, and rearward when furthest from the road for the exhaust holes at the extreme perimeter of the right side cover to minimize the outside influences on the natural centrifugal flow resulting from the air spinning inside the motor. Air has mass, so just like a ball on a string if you spin them in a circle, centrifugal force pushes them outward trying to escape their confines.
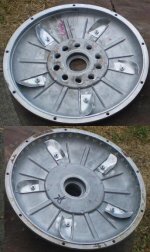
Click on the pic below and click again to enlarge to see more detail:
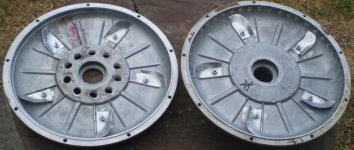
The bottom line is that this approach works quite well, and even better than on the motor on my son's ebike, since his motor was warm (not hot, but markedly warm) at the magnet ring when we stopped at the top. That motor wasn't pushed into saturation either, and though it is a 200mm diameter motor, his has blades and larger holes, but with one side intake and dual side exhaust, so his doesn't get much flow at all through the magnetic gap. With much larger blades and hole, I wouldn't doubt that his flows more air, just not where it's needed the very most, so this new method is what I'm sticking with from now on. Maybe once I start doing some much slower off-road riding I'll find a need for going with active ventilation, but I'll cross that bridge when I get to it.
John
The cooling effectiveness astounded me, because when we stopped at the top magnet backing ring was only 37°C and the stator couldn't have been much warmer, if at all, because there was no warm air was rising out of the exhaust holes. The covers themselves were cooler, though not quite the ambient of 22°C like the rest of the bike.
All my other ventilation attempts used perimeter exhaust holes in both covers. With Hubmonster I wanted to get more air flow through the magnetic gap due to the wide stator of 50mm. My approach was simply intake on one side, exhaust out of the other side with blades near the stator in both covers. The blades serve several purposes:
1. Ensure that the air inside the motor is spinning at full motor rpm.
2. Prevent the easiest air flow path along the smooth unobstructed side covers where it does no good by deflecting the spinning flow of air away from the cover directly at the stator where it is needed the most. This creates a more turbulent flow at the stator, and much better cooling...like blowing air into you bowl of hot soup instead of blowing across the top from the side.
Since I ride on the road at speed, this approach works fine with this large diameter motor (stator 265mm). It barely gets warm with plenty of full stop and slow speed launches, which are the hardest in terms of heat. Once I get a controller that can go to 300A, which this motor can definitely handle, if it gets warmer than I like when I go around hunting for motorcycles to embarass, I'll first add a cowling to funnel air at the intake, and if that's not enough I'll add a ring of larger intake holes for a less restrictive intake, go to 15 blades in each cover, and enlarge the exhaust holes, so I do have an upgrade path if it proves necessary at over 20kw.
Here are pics of the side covers. Note that the blades almost touch the stator. In fact, I had to open the motor twice when I first put it back together to bend some blades flatter that were rubbing against the widest point on the stator end-windings. The blades are both bolted and epoxied to prevent them from either coming loose and rattling or coming off completely and ruining the motor. The holes are angled, forward at the top of the rotation to "bite" into the air better for the left side intake holes in the thick part of the cover near the bearing, and rearward when furthest from the road for the exhaust holes at the extreme perimeter of the right side cover to minimize the outside influences on the natural centrifugal flow resulting from the air spinning inside the motor. Air has mass, so just like a ball on a string if you spin them in a circle, centrifugal force pushes them outward trying to escape their confines.
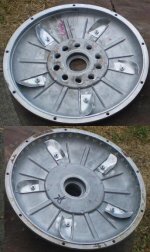
Click on the pic below and click again to enlarge to see more detail:
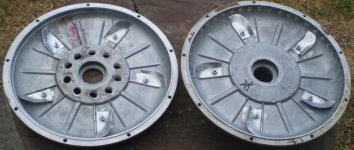
The bottom line is that this approach works quite well, and even better than on the motor on my son's ebike, since his motor was warm (not hot, but markedly warm) at the magnet ring when we stopped at the top. That motor wasn't pushed into saturation either, and though it is a 200mm diameter motor, his has blades and larger holes, but with one side intake and dual side exhaust, so his doesn't get much flow at all through the magnetic gap. With much larger blades and hole, I wouldn't doubt that his flows more air, just not where it's needed the very most, so this new method is what I'm sticking with from now on. Maybe once I start doing some much slower off-road riding I'll find a need for going with active ventilation, but I'll cross that bridge when I get to it.
John