Its Alive!
I emailed Steven at Kelly Controller about my throttle issue. As usual, his response was quick and complete - one of the many things I like about using Kelly products.
He said that I should modify my PB6 with a third wire to 5v (J2 pin 7) to convert it a 0-5v throttle. The controller does support a 2-wire throttle, with a 1k resistor, but it is “less preferred."
So, I opened the PB6 case. I thought I was going to have to mess with the return spring to get at the pot, but that assembly remained intact. Naturally, the center connector is the wiper, and the two end connectors are the + or -. The '+' end is the open pin in the first picture, so I soldered a red wire to it. When I soldered the PB6 yesterday, I connected the black wire to ground - to me, ground is always negative.
In a resistance pot setup it the ends don't really matter, but in a 0-5v it setup it obviously does. I had a 50/50 chance of wiring it correctly, but once I opened the pot, I could see that the wiper was wired to black, and the negative side was wired to white. Rather than undo all my other work, I swapped the white and black wires at the pot (as seen in the 2nd photo). Besides being easier, it is more intuitive for me in the future.
That said, I took the new control harness outside and hooked up everything but the contactor so the controller wouldn't spin the motor at power-on - I left it programmed in 5-0 mode last night. I reprogrammed the controller to 0-5 mode and re-enabled the high-pedal cutoff. The motor now responds to the throttle! I put it in reverse, gradually added the throttle, and the bus lurched backwards with far more torque than I expected for 53v, more bite than I remember from the ICE. Of course, it could well have been supplying 25kw (50vx500a), 33 electric horsepower, and the ICE was 66hp. I am eager to see how it performs on the street, but I have more to do to make it roadworthy.
Having it MOVE in a controlled fashion is a major milestone for me. To be honest, I have been
stressed out about this project since I started. I have been absorbing tons of information, found out I didn't know half of what I thought I knew, and was concerned that I would miss something important or trash something or hit a roadblock beyond my skills.
The motor part really concerned me - I've never even handled a clutch or flywheel before, and if I had hit a problem (something doesn't fit, etc) I don't have the skills or tools to fix it. Ultimately the motor was the easiest part of the whole installation, everything just bolted on.
The rear-engine aircooled VW configuration compliments an electric motor installation very well, I bypassed many of the hurdles one would face converting a more modern car with a front-engine layout. I should give credit to the CanEv kit for simplifying the process too; I was considering another kit that uses a taper lock that had a lot of precision adjustments that I think were beyond my skill set, and the CanEv simply bolted on.
One must be vigilant about things including high-voltage issues, working with heavy masses, and keeping the driveline disengaged (be aware of the risks, do your homework to be safe),
but with that in mind I would like to pass on to others: if you have ebikes down, converting an aircooled VW to electric is easily within your skill set. I did every single element of this conversion single handed, the only help I needed was torquing the flywheel bolts and my 5' 100lb wife helped with that. Most of the tasks here are things I never tried before.
The next step was charging. I bought (7) brand-new Vicor power supplies (as recommended by Dr. Bass - thanks for yet ANOTHER great tip Doc!). I got that many because they were new, dirt cheap, and all 8 slots filled with 48v4.2a subchargers, capable of 33.6a when paralleled! I thought these would be a nice compliment to the 48v-3.7v DC-DC converters I bought here fore single-cell chargers. I'll still use those as balancers in the future, but for now I'll charge the cells directly with one of these. The modules were all turned down to 30v, but the set screw allowed me to adjust them up to 56.2v. I tuned them to 52.8v to charge 16 cells to 3.3v/cell. By combining the 8 sub-modules in parallel and series, and adjusting set screws, I can hit any target voltage from a single charger, no matter how I configure the pack. It will only supply 1200w at 120v AC, so the higher the pack voltage the slower the charge.
So, tomorrow I hope to pump some juice into the cells, and get started on the Vacuum pump/reservoir to assist the brakes. After that, I'll mount the PB6 to the throttle cable (with a separate return spring). Then I'll work a permanent aluminum-plate mounting for the controller and the Jumbo-Screen Cycleanalyst I've had in storage. Then this will be ready for basic road testing to see how many watts/mile this uses to size the final battery pack. Then I am ready for the final, permanent install of all systems.
But today, today it moves!
-JD
NOTE: THESE ARE THE RAMBLINGS OF A RANK AMATEUR ON HIS FIRST EV CONVERSION JOURNEY - LISTEN AT YOUR OWN PERIL.
View attachment 1
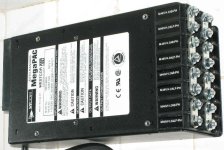