Gregzouz
1 mW
Hello everybody,
I'm Greg from French Alps.
I come to this forum to present to you my build project based on a dirty KTM 450 SXF from 2009 bought 900€ without motor.
The swap consist of :
- motor QS138 70H V3 with installation of the 3SHUL encoder kit
- ESC 3SHUL CL700
- DOMINO throttle
- homemade battery build with :
* NMC Li-Ion cells from CALB with threaded studs on copper 60mm² bus bars
* 89 V nominal (24S1P)
* 58 Ah
* 5150 Wh
* 110 A continuous
* 350 A peak
* ANT BMS
* aluminium plates casing
- RAGE MECHANICS Smart Display
- CHARGERY POWER charger
I'm a mechanical engineer so for the dismantling, cleaning, rebuild, optimizing steps, no problem even for adaptation of motor or battery mounts on the steel frame.
Here is the bike in puzzle mode before treatment on parts :
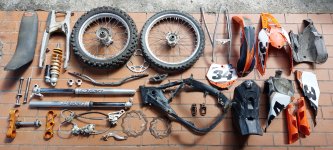
Mechanic is well advanced and I post the before/after of the front brake to give you an example of what finition I intend (more photo available if wanted by the crew) :
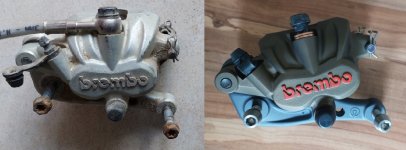
But before asking to you a LLLOOOOTTT of questions about setting the BMS/ESC of my installation, I still need some advice, comment and/or confirmation about the main electrical scheme of the bike. My last version is below :
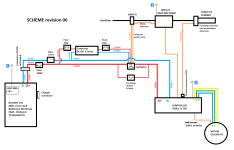
What do you think. I have already removed the back EMF diode on ESC inputs cause Hackey BABEL from 3SHUL told me this is not necessary. I'm wondering how to remove the DC converter 12V to have something more reliable and simplier but how to ignit the beast without any fire risk !!! ?
And I still wait assembly instructions from Hackey for the installation of the encoder kit inside the motor. If someone has a link or done the work with pictures or videos, I'm quite interested !!!
Thanks for your advices/comments/congratulations/threat messages ! I take everything to have a perfect bike with mainly range but also some punch and reliability to go back home with smile and dirt-covered-teeth after each session in the woods around !
I'm Greg from French Alps.
I come to this forum to present to you my build project based on a dirty KTM 450 SXF from 2009 bought 900€ without motor.
The swap consist of :
- motor QS138 70H V3 with installation of the 3SHUL encoder kit
- ESC 3SHUL CL700
- DOMINO throttle
- homemade battery build with :
* NMC Li-Ion cells from CALB with threaded studs on copper 60mm² bus bars
* 89 V nominal (24S1P)
* 58 Ah
* 5150 Wh
* 110 A continuous
* 350 A peak
* ANT BMS
* aluminium plates casing
- RAGE MECHANICS Smart Display
- CHARGERY POWER charger
I'm a mechanical engineer so for the dismantling, cleaning, rebuild, optimizing steps, no problem even for adaptation of motor or battery mounts on the steel frame.
Here is the bike in puzzle mode before treatment on parts :
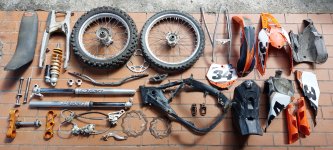
Mechanic is well advanced and I post the before/after of the front brake to give you an example of what finition I intend (more photo available if wanted by the crew) :
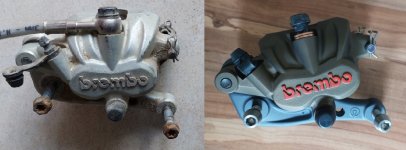
But before asking to you a LLLOOOOTTT of questions about setting the BMS/ESC of my installation, I still need some advice, comment and/or confirmation about the main electrical scheme of the bike. My last version is below :
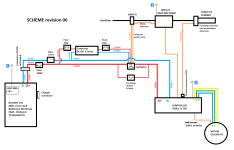
What do you think. I have already removed the back EMF diode on ESC inputs cause Hackey BABEL from 3SHUL told me this is not necessary. I'm wondering how to remove the DC converter 12V to have something more reliable and simplier but how to ignit the beast without any fire risk !!! ?

And I still wait assembly instructions from Hackey for the installation of the encoder kit inside the motor. If someone has a link or done the work with pictures or videos, I'm quite interested !!!
Thanks for your advices/comments/congratulations/threat messages ! I take everything to have a perfect bike with mainly range but also some punch and reliability to go back home with smile and dirt-covered-teeth after each session in the woods around !
Last edited: