whatever
100 kW
- Joined
- Jun 3, 2010
- Messages
- 1,297
Might seem pretty obvioius to some, but here is my method for cleaning out the holes in circuit boards that are filled with solder when replacing mosfets. I just get a safety pin which is approx same diameter of the hole, just a little bit smaller.
Put the pointy end of safety pin on the hole filled with solder then touch the solder trying to remove with hot soldering iron with a little bit of solder on it ( sometimes easier to go from top or sometimes bottom of board).
I always put the safety pin such a way that it wont push any contact metal on board out, so if contact is on top of board push down from top.
So you wiggle the safety pin a little while applying the iron, it will go through the hole as soon as solder gets liquid, it will take the solder with it. To withdraw the safety pin is usually necessary to scrap off the solder on the pin with knife or similar.
Its extremely quick and effective method.
Before puting new mosfet in place, work the safety pin around the hole just to make sure its big enough for the mosfet to push in,
its usually a nice snug fit.
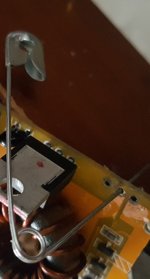
Put the pointy end of safety pin on the hole filled with solder then touch the solder trying to remove with hot soldering iron with a little bit of solder on it ( sometimes easier to go from top or sometimes bottom of board).
I always put the safety pin such a way that it wont push any contact metal on board out, so if contact is on top of board push down from top.
So you wiggle the safety pin a little while applying the iron, it will go through the hole as soon as solder gets liquid, it will take the solder with it. To withdraw the safety pin is usually necessary to scrap off the solder on the pin with knife or similar.
Its extremely quick and effective method.
Before puting new mosfet in place, work the safety pin around the hole just to make sure its big enough for the mosfet to push in,
its usually a nice snug fit.
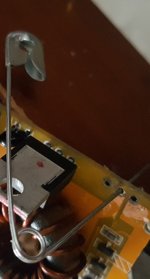