urialbocher
100 µW
- Joined
- May 9, 2009
- Messages
- 8
Hi all,
This build started some time ago, working on it on and off, mostly off. I have been riding full suspension mountain bike for roughly 10 years and always wanted to add a small motor kit to make the ride more fun. I wanted minimum changes to the bike and so the goal was preserve all 27 speeds, not to add too much weight, and make the kit easily detachable so I can switch back to regular mountain bike without too much work.
I looked around for motors for quite a while and finally decided to go with the my1018z (TNC scooters) which has relatively low weight and an integrated reduction gear. Since the motor does not have a freewheel sprocket, I got one from Juerg Lanz, a Swiss guy who has since then opened an ebike shop (http://www.boosty.ch/en/bike-kits.html), and who luckily for me designed one specifically for this motor. Next step was to get a freewheeling crank. I got the Echo threaded cranks and bought the threaded freewheel and some nasty metal chainrings from Cyclon.
My first attempt was was just to get the motor mounted on the bike and see how it goes. I collected some scap metal and mounted the thing on the bike. I used a pair of DIN rails which were fastened against the bike's tube using a pair of long bolts. Since these were my spare bike, and I only wanted to get a feel of things, I did not mind drilling through the frame tube. I also wasn't too concerned about strength issues since the hole diameter wasn't bigger than the exisiting water bottle holes.
The results were pretty nasty, but the thing worked pretty well...
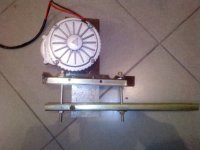
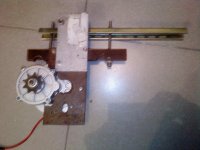
View attachment 11
The my1018z motor is annoyingly noisey, a result of it's straight cut gears, but other than that I was happy with its performance. It gave me the extra boost without turning the bicycle into a tank, and so I decided to stick with it and create some drawings for milled parts. I designed an aluminum "spider" to hold 4 chainrings - the bike 3 originals, and one for the motor:
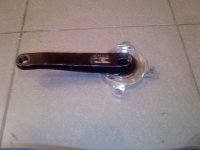
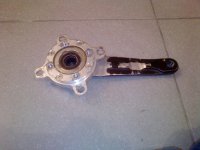
For the motor mount I decided not to use the frame tube, and instead use the bike bottom bracket as a basis for the mount. This was roughly 2 years ago and since then I discoverd that others have been using this method too (Elation, and especially Malcolm with his elegant design at: http://endless-sphere.com/forums/viewtopic.php?f=2&t=3306&p=55489&hilit=Juerg+Lanz#p55489). I am still not sure it is beats mounting of the frame tube but I went with it anyway.
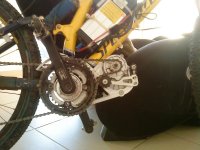
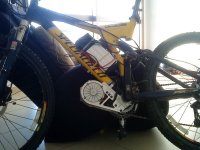

Basically, the motor slides into place using the 10mm placement pins, and a pull plunger fixes it into position Then the chain is placed, followed by the tensioner. Pretty easy swap between motor/non-motor configulation, which is what I aimed for to start with. I do have to admit though, that the motor is mostly on, it's just much more fun.
This setup worked quite well, but in time I started to see some that the Cyclone freewheel is developing slack, and some greese was dripping out. The the bending moment created by the four chainring setup was taking its toll, and it seemed only a question of time until the thing falls apart. The single bearing just does not seem up to it.
I looked around a little but couldn't find an easy solution. So I considered some options:
1. Get a better rachet type freewheel than Cyclone's. This still does not resolve the single bearing issue but will last longer and is a relatively cheap option.
2. Go for a sprag clutch, something like Elation's. This doesn't resolve the single bearing problem problem without an additional bearing and also requires making some adoptations to match the crank. The sprags are also pretty heavy, something like 300 grams. I was also a bit concered about their quality. The price for the German version was about $120 compared to $30 for the chinese you can get off ebay and I do not belive in free meals...
3. Go for a one way needle bearing. These are basically composed of a one way mechanism in the center of the unit, and two roller bearings on the side. The largest one I could find is the HFL3530 which easly supports the bending moment created by the chainrings. On the down side is that the maximum torque the clutch allows is 121NM which translates to about 70kg applied on the pedals at a horizontal orientation, which, to say the least, is marginal considering the average person.
I finally decided to go with the HFL3530. I decided this considering some additional thingslike the fact I could get it for $30 from a real company (INA). The failing torque has to be higher than the permissible torque of 121MN, and I belive than in the vast majority of the rides I am not even near that value. This is compared the first two options were you are basically loading the bearing incorrectly ALL the time. An additional little advantage to this roller clutch is its weight - 50 grams only!
I was lucky to find a manufacturer that gave me, what I thought, are reasonable prices. The final solution consisted of 3 parts
1. A new crank arm, with an ISIS fit created using electroerosion (EDM).
2. An adopter between the crank arm and the roller clutch (made from a hardened polished round bar).
3. A new "spider" for the chainrings into which the roller clutch was press fit.
Enough with the talking... here are some pictures:
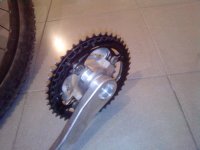
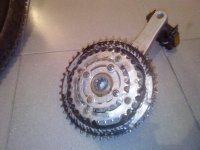
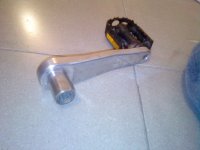
View attachment 2
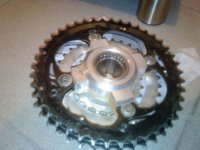
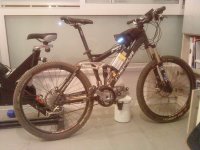
Uri
This build started some time ago, working on it on and off, mostly off. I have been riding full suspension mountain bike for roughly 10 years and always wanted to add a small motor kit to make the ride more fun. I wanted minimum changes to the bike and so the goal was preserve all 27 speeds, not to add too much weight, and make the kit easily detachable so I can switch back to regular mountain bike without too much work.
I looked around for motors for quite a while and finally decided to go with the my1018z (TNC scooters) which has relatively low weight and an integrated reduction gear. Since the motor does not have a freewheel sprocket, I got one from Juerg Lanz, a Swiss guy who has since then opened an ebike shop (http://www.boosty.ch/en/bike-kits.html), and who luckily for me designed one specifically for this motor. Next step was to get a freewheeling crank. I got the Echo threaded cranks and bought the threaded freewheel and some nasty metal chainrings from Cyclon.
My first attempt was was just to get the motor mounted on the bike and see how it goes. I collected some scap metal and mounted the thing on the bike. I used a pair of DIN rails which were fastened against the bike's tube using a pair of long bolts. Since these were my spare bike, and I only wanted to get a feel of things, I did not mind drilling through the frame tube. I also wasn't too concerned about strength issues since the hole diameter wasn't bigger than the exisiting water bottle holes.
The results were pretty nasty, but the thing worked pretty well...
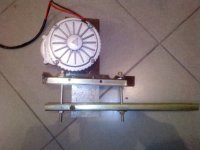
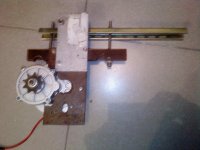
View attachment 11
The my1018z motor is annoyingly noisey, a result of it's straight cut gears, but other than that I was happy with its performance. It gave me the extra boost without turning the bicycle into a tank, and so I decided to stick with it and create some drawings for milled parts. I designed an aluminum "spider" to hold 4 chainrings - the bike 3 originals, and one for the motor:
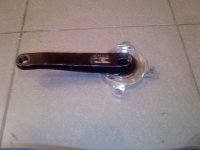
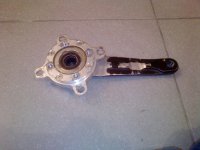
For the motor mount I decided not to use the frame tube, and instead use the bike bottom bracket as a basis for the mount. This was roughly 2 years ago and since then I discoverd that others have been using this method too (Elation, and especially Malcolm with his elegant design at: http://endless-sphere.com/forums/viewtopic.php?f=2&t=3306&p=55489&hilit=Juerg+Lanz#p55489). I am still not sure it is beats mounting of the frame tube but I went with it anyway.
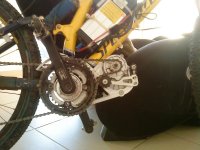
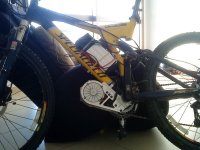

Basically, the motor slides into place using the 10mm placement pins, and a pull plunger fixes it into position Then the chain is placed, followed by the tensioner. Pretty easy swap between motor/non-motor configulation, which is what I aimed for to start with. I do have to admit though, that the motor is mostly on, it's just much more fun.
This setup worked quite well, but in time I started to see some that the Cyclone freewheel is developing slack, and some greese was dripping out. The the bending moment created by the four chainring setup was taking its toll, and it seemed only a question of time until the thing falls apart. The single bearing just does not seem up to it.
I looked around a little but couldn't find an easy solution. So I considered some options:
1. Get a better rachet type freewheel than Cyclone's. This still does not resolve the single bearing issue but will last longer and is a relatively cheap option.
2. Go for a sprag clutch, something like Elation's. This doesn't resolve the single bearing problem problem without an additional bearing and also requires making some adoptations to match the crank. The sprags are also pretty heavy, something like 300 grams. I was also a bit concered about their quality. The price for the German version was about $120 compared to $30 for the chinese you can get off ebay and I do not belive in free meals...
3. Go for a one way needle bearing. These are basically composed of a one way mechanism in the center of the unit, and two roller bearings on the side. The largest one I could find is the HFL3530 which easly supports the bending moment created by the chainrings. On the down side is that the maximum torque the clutch allows is 121NM which translates to about 70kg applied on the pedals at a horizontal orientation, which, to say the least, is marginal considering the average person.
I finally decided to go with the HFL3530. I decided this considering some additional thingslike the fact I could get it for $30 from a real company (INA). The failing torque has to be higher than the permissible torque of 121MN, and I belive than in the vast majority of the rides I am not even near that value. This is compared the first two options were you are basically loading the bearing incorrectly ALL the time. An additional little advantage to this roller clutch is its weight - 50 grams only!
I was lucky to find a manufacturer that gave me, what I thought, are reasonable prices. The final solution consisted of 3 parts
1. A new crank arm, with an ISIS fit created using electroerosion (EDM).
2. An adopter between the crank arm and the roller clutch (made from a hardened polished round bar).
3. A new "spider" for the chainrings into which the roller clutch was press fit.
Enough with the talking... here are some pictures:
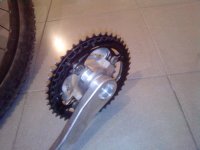
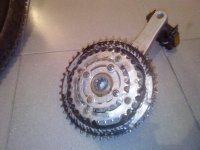
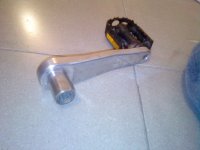
View attachment 2
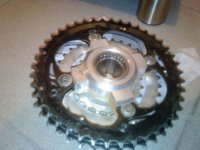
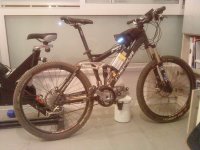
Uri