theGoPedal
100 mW
Hi, first timer here.
I have a 24V cordless electric lawnmower and I wanted to upgrade it's battery from lead to LiFePO4 for increased range. I ordered a 24V20ah pack from 'Michelle at Headway', who quoted me a very good price for this pack size. I'm happy to say the transaction went smoothly and my battery arrived approx 2 weeks after I ordered it.
When I got the battery, it's voltage was 28.0V and everything looked good. However, when I hooked it up to the lawnmower it failed to spin the motor. Here are the details: When I turn the mower on, the blade motor turns about 1/4 of a turn and then stops. There is a smaller, secondary motor for the wheels (it's a self-propelled model) and this motor spins fine, no issue there. So, my guess is the BMS that came with the battery is limiting the current which is keeping the blade motor from spinning.
When I ordered the battery, I was asked what the working current of the lawnmower was. I didn't have a meter that could measure this, so I guessed it to be 20A. There is a 40A safety fuse on the mower, so I guessed the working current would be half of that. Maybe I guessed too low.
My question is, can I see what the current limit is from looking at the BMS board? And can I adjust anything on the BMS to increase the current?
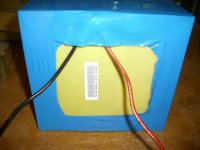
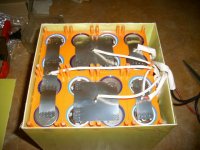
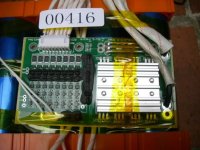
I have a 24V cordless electric lawnmower and I wanted to upgrade it's battery from lead to LiFePO4 for increased range. I ordered a 24V20ah pack from 'Michelle at Headway', who quoted me a very good price for this pack size. I'm happy to say the transaction went smoothly and my battery arrived approx 2 weeks after I ordered it.
When I got the battery, it's voltage was 28.0V and everything looked good. However, when I hooked it up to the lawnmower it failed to spin the motor. Here are the details: When I turn the mower on, the blade motor turns about 1/4 of a turn and then stops. There is a smaller, secondary motor for the wheels (it's a self-propelled model) and this motor spins fine, no issue there. So, my guess is the BMS that came with the battery is limiting the current which is keeping the blade motor from spinning.
When I ordered the battery, I was asked what the working current of the lawnmower was. I didn't have a meter that could measure this, so I guessed it to be 20A. There is a 40A safety fuse on the mower, so I guessed the working current would be half of that. Maybe I guessed too low.
My question is, can I see what the current limit is from looking at the BMS board? And can I adjust anything on the BMS to increase the current?
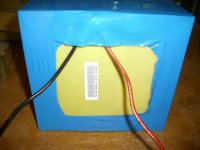
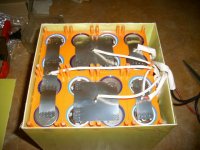
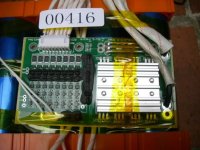