Sunder
10 MW
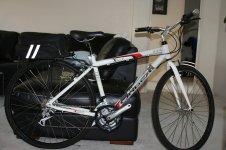
After months of fartarsing around with gears, derailleurs and lacing the rear wheel, I've finally finished my semi-stealth project. To give you a bit of background, my previous bike was a steel framed no suspension mountain bike with a Magic Pie copy on the front wheel. While it did the job, my complaints were that the bike was heavy (A bit over 30kg), and didn't let me pedal at full speed. (~45km/h). It was also obviously an electric bike.
The new project was designed to rectify those issues by replacing the front motor with a rear Q100. The photo you see above is the result.
The bike now weighs just over 18kg with a 12S2P (10Ah) Lipo battery attached. While it is substantially lighter, the balance now feels a little "off" with almost all the weight behind the seat post.
First impressions was that it is very, very torquey - and very noisy at low speeds. Get above 15km/h though, and it's a near silent whine.
The bike feels a little heavy without power, but nothing like the old DD motor, but this is not a surprise, since my road bike weighs less than 7kg. I can conceivably pedal this bike meaningful distances, and keep up with normal cyclists on flats and very low hill terrain. They'd leave me for dead on any hill though. A tiny amount of power though, and I'm effortlessly doing 30km/h.
Full throttle on this thing is about 30-35km/h. I haven't fitted the bike computer yet, but will update this post when I do. Once on full throttle, I can easily pedal to high 40s, which is actually about what I can sustain on my road bike. I'm surprised with a 44/11t, I can only pedal up to the second last gear (44/13, I think), otherwise my legs start burning... I guess I need more training. I would have thought a 44/11t would top out at high 40s, but then again, my estimates could be wrong.
I intentionally did a very steep hill - maybe a 70-80m gain over about 700m. On full throttle with a bit of pedal assist, I was easily doing 20-25km/h, and the motor felt only slightly warmer than the bike at the end - caveat, it was raining and the motor was clearly wet, so I intend repeating this a dry warm day. It could also be that the outside is (most likely unintentionally) thermally isolated from the parts that get hot. Still need to be careful until I know for certain it can cope.
Overall, I would rate the satisfaction on this bike a 7.5/10. It could still be far better, but considering I rated my last bike only a 5/10, it's a step forward.
Pros:
Very hard to tell it's an electric bike
Much lighter than my last bike
Silent at high speed
Can be easily pedaled
Very torquey up hills and from start.
Cons:
You're not fooling anyone if you power from start. (grrrrrrrreeerrrrr!)
Would have liked a top speed maybe 5-10km/h faster
My wife would kill me if I told her I was upgrading again though, so I think I will stick with this bike for another year or so, then maybe look at another geared hubbie - slightly bigger, maybe hand re-wound with stronger magnets and filled with ATF. That might raise me to a 9/10 satisfaction.