OK Wow. So we managed to do the tests just over a week ago, with both a high speed (240fps) camera and an IR camera recording the experiment. We were initially trying to cause a cell venting with with the bare unpotted packs but it proved trickier than expected to have a "short circuit" that would drain enough current to cause the cells to go, but not so much current as to vaporize the connecting tabs. However, with the potted units the tabs were in good thermal contact with the resin and that seemed to allow them to handle more amperage without melting apart. In the end, a long spool of copper wire served as the perfect load for this, giving us an initial ~25C discharge rate on the cells.
Have a look at the results:
https://www.youtube.com/watch?v=oBlac5gWLfI
[youtube]oBlac5gWLfI[/youtube]
It took almost 2 minutes of short current flowing during which the batteries drained over half of their energy, before finally something went open circuit. At that point in the test you can see that cell#4 is clearly hotter than the others, but it's not until the current has dropped to 0 amps that things really get exciting, and then one by one nearby cells that were just hot now start to go thermal too. We sped up the IR video feed to 5x rate but whole process took about 20 minutes before the pack finally started cooling again.
To the credit of the cells and the enclosure there were no flames or fireballs, but still quite a lot of unpleasant smoke and charring. Here's what the pack looked like after the fact. The blue/red/yellow colours on the right was us just doing a quick experiment with drops of dye on the fibreglass cloth before potting.
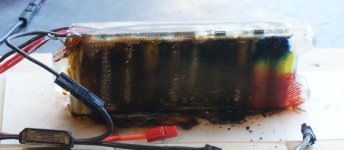
Have a look at the results:
https://www.youtube.com/watch?v=oBlac5gWLfI
[youtube]oBlac5gWLfI[/youtube]
It took almost 2 minutes of short current flowing during which the batteries drained over half of their energy, before finally something went open circuit. At that point in the test you can see that cell#4 is clearly hotter than the others, but it's not until the current has dropped to 0 amps that things really get exciting, and then one by one nearby cells that were just hot now start to go thermal too. We sped up the IR video feed to 5x rate but whole process took about 20 minutes before the pack finally started cooling again.
To the credit of the cells and the enclosure there were no flames or fireballs, but still quite a lot of unpleasant smoke and charring. Here's what the pack looked like after the fact. The blue/red/yellow colours on the right was us just doing a quick experiment with drops of dye on the fibreglass cloth before potting.
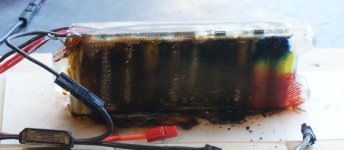