LI-ghtcycle
10 MW
I know this will vary from motor to motor, and I have heard it said that a good rule of thumb is that if the motor is too hot to keep your hand on it comfortably for more than a few seconds it's getting too hot.
I have a IR thermometer, so I'm guessing that things start to get bad for the typical motor around 180 - 200F on the outside (I know this means things are MUCH hotter on the inside, so I am hoping to get a feel for where the limits are on my Golden Motor In-runner "Trike Motor") but how one translates that on this motor I'm not exactly sure where to start.
http://goldenmotor.com/
(It's the one on the far right, the "800W" model)
I plan on trying this motor at 74V (20S of Turnigy Nano Tech 25c) and I will most likely get some liquid cooling via a home computer style liquid cooling system with some hand bent copper tubing between the "fins" of a curved aluminum heat sink on the outside, using a small 12V pump with sump and probably a sealed system will be enough for my needs.
Just wanting to keep things on the cool side for some moderate over-volting.
I have been using this motor at 12S quite successfully with no active cooling and it has only gotten moderately hot going up the local hill (2 miles 5 - 12% grade IIRC) and has never really had me too worried, but at 74V I think it will be a bit more hot. :wink:
I have a IR thermometer, so I'm guessing that things start to get bad for the typical motor around 180 - 200F on the outside (I know this means things are MUCH hotter on the inside, so I am hoping to get a feel for where the limits are on my Golden Motor In-runner "Trike Motor") but how one translates that on this motor I'm not exactly sure where to start.
http://goldenmotor.com/
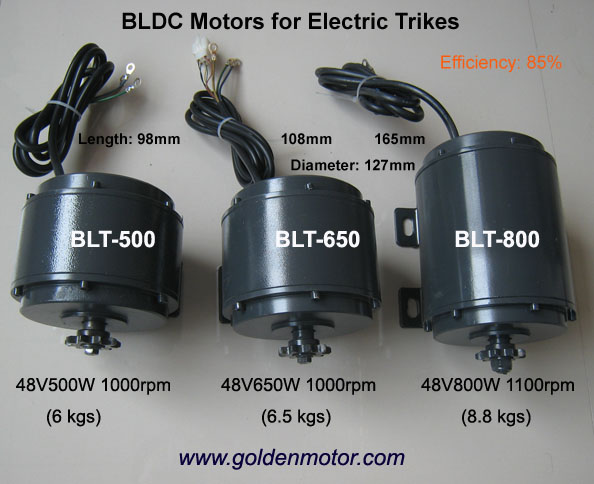
(It's the one on the far right, the "800W" model)
I plan on trying this motor at 74V (20S of Turnigy Nano Tech 25c) and I will most likely get some liquid cooling via a home computer style liquid cooling system with some hand bent copper tubing between the "fins" of a curved aluminum heat sink on the outside, using a small 12V pump with sump and probably a sealed system will be enough for my needs.
Just wanting to keep things on the cool side for some moderate over-volting.
I have been using this motor at 12S quite successfully with no active cooling and it has only gotten moderately hot going up the local hill (2 miles 5 - 12% grade IIRC) and has never really had me too worried, but at 74V I think it will be a bit more hot. :wink: