This build thread might be a bit premature, but since I've already invested countless hours in reading the forum, I figured I might as well start posting before it begins. Long story short, I want an electric enduro bike, and having exhausted all options for ready models, I found someone selling a half-finished build. The bike has the engine and the controller mounted in, and the battery has been ordered in a reportedly reputable local shop. I'm scheduled to pick it up next weekend if the battery does indeed materialize. Here's what I have laid out so far, please tell me if you spot any mistakes, improvement ideas or reasons not to get into this 
Just to clarify: I have no experience building electric motorcycles. I've built two ebikes from kits this year, and have amateur electronics and CAD/3D printing experience. I own an EXC500 enduro that I ride in rally competitions as well as superenduro practice and maintain myself. The donor bike is supposedly in good mechanical condition with suspension serviced and all bearings replaced, but I can deal with any issues on that front if they arise.
Now, since this is a project that's been already started by someone else, I am a bit locked into the choices made here. That being said, I think it fits my needs quite perfectly. What I ideally want to build:
- under 100kg total
- not competition, just for recreational riding
- mostly enduro/hard enduro/trials - low speeds
- likely with almost no plastics to not look too conspicuous near friendly monster e-bikes
- safe to ride and charge
Mechanically I plan to put the rear brake on the handlebar, potentially with switch wired from it to regen braking as well, original 21/19 wheels with stock tyre sizes. I'll likely replace both master cylinders with a matched set if I can find something decent for a reasonable price. I don't really need a screen, but might make a simple arduino bridge to the CAN/serial output to get voltage and error status from the controller and show it in a discreet way.
As for target power: given the cells are rated at 16.6A cont. / 21.2A peak, this would give me figures of 332 and 424 amps, respectively. That being said, I've seen factors of 50-80% being applied to 18650 cells in a pack, so let's settle on 200 continuous and 350-400A peak. At the rated 72V, it's 14.4kW of continuous power, potentially as high as 32kW in few-second bursts; at least that's what the battery should be able to sustain. I don't expect the small 70H motor to last an hour at 14.4k, but given I'll mostly be doing trail riding with occasional logs and steep uphills with plenty of cooldown in between, i am not very concerned about that. The controller is supposedly rated at 190/450A, so my target settings for this, considering Votol software, would be 200A for normal busbar current, with modes set probably at something like 25/50/100%, and 350-400A of sport mode current, potentially with the limit timer just in case.
Considering the engine having 1:2.35 reduction, with the stock 13:51 gearing, gives me 9.21 final drive ratio. I still have the option to go to 52 on the rear, but I think it should be quite okay if I can kick in the double power for 15-30s needed for the steepest climbs and obstacles. I have calculated the max speed given reasonable engine RPM to be about 95km/h, and would happily accept 70-75 on the final construction if the low-end is strong enough.
One thing I'm a bit concerned about is the battery capacity. The cells can produce respectable current, but the data online only gives them about 2Ah each. That would mean just 40Ah for the entire battery, or 2.9kWh. That's suspiciously small considering how large the usual electric motorcycle batteries are, and so the battery might need an upgrade in the future - likely to be replaced either with some LG chem pouch cells, or at the very least something like VTC5a which seem to have both higher current and +30% capacity. At least the weight of just the cells comes up at around ~18kg, so that's looking good for my weight target.
The biggest part left to finish in this project is going to be the battery case, and for that I'm currently aiming at creating a sheet metal design that I'll send to my local aluminium shop, so that they can review it, sent for laser cutting, then bend and TIG weld for me.
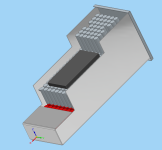
The plan would be to glue FR4, epoxy fiberglass or PC panels inside to prevent shorting on the box, then cradle the battery inside with some rubber. I'm still not sure how the finish battery will look like, but I'd like to connect it to waterproof outside terminals using either thick copper bars or 0AWG connecting segments. Details of those connections are TBD - as well as how the box will actually close.
So, while i sit here and twiddle my thumbs, here are the questions to the community:
1) Do you see anything concerning in the project based on the above?
2) Is my idea for the box okay? If so
2A) Do you have opinions for how the box should close? A small lid on the top held by screws around it or two halves grabbed together around the perimeter?
versus 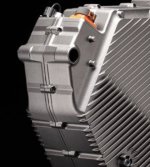
3) Should I have a precharge resistor / battery killswitch?
3A) if so, should it be operated completely automatically with a timer to prevent misuse or manually with double switches?
3B) should the contactron for the main circuit reside inside or outside of the battery?
3C) is it okay if I leave the precharge circuit always-on and only switch the main output?
3D) is it necessary to have the main battery killswitch easily accessible? I plan a magnetic killswitch on the handlebar wired to the controller as a safety measure.
4) Do i need another fuse inside or near the battery? AFAIK the controller has a place for a fuse on its enclosure:
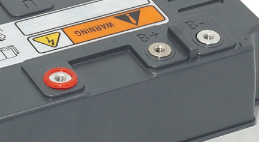
Let's hope I can indeed make this project real; at the same time, huge thanks to the community for posting so, so much valuable information here, so I could even contemplate such an undertaking.
Just to clarify: I have no experience building electric motorcycles. I've built two ebikes from kits this year, and have amateur electronics and CAD/3D printing experience. I own an EXC500 enduro that I ride in rally competitions as well as superenduro practice and maintain myself. The donor bike is supposedly in good mechanical condition with suspension serviced and all bearings replaced, but I can deal with any issues on that front if they arise.
Now, since this is a project that's been already started by someone else, I am a bit locked into the choices made here. That being said, I think it fits my needs quite perfectly. What I ideally want to build:
- under 100kg total
- not competition, just for recreational riding
- mostly enduro/hard enduro/trials - low speeds
- likely with almost no plastics to not look too conspicuous near friendly monster e-bikes
- safe to ride and charge
Mechanically I plan to put the rear brake on the handlebar, potentially with switch wired from it to regen braking as well, original 21/19 wheels with stock tyre sizes. I'll likely replace both master cylinders with a matched set if I can find something decent for a reasonable price. I don't really need a screen, but might make a simple arduino bridge to the CAN/serial output to get voltage and error status from the controller and show it in a discreet way.
As for target power: given the cells are rated at 16.6A cont. / 21.2A peak, this would give me figures of 332 and 424 amps, respectively. That being said, I've seen factors of 50-80% being applied to 18650 cells in a pack, so let's settle on 200 continuous and 350-400A peak. At the rated 72V, it's 14.4kW of continuous power, potentially as high as 32kW in few-second bursts; at least that's what the battery should be able to sustain. I don't expect the small 70H motor to last an hour at 14.4k, but given I'll mostly be doing trail riding with occasional logs and steep uphills with plenty of cooldown in between, i am not very concerned about that. The controller is supposedly rated at 190/450A, so my target settings for this, considering Votol software, would be 200A for normal busbar current, with modes set probably at something like 25/50/100%, and 350-400A of sport mode current, potentially with the limit timer just in case.
Considering the engine having 1:2.35 reduction, with the stock 13:51 gearing, gives me 9.21 final drive ratio. I still have the option to go to 52 on the rear, but I think it should be quite okay if I can kick in the double power for 15-30s needed for the steepest climbs and obstacles. I have calculated the max speed given reasonable engine RPM to be about 95km/h, and would happily accept 70-75 on the final construction if the low-end is strong enough.
One thing I'm a bit concerned about is the battery capacity. The cells can produce respectable current, but the data online only gives them about 2Ah each. That would mean just 40Ah for the entire battery, or 2.9kWh. That's suspiciously small considering how large the usual electric motorcycle batteries are, and so the battery might need an upgrade in the future - likely to be replaced either with some LG chem pouch cells, or at the very least something like VTC5a which seem to have both higher current and +30% capacity. At least the weight of just the cells comes up at around ~18kg, so that's looking good for my weight target.
The biggest part left to finish in this project is going to be the battery case, and for that I'm currently aiming at creating a sheet metal design that I'll send to my local aluminium shop, so that they can review it, sent for laser cutting, then bend and TIG weld for me.
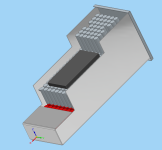
The plan would be to glue FR4, epoxy fiberglass or PC panels inside to prevent shorting on the box, then cradle the battery inside with some rubber. I'm still not sure how the finish battery will look like, but I'd like to connect it to waterproof outside terminals using either thick copper bars or 0AWG connecting segments. Details of those connections are TBD - as well as how the box will actually close.
So, while i sit here and twiddle my thumbs, here are the questions to the community:
1) Do you see anything concerning in the project based on the above?
2) Is my idea for the box okay? If so
2A) Do you have opinions for how the box should close? A small lid on the top held by screws around it or two halves grabbed together around the perimeter?
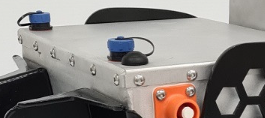
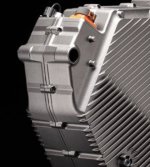
3) Should I have a precharge resistor / battery killswitch?
3A) if so, should it be operated completely automatically with a timer to prevent misuse or manually with double switches?
3B) should the contactron for the main circuit reside inside or outside of the battery?
3C) is it okay if I leave the precharge circuit always-on and only switch the main output?
3D) is it necessary to have the main battery killswitch easily accessible? I plan a magnetic killswitch on the handlebar wired to the controller as a safety measure.
4) Do i need another fuse inside or near the battery? AFAIK the controller has a place for a fuse on its enclosure:
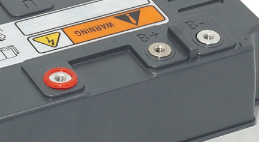
Let's hope I can indeed make this project real; at the same time, huge thanks to the community for posting so, so much valuable information here, so I could even contemplate such an undertaking.
Last edited: