Hi efreak, did you manage to get those tyco dc/dc's working? If not then this is how I'd connect them.
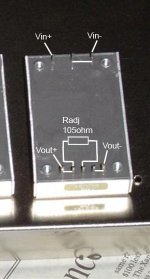
From the equation on page 11 of the datasheet, I get a value of 105 ohm for the adjust up resistor to give a 10% increase in Vout to 3.63V.
From the data sheet (page 10)
“Overcurrent Protection
To provide protection in a fault (output overload) condition,
the unit is equipped with internal current-limiting
circuitry and can endure current limiting for up to one
second. If overcurrent exists for more than one second,
the unit will shut down.
At the point of current-limit inception, the unit shifts
from voltage control to current control. If the output voltage
is pulled very low during a severe fault, the currentlimit
circuit can exhibit either foldback or tailout characteristics
(output current decrease or increase).
The module is available in two overcurrent configurations.
In one configuration, when the unit shuts down it
will latch off. The overcurrent latch is reset by either
cycling the input power or by toggling the ON/OFF pin
for one second. In the other configuration, the unit will
try to restart after shutdown. If the output overload condition
still exists when the unit restarts, it will shut down
again. This operation will continue indefinitely until the
overcurrent condition is corrected.â€Â
Hopefully you've got the type which doesn't latch off when over current is reached.
If the Meanwell power supply limits current to 7A with 110V input ie. is a CC/CV charger, which it looks like it is, then, with four converters connected to it they shouldn't ever hit the over current point, but the Eltek will allow 25A to the converters and therefore they could trip off if the cells draw too many amps, which won't be good if they're the latch off type.
Looks like there is a similar issue with the over temp protection too, you might need to add a fan to the PSU to keep everything cool enough.
What cells are you gonna be charging with these? How many per parallel group?