John in CR
100 TW
So I've got my ferrite cores, 4.5"OD, 2.25"ID, .75" thick that I'm going to wind with 8ga wire. I'm shooting to add approx. 50uH to 75uH to each phase in an effort to help protect my last remaining higher power controller from my controller eating motor. Even at quite moderate current every controller I've tried with these motors has run quite warm, and with each phase consisting of 2 turns of 8-9ga wire on 17 teeth, I'm convinced that low inductance with low resistance is to blame. I'm certainly not going to add resistance, so after a couple thousand $ worth of controllers over 2 years, I'm finally going to follow Fechter's advice and add some chokes in front of the motor.
I wanted to check before I do something stupid and make sure I'm not doing something that introduces a new risk. What if these DIY coils have some variance in their inductance? Could that create some kind of imbalance and blow the controller?
While I'm at it, I'd like to understand what the added inductance does that makes it an easier load for the controller, and are there detriments other than hopefully slight losses in the added coils? How will it affect performance. I understand that inductors slow the flow of electricity, and in other applications they act as low pass filters. On its own, I take it that a controller would send square pulses of DC current due to PWM, and if the current is allowed to flow freely, the abruptness of on/off of high currents is hard on the controller, like turning a facet on and off very fast repeatedly and you hear the water hammer effect in the pipes. Then the added inductance slows the transitions and rounds off the corners so to speak, resulting in a smoother wave form instead of one that is like the bill of a sawfish.
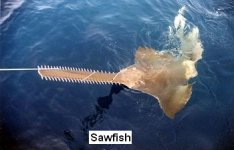
I wanted to check before I do something stupid and make sure I'm not doing something that introduces a new risk. What if these DIY coils have some variance in their inductance? Could that create some kind of imbalance and blow the controller?
While I'm at it, I'd like to understand what the added inductance does that makes it an easier load for the controller, and are there detriments other than hopefully slight losses in the added coils? How will it affect performance. I understand that inductors slow the flow of electricity, and in other applications they act as low pass filters. On its own, I take it that a controller would send square pulses of DC current due to PWM, and if the current is allowed to flow freely, the abruptness of on/off of high currents is hard on the controller, like turning a facet on and off very fast repeatedly and you hear the water hammer effect in the pipes. Then the added inductance slows the transitions and rounds off the corners so to speak, resulting in a smoother wave form instead of one that is like the bill of a sawfish.
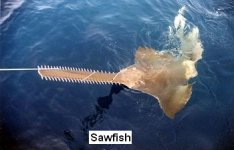