I was troubleshooting my DIY BBSHD 52v bike running @33amp max.
Came across these burned butt connectors on the main and I also take a small current for accessories from here.
(This was not the main issue, but happy I came across it)
Before I've always been using those heat shrink with solder connectors, but after reading about crimping, it seemed to be a better choice.
The connection seems strong and solid, nothing came loose.
These yellow butts are just cheap ones I found, is there any difference in buying more expensive ones?
Any thoughts?

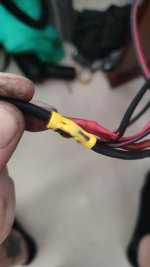
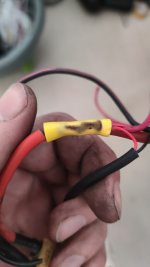
Came across these burned butt connectors on the main and I also take a small current for accessories from here.
(This was not the main issue, but happy I came across it)
Before I've always been using those heat shrink with solder connectors, but after reading about crimping, it seemed to be a better choice.
The connection seems strong and solid, nothing came loose.
These yellow butts are just cheap ones I found, is there any difference in buying more expensive ones?
Any thoughts?

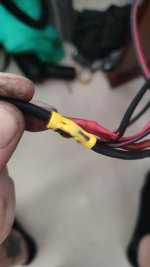
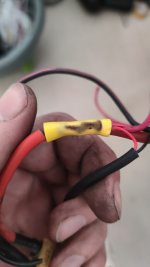