I recommend that copies of this clamping torque-arm be made from mild steel, aluminum was used to make the prototyping easy.
Here is the current version. If was doing this over, I would make them 8-1/4 inches long (instead of 6 inches shown) and use two U-bolts instead of one. That size would fit in the smallest post office "if it fits, it ships" box, roughly $10 to anywhere in the USA.
edit, I stumbled across an interesting fact. I've swapped the first version of these plates onto my fat bike, so I can test a DD hubmotor. When dry fitting everything together, I suddenly realized I could move the entire plate to the rear just a little, and that would tension the chain enough that I wouldn't need a tensioner, if using a 14T single-speed freewheel.
your derailleurs might be longer or shorter than mine, so your chains will be shorter or longer than mine. That being said, these plates have a 10mm wide slot for the axle, and the length of the slot is 1.6 inches (42mm).
The distance from the center of the bolt hole (the bolt which goes into the stock frames' drop out) to the front edge of the slot is 1-3/4 inches (55mm). If you want to try to make these, I recommend mocking up one of them out of 1/4-inch thick plywood, which is cheap, fast, and easy to cut.
xxxxxxxxxxxxxxxxxxxxxxxxxxxxxxxxxxxxxxxxx
Original thread starts here:
Its only a matter of time before mid-drives take over the off-road market, but...for a street hot rod ebike? large direct drive (DD) hubs remain popular. The big hold up is torque arms, and the wide variety of frames out there. Some frames have the desirable broad and flat drop-outs, which allow a lot of options. Here are 6 pages of Torque Arm ideas: https://endless-sphere.com/forums/viewtopic.php?f=2&t=26444
A while back, an Australian ES member used laser-cutting and water-jetting to make a 3-level torque-arm for a specific popular off-road frame. The three levels were welded together to create a desirable clamping element (here's the link, thanks, Sam https://endless-sphere.com/forums/viewtopic.php?t=33767). It worked, but the more levels/layers you use, the more expensive it would be.
https://www.electricbike.com/cadcam-the-diy-builders-best-friend/
It would work great if you could just use slightly thicker metal and use just one layer. If you simply use very thick steel, no clamping element is needed (like Doc's beefy TAs), but...there must be a way to have a single layer of thinner steel (or possibly even aluminum, with a clamping element).
I think I found something, and I need everyones help to find a purchase source, and alternates. Imagine this as a thin single-layer steel water-jetted part:
and then add these:
http://www.mksinst.com/product/product.aspx?ProductID=333
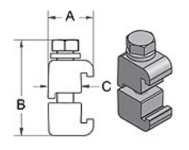
Here is the current version. If was doing this over, I would make them 8-1/4 inches long (instead of 6 inches shown) and use two U-bolts instead of one. That size would fit in the smallest post office "if it fits, it ships" box, roughly $10 to anywhere in the USA.
edit, I stumbled across an interesting fact. I've swapped the first version of these plates onto my fat bike, so I can test a DD hubmotor. When dry fitting everything together, I suddenly realized I could move the entire plate to the rear just a little, and that would tension the chain enough that I wouldn't need a tensioner, if using a 14T single-speed freewheel.
your derailleurs might be longer or shorter than mine, so your chains will be shorter or longer than mine. That being said, these plates have a 10mm wide slot for the axle, and the length of the slot is 1.6 inches (42mm).
The distance from the center of the bolt hole (the bolt which goes into the stock frames' drop out) to the front edge of the slot is 1-3/4 inches (55mm). If you want to try to make these, I recommend mocking up one of them out of 1/4-inch thick plywood, which is cheap, fast, and easy to cut.
xxxxxxxxxxxxxxxxxxxxxxxxxxxxxxxxxxxxxxxxx
Original thread starts here:
Its only a matter of time before mid-drives take over the off-road market, but...for a street hot rod ebike? large direct drive (DD) hubs remain popular. The big hold up is torque arms, and the wide variety of frames out there. Some frames have the desirable broad and flat drop-outs, which allow a lot of options. Here are 6 pages of Torque Arm ideas: https://endless-sphere.com/forums/viewtopic.php?f=2&t=26444
A while back, an Australian ES member used laser-cutting and water-jetting to make a 3-level torque-arm for a specific popular off-road frame. The three levels were welded together to create a desirable clamping element (here's the link, thanks, Sam https://endless-sphere.com/forums/viewtopic.php?t=33767). It worked, but the more levels/layers you use, the more expensive it would be.
https://www.electricbike.com/cadcam-the-diy-builders-best-friend/
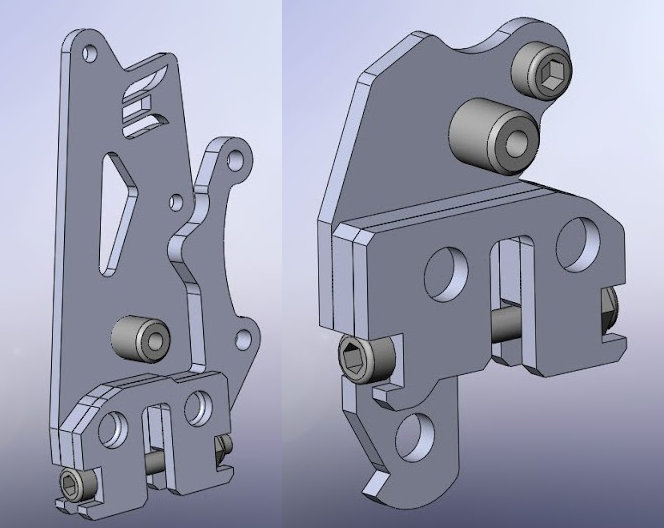
It would work great if you could just use slightly thicker metal and use just one layer. If you simply use very thick steel, no clamping element is needed (like Doc's beefy TAs), but...there must be a way to have a single layer of thinner steel (or possibly even aluminum, with a clamping element).
I think I found something, and I need everyones help to find a purchase source, and alternates. Imagine this as a thin single-layer steel water-jetted part:
and then add these:
http://www.mksinst.com/product/product.aspx?ProductID=333
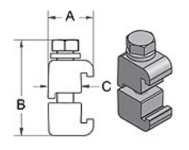