VooteleAer
100 mW
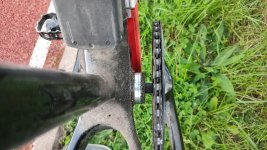
In Europe. Still haven't found a reseller. The search continues.T88 specs do look good.
My experience with composites was on the Makani electricity generating kite. (2008 to 2011)
Using an Instron testing machine we did quite a bite of material strength testing on composites and bonding aluminum, titanium metal components to composites .
For what ever reason System 3 epoxies were not included in the testing cycle.
JB Weld tech sheet does show good flex strength, 7320psi and an unusual property of zero shrinkage when cured.
Available at any hardware store.
In Europe. Still haven't found a reseller. The search continues.
T-88 is a non-brittle structural adhesive which gives superior finished results even when used under adverse working conditions. T-88 will cure in temperatures as low as 35°F which makes it an excellent choice for homebuilders living in colder climates. It is recommended by the builders of many types of homebuilt aircraft and is excellent for bonding aluminum, steel or wood. When fully cured, it is not affected by water, oil, gasoline and most other chemicals.