I am trying to get as much top speed as possible. I use the ebike in a Main Road , for not very long (maybe 20 minutes a day), and it is full of Trucks, currently I can only reach about 22 MPH which causes a bit of a disturbance in the road, cars and Trucks have to be overtaking me.
So would you drill in a brand new Motor (maybe I need to use the guarantee, I will try it for 2 Months then do this) ? Although I want to take the oportunity of then the Wheel has no Disk Brake Plate attached , so I may do it straightaway.
How often to apply Statorade? How many miles?
Also How do you monitor the temperature of the Motor?
Do you buy a Termometer Gun, use the motor for a bit then point it straightaway at it to check the temperature?
I am ready to tinker
Good attitude! Thanks for defining your goal. Unfortunately, you'll likely need to go up in voltage to increase your speed. Something called back EMF stops an electric motor from spinning faster than it's rated speed for a given voltage, which in this case, at 48V, prevents the motor from spinning faster (the back EMF is equal to the forward EMF, so it's like it's hit the wall at that speed).
There are controllers with a feature called "field weakening", that changes the back EMF in order to allow the motor to spin faster, but that feature uses more current, so not a long term solution, but in your case, if you only need the speed for part of your trip, it may be a possible solution. Unfortunately, those controllers usually cost more.
There are cheaper controller that have what is called a 3-speed switch, where speed 2 is the normal speed, while 3 may implement field weakening or some other timing tricks to achieve a higher speed. This may work possibly work for you, but not all 3-speed switches function the same, so may take some hunting.
Here are some examples, not necessarily your motor, but I've tweaked the motor parameters to match your 22mph top speed for the base case.
You need about 400 watts to go 22 mph (black curve the the load). Battery power is 493W (compensating for losses, etc.).
Our ebike motor simulator allows you to easily simulate the different performance characteristics of different ebike setups - with a wide selection of hub motors modeled, and the ability to add custom batteries and controllers and set a wide variety of vehicle parameters you'll be able to see...
ebikes.ca
Raising the power from a 26A controller to 30A or even 40A results in no change to top speed, but does provide a bit more torque (blue line. increases acceleration or climbing power), and power (red line):
Our ebike motor simulator allows you to easily simulate the different performance characteristics of different ebike setups - with a wide selection of hub motors modeled, and the ability to add custom batteries and controllers and set a wide variety of vehicle parameters you'll be able to see...
ebikes.ca
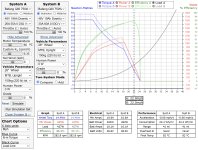
So, if speed is what you need, you'll likely need to up your voltage, which means a new higher voltage pack (60V in this example).
Our ebike motor simulator allows you to easily simulate the different performance characteristics of different ebike setups - with a wide selection of hub motors modeled, and the ability to add custom batteries and controllers and set a wide variety of vehicle parameters you'll be able to see...
ebikes.ca
You may wish to play with the simulator and get familiar with how it works. It's very accurate, so one way to try before you buy.
Statorade will last a couple of years before you need to top it off. You use very little. Drilling a hole is one way to apply it, or opening the side cover of the motor is another. I drilled on my first motor, and opened the side cover for my second. I don't worry about the warranty. These motors either work when you get them or don't, and I haven't heard of many folks getting warranty work on them.
Monitoring motor temps requires a temp sensor in the motor, attached to the stator. Some motors come with them, but you can add a sensor as well. The main hurdle is adding the wiring. It's only a single wire, since ground is already present in the motor, but fishing it through the axle is the challenge. Monitoring the case temp with your hand isn't very accurate, but better than nothing, since adding Statorade allows the heat from inside of the motor to be transferred to the case, allowing the heat to radiate from the motor. Without it, there's no path for the heat to reach the case, so the stator could be really hot, while the case feel lukewarm.
While going to a 2000W motor and compatible controller may not necessarily get you a higher speed, it can. You have to know the motor constant or turn count of the motor to know for sure. A lot of cheap motors may not list their turn counts, but may list a speed (e.g. 30 mph), and a motor voltage (motors aren't rated for voltage, so when the voltage is listed, it is usually supporting other parameter, like 30 mph using a 48V battery). So, you could by a 1000W motor, with a higher speed constant, and get the results you want without going up in voltage. Again, playing with the simulator and changing motors may help you get closer to finding the right motor.