Bluefang
10 kW
Ok, to put it bluntly i have no idea about electronics past basic soldering, no idea about electric motors and hall sensors and no idea about how to plan a build. But damn its great fun when something works the way it should
Reading this forum has really inspired me to see if i could build a electric bike, been a handyman i hoped i had enough sense to be able to take a whole lot of different ideas from other peoples posts and work them into something good. I have been reading the posts a fair bit, my plans have changed from a scooter build like Gwhy, to a bike build like Burtie and now finally to get my teeth into something i decide to try a Friction drive. I wanted it to be abit different in that most of the highend force increasing friction drives i have seen are mounted from the seat post, this is not going to work if i wanted to put it onto a full suspension bike which will be the end game with a 7kw+ motor etc......in a long time tho. I looked at the way the drives moved along and into the wheel as they increased in power and to get the same effect i have mounted my drive off the angled support tubes(no idea what to call them really) for the rear wheel with a smaller radius of travel so that it digs into the wheel about 2cm over a 10cm travel.
The parts.
The motor is a Turnigy SK 50-65 270 http://www.hobbyking.com/hobbyking/store/uh_viewItem.asp?idProduct=7709
The controller is WAY overkill 12fet Lyen controller with throttle, 3 set switch
Halls added to a PVC ring around motor at 120 intervals
3x4S turnigy 5ah 20C, overkill again
12 Tooth bike sprocket ebay
Adapter to mount the sprocket onto the motor $65
Bunch of free scraps of Alloy
$30 worth of threaded bar, bolts and nuts.
Roller is a hacked up rear hub from a scrap bike i found in some local street that i have Epoxied a PVC pipe over and then glued some old sand paper onto that.
All up cost me about $500AU, the bikes a 10yr old steel mountain bike
The bike works, can get up to about 18mph at 50% setting on the controller, i have not tried 100% as the motor is getting hot as it is and i dont think my halls are really in the right position
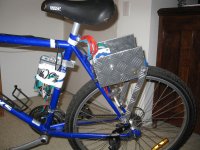
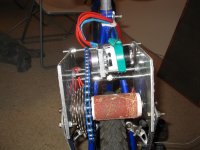
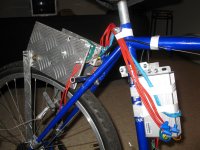
View attachment 1
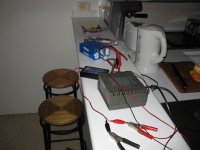
Now the questions, can anyone recommend a strong bolting clamp that will hold onto roughly 19mm diameter pipe for my next project? With my controller i have it limited to 50% of power, i assume with my 12S of batteries its limited to under 30V? The motor specs say this is the max does anyone think the motor can handle more? On the controller i have the Phase current set to 70 and the rated current set to 30, the motor is listed to handle up to 90 burst yet it gets fairly hot, can easily hold hand on it, after afew min of uphill riding on 50%, stays nice and cool on 30%. Have i got the controller set wrong, or could it be that my halls are out of wack and using more power then needed. I probably should have asked these questions first or researched more, so much more fun building and learning from mistakes.
Incidentally i have a RC ESC on the way with a thumb throttle, HVBEC and a servo tester to try out. Still have not ordered a watt meter or anything really usefull.
Fyi It took me about 2 days to build with about 1.5 of those days figuring out what i had done wrong, 1 day to solve my electrical problems, and i have only ridden it for about 30min in amongst a morning problem solving minor things and redesigning the whole way it moved in a arc over the tire, fun tho. Get some very weird looks from my neighbors.

Reading this forum has really inspired me to see if i could build a electric bike, been a handyman i hoped i had enough sense to be able to take a whole lot of different ideas from other peoples posts and work them into something good. I have been reading the posts a fair bit, my plans have changed from a scooter build like Gwhy, to a bike build like Burtie and now finally to get my teeth into something i decide to try a Friction drive. I wanted it to be abit different in that most of the highend force increasing friction drives i have seen are mounted from the seat post, this is not going to work if i wanted to put it onto a full suspension bike which will be the end game with a 7kw+ motor etc......in a long time tho. I looked at the way the drives moved along and into the wheel as they increased in power and to get the same effect i have mounted my drive off the angled support tubes(no idea what to call them really) for the rear wheel with a smaller radius of travel so that it digs into the wheel about 2cm over a 10cm travel.
The parts.
The motor is a Turnigy SK 50-65 270 http://www.hobbyking.com/hobbyking/store/uh_viewItem.asp?idProduct=7709
The controller is WAY overkill 12fet Lyen controller with throttle, 3 set switch
Halls added to a PVC ring around motor at 120 intervals
3x4S turnigy 5ah 20C, overkill again

12 Tooth bike sprocket ebay
Adapter to mount the sprocket onto the motor $65
Bunch of free scraps of Alloy
$30 worth of threaded bar, bolts and nuts.
Roller is a hacked up rear hub from a scrap bike i found in some local street that i have Epoxied a PVC pipe over and then glued some old sand paper onto that.
All up cost me about $500AU, the bikes a 10yr old steel mountain bike
The bike works, can get up to about 18mph at 50% setting on the controller, i have not tried 100% as the motor is getting hot as it is and i dont think my halls are really in the right position
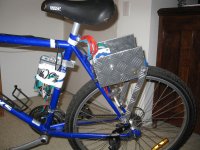
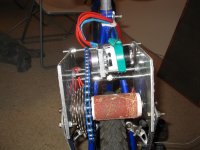
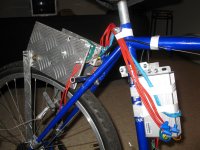
View attachment 1
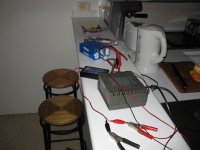
Now the questions, can anyone recommend a strong bolting clamp that will hold onto roughly 19mm diameter pipe for my next project? With my controller i have it limited to 50% of power, i assume with my 12S of batteries its limited to under 30V? The motor specs say this is the max does anyone think the motor can handle more? On the controller i have the Phase current set to 70 and the rated current set to 30, the motor is listed to handle up to 90 burst yet it gets fairly hot, can easily hold hand on it, after afew min of uphill riding on 50%, stays nice and cool on 30%. Have i got the controller set wrong, or could it be that my halls are out of wack and using more power then needed. I probably should have asked these questions first or researched more, so much more fun building and learning from mistakes.
Incidentally i have a RC ESC on the way with a thumb throttle, HVBEC and a servo tester to try out. Still have not ordered a watt meter or anything really usefull.
Fyi It took me about 2 days to build with about 1.5 of those days figuring out what i had done wrong, 1 day to solve my electrical problems, and i have only ridden it for about 30min in amongst a morning problem solving minor things and redesigning the whole way it moved in a arc over the tire, fun tho. Get some very weird looks from my neighbors.