In the past years i've seen a lot of people talking about this motor, most of them giving 25/30kW no proble, and over 500 phase amps, but my experience was completely different...
SPECS:
The thing i found weird is that outside rotor temperature was between 35 to 45°C when internal temperature was over 100°C, on the same roads with an escooter and same specs i get max 80°C internal and 50/60°C external, the ΔT between external and internal temperature of this motor is huge in my case, up to 80°C.
I opened the motor the first day i got it, didn't put ferrofluid or oil but i checked bearings, seals and added two waterproof pressure relief vales.
Motor runs fine, and torque is pretty good, but i didn't expect it to heat up so much and takes even longer to cooldown.
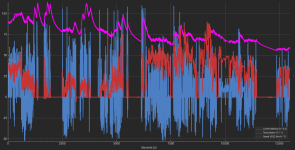
Now, is just my experience or is it always like that?
i'm thinking about doing one of those:
Internal temperature measured via KTY83/122 already inside the QS273, external temperature taken via infrared thermometer.
I've already used mineral 10W40 engine oil (car) into brushless motors and they works fine after years, but was always messy as oil leaks even through wire strands
SPECS:
- Motor QS273 40H 3.5T
- Controller: Mine, VESC based, 150A battery 350Aphase (400A peak)
- Battery: 20S LiIon 72V 90Ah nominal (84V max)
- Motor temperature limited to 110°C (120°C absolute max)
- Frame custom build stealth bomber like frame, steel/aluminium
- Weigth total around 160kg, rider/gear included
The thing i found weird is that outside rotor temperature was between 35 to 45°C when internal temperature was over 100°C, on the same roads with an escooter and same specs i get max 80°C internal and 50/60°C external, the ΔT between external and internal temperature of this motor is huge in my case, up to 80°C.
I opened the motor the first day i got it, didn't put ferrofluid or oil but i checked bearings, seals and added two waterproof pressure relief vales.
Motor runs fine, and torque is pretty good, but i didn't expect it to heat up so much and takes even longer to cooldown.
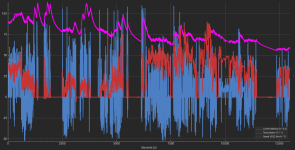
Now, is just my experience or is it always like that?
i'm thinking about doing one of those:
- adding synthetic or mineral oil inside the motore to improve heat exchange (messy)
- adding ferrofluid (messy)
- add internal fans (somewhat simple, works?)
- find a way to liquid cool the stator running two thin copper pipes via the axle (most efficient, most complex)
What do you think is the best solution, as in the future i'm going to upgrade the controller to hopefully give this motor 250A battery 700A phase.Internal temperature measured via KTY83/122 already inside the QS273, external temperature taken via infrared thermometer.
I've already used mineral 10W40 engine oil (car) into brushless motors and they works fine after years, but was always messy as oil leaks even through wire strands
Last edited: