auraslip
10 MW
- Joined
- Mar 5, 2010
- Messages
- 3,535
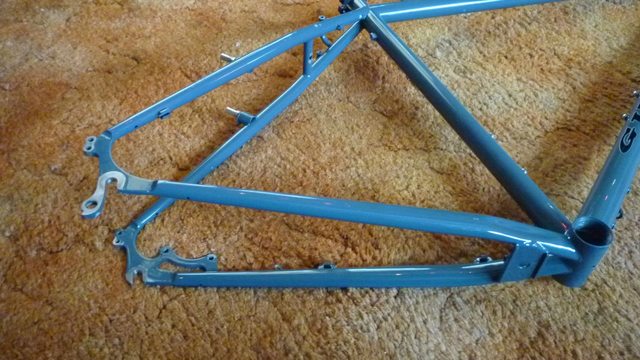
This air hardened tool steel frame. The derailleur hanger and rear portion of drop outs will be trimmed.
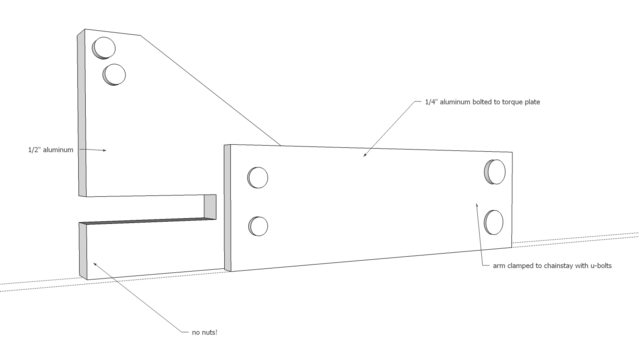
Two piece design. Torque plate will be bolted to rack mounts and possibly epoxied.
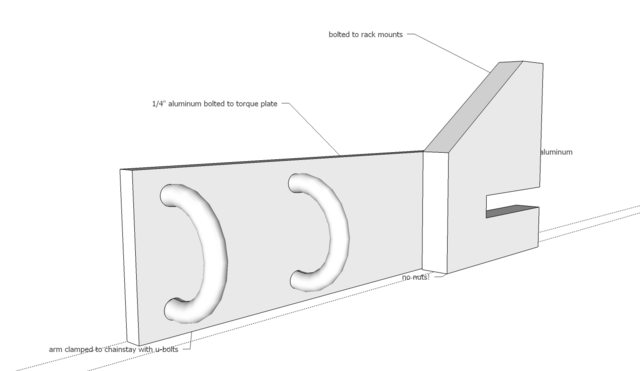
Arm clamps to frame with u-bolts. The arm is attached to the torque plate with bolts.
I wanted to use docs torque plates, but I was worried about the drop outs themselves failing at the weld. I choose to use aluminum here because it's 1/2" an inch thick and should be able to handle the torque when clamped. That's a total of an inch of clamping force on the axle. Besides, the axle these hub motors come with are made from soft steel, so there is little to gain from using hard steel in drop outs. Additionally, aluminum is much easier to work with. And cheap as well. The cost for the metal is only $15 + shipping.
Hopefully I can work this design as a standard horizontal drop out and not need a chain tensioner.
I'm pretty sure this design will work, but I'm not a machine head so I was hoping I could get some feed back.