Then today when I went to pound the roll pin in the right side, the TA popped off again
I was ponding from the outside in again. On the other side I went from the inside and had no problem.
I looked at the TA that popped off and there was a uniform layer on it. It was prob closer to .5mm though.
7 mil is ~.18 mm.
So after debating with myself for a while I decided to just weld it.
I don't have a device to measure down to 7mil and the only thing I know I can buy that's 7 mil is poly.
I didn't want to go buy poly and I dreaded the thought of doing it again.
So I mounted the wheel in the frame tightened the nut's TIGHT tight and installed the right side roll pin.
Then practiced arc welding on an old wheel barrow.
Then I went to tack some welds on the bike.
I got one little tack done and it looked like crap! (I'm not so pretty good at welding

)
But just then the neighbor chick popped in and said her bf's buddy was a welder and he could probably do it for me.
And I got to thinking I know a couple dude's who weld for a living, so I'll just have someone ells do it for me.
But for now IF I get it running before someone can weld it, I'm confident that it will be fine with the roll pins in there and the nuts tight.
So then I decided to mess with the phase wires on the MXUS.
The protective layer had been sliced through by the C clip from me messing with it so much.
So I figured at the bare minimum I had to re shrink wrap that part.
I popped the cover off. (first time ever doing any of this)
Pealed the outside layer back.
I couldn't see any bare copper.
Then I did something stupid.
I tried pushing the wires through the axle from the outside in.
The axle is razer sharp there and it sliced a bit of insulation off the tepm wire and nicked the green hall.
So then I cut the phase wires pulled them out one at a time and cut the hall wires 1&1/2 foot from the outside of the axle and pulled them though to the inside of the axle.
I'll just shrink wrap them and leave the first 4 inches in the motor.
I'm glad I did this though because two of the phase wires had little nicks in them right where that snap ring was.
I got 10AWG military spec PTFE coming from teslanv so hopefully I can squeeze them through there.
If I can't I will settle for 12 AWG of the same stuff from teslan. Since the stock one's equivalate to about 13AWG this will still be an upgrade and my motor is only 15x4 strands anyway so the 12 AWG should be adequate.
I will be dremeling the axle a bit though too, just to smooth out the sharp edges.
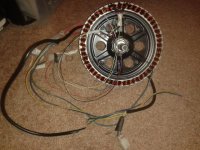
I did notice the same thing Ed noticed on his V1.
The laminations were kind of spaced a bit on one side like they are coming apart or something.
And they were a bit rusty.
yah that hole side is like that all the way around. (the brake side)
Do I have anything to worry about? It's not like a lamination is going to go flying when in use right?
Prob just little less efficiency.