I've been working on a new handpiece for the welder that will be simpler to produce with improved reliability and ergonomics. Maintaining gas seals and allowing free retraction of the electrode whilst retaining a low resistance, low friction flexible high current connection onto the electrode has been challenging but this design is now fairly reproducible. I have sent out RFQs for the internal CNC brass parts that I would need to make a short production run.
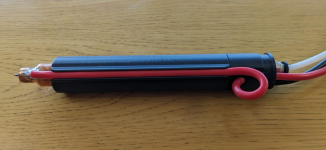
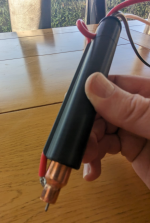
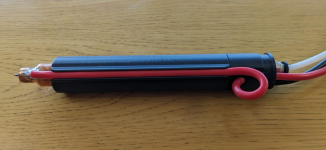
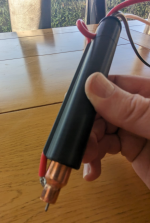