John in CR
100 TW
I decided enough of these hot controllers. I took a small centrifugal fan that came in my Bosch chargers and were left over after that hack. It's a 4cfm fan, so my .5 liter controller will have it's air replaced 3 times per second, actually a bit faster since I'm overvolting the 12V fan a bit to 14.8V nominal off of my light pack. If I wasn't such a caveman hacker I'd put a thermal switch to turn it on. Instead I'll just use a forward/reverse grip switch to turn it on manually for hills.
I didn't have a nice neat way to have it blow into the controller, so I cut a big hole in the controller end cap and epoxied the fan to the cap to work as an extractor fan. Being a centrifugal fan it works fine that way, but hopefully the air intake temp never gets high enough to damage it. The controller tilts down at the back and the fan exhaust is at the bottom, so even if something got in while the fan is off sand. water, etc. won't get into the controller that route.
Intake is at the front of the controller from the bottom near the 1st FET. I used a pair of 3/8" nylon tubing that extend down so debris and water can't easily find their way in, and I plan to tape a little balloon of screen as a filter with restricting air flow. Good thing I put 2 tubes. One restricts airflow too much and slows the fan and it seems to run properly with 2. If I even have to get into the controller again, I'll add another tube just to be sure the fan draws air freely.
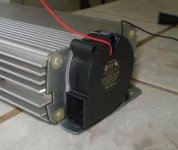
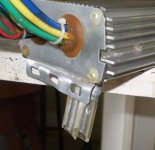
I didn't have a nice neat way to have it blow into the controller, so I cut a big hole in the controller end cap and epoxied the fan to the cap to work as an extractor fan. Being a centrifugal fan it works fine that way, but hopefully the air intake temp never gets high enough to damage it. The controller tilts down at the back and the fan exhaust is at the bottom, so even if something got in while the fan is off sand. water, etc. won't get into the controller that route.
Intake is at the front of the controller from the bottom near the 1st FET. I used a pair of 3/8" nylon tubing that extend down so debris and water can't easily find their way in, and I plan to tape a little balloon of screen as a filter with restricting air flow. Good thing I put 2 tubes. One restricts airflow too much and slows the fan and it seems to run properly with 2. If I even have to get into the controller again, I'll add another tube just to be sure the fan draws air freely.
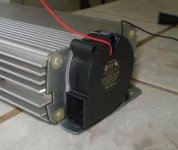
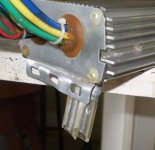