Got my VESC back from chaka about 2 weeks ago and it is very nice to replace the FVT. The vesc lacks a little grunt on start-up compared to the FVT, but having reliable brakes, the nunchuck and FOC greatly makes up for it. I've been running 10s lipo for the last couple of days and boy does that little tacon scream near the top end (I need to check the erpm, but should be somewhere around 10k rpm)!
I found a deck shape I liked on sketchup warehouse by a guy named 97longboards: https://3dwarehouse.sketchup.com/model.html?id=722f089bb160b6f4a12149f3fbea221f&commentafterlogin=add&firstcommenttext=Love%2520this%2520shape!%2520Thanks%2520for%2520sharing.&login=true
So I downloaded it, got rid of the wheel wells (don't need 'em on this 4x4!), chopped the tail a bit and added holes for my rail system.
I printed it out and did a little arts and crafts to get a full size template. I cut this out using a combination of jig saw and table saw.
I've been running this raw deck for about a week, no grip on top makes it a little hairy in the corners.
View attachment 8
I decided a liked the shape enough to try adding a little grip to the top and color to the bottom. I traced the original shape onto another section of plywood and spent a little time with the sander on this version. I'm trying a DIY spray grip utilizing Behr floor finish additive (basically seems like finely crushed quartz, maybe glass) and some spray poly to stick it down. I tried this on a piece of scrap and it seems to work in small scale, time will tell if it's an adequate solution- I'll keep ya posted.
I sprayed the bottom and sides satin black.
And I think I put about 4 coats of poly with sprinkled grip.
You may have noticed my velcro straps on the deck bottom image above, here's the sketchup of the individual brackets.
And a gratuitous printer pic, eSun PETG of course.
View attachment 4
There is a 2" wide velcro strap attached via 1/4"-20 bolt to two brackets. The brackets are then mounted to the rail, velcro strap crosses whatever needs strapping and loops under the opposite bracket/bolt combo (bolt threads covered with heat shrink tube) and adheres back to itself. Makes for really quick battery and electronic change outs- perfect as a prototyping deck.
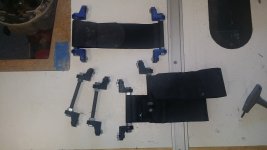