galp
100 W
Hi!
So I got this Idea to machine pulley from carbon fiber sheet. I'm thinking of using 3mm sheets and cutting 4 of them and then bolting them together to get 12mm in width. Carbon fiber could also work better because I can use 1mm or 0.5mm tool. I machined pulley from 10mm aluminum today but I don't know how will it work since there is some leftover material in each slot.
This is what I'm talking about. The blue stuff:

Circle represents the smallest tool I have for aluminum -> 2mm. The blue stuff from picture above is between circle and 3d model.

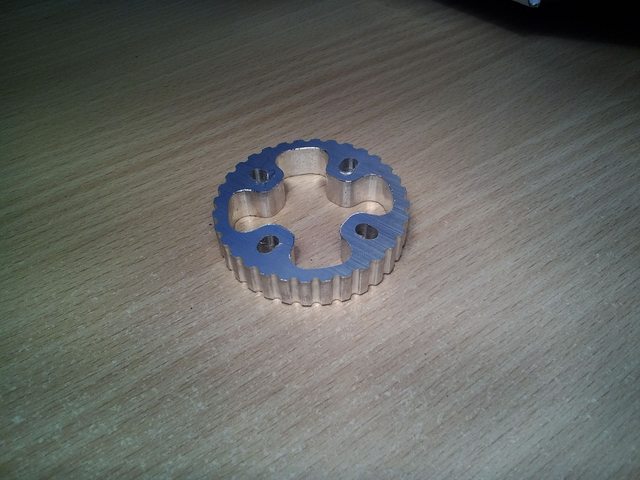
The question is could carbon fiber work for a pulley? And also should I worry about that leftover material?
BTW: If someone is interested in cf sheets you can get them on ebay. A4 paper size 200×300×3mm for about 25$.
So I got this Idea to machine pulley from carbon fiber sheet. I'm thinking of using 3mm sheets and cutting 4 of them and then bolting them together to get 12mm in width. Carbon fiber could also work better because I can use 1mm or 0.5mm tool. I machined pulley from 10mm aluminum today but I don't know how will it work since there is some leftover material in each slot.
This is what I'm talking about. The blue stuff:

Circle represents the smallest tool I have for aluminum -> 2mm. The blue stuff from picture above is between circle and 3d model.

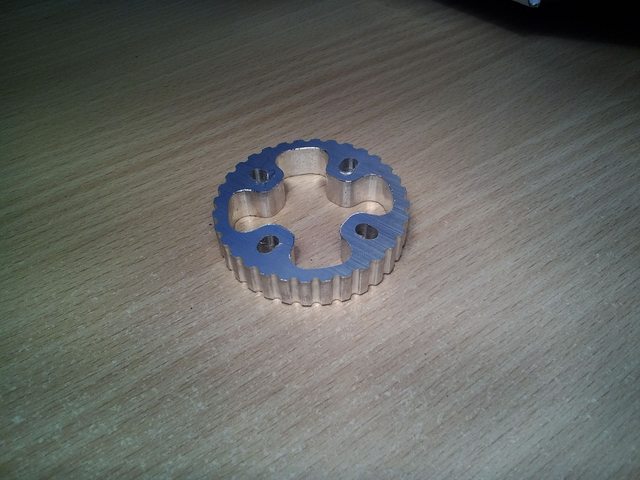
The question is could carbon fiber work for a pulley? And also should I worry about that leftover material?
BTW: If someone is interested in cf sheets you can get them on ebay. A4 paper size 200×300×3mm for about 25$.