The part that makes this a conversion from a
shell-drive into a
shaft-drive is that: the stator is "unpinned" from the axle-- by removing the square shaft key and also the aluminum shaft-to-stator collar.
Then...the stator must be solidly attached to the flat sideplate. If the new stator-brace that attaches the stator to the flat side-plate is made from thick aluminum, it will transfer
heat from the stator core to the sideplate, and then to the entire motor-shell. This optional heat-transfer is a major benefit.
For the axle to turn in the same direction as the rear wheel of the bicycle (after this conversion), you must flip over the motor so that the flat side of the motor housing will now be on the left. Also, the long part of the axle-shaft will now be on the left.
Do not worry about keeping the stator centered in the magnetic rotor. With the side plate off, you can feel a small amount of axle "wiggle" due to the one side plate axle bearing being removed with that sideplate. When the flat sideplate is re-installed, the two axle bearings and the large central stator bearing will keep the stator and magnet-ring perfectly aligned.
To describe this in another way, the stator center and the magnet-rotor center are connected to each other by the large central bearing. This stator/rotor "assembly" is attached to the flat sideplate by the bolted-on heat-bridge on the housings' flat-plate side. And then, on the other side, it is supported by the central sun-gear of the magnet-rotor being suspended in the center of the three large planet-gears.
The shaft and planet-gear carrier-disc "assembly" will continue to use their stock
square shaft-key and
snug-fit to connect to each other. This assembly is supported by the
outer ring-gear, which is firmly attached to the left side-plate. The two side-plate bearings will support the shaft, and will hold the alignment and centering of this assembly.
[insert pics of bikini girls on Ebikes, yada yada yada]
There are several ways to do this, and no single way to shape the heat-bridge ring. My plan is to make precise measurements to form the heat-bridge ring, but to make it it slightly too tall for the side-plate to seat completely. Once the sideplate screws are merely finger-snug and evenly inserted all the way around (do not make the assembly so tight that the three internal spring washers are completely compressed), I will make a final measurement of the side plate air-gap, and I will then remove the heat-bridge ring and shave it to the final dimension. This will account for minor manufacturing variations between one motor and a different one. The measurements I'm reading: are 15mm for the heat bridge width (but yours might be 14.5mm or 15.5mm). Proceed at your own risk, and with caution.
Below are rough estimates of what a heat-bridge/stator-brace would look like for
a MAC, a BMC, and a Bafang.
edit: waynebergman has reported that the stator-recess that the heat-bridge sits in on
his MAC is 67mm diameter (instead of 66mm, like mine), so be aware that assembly-line accuracy varies from one motor to another.
[insert video of Lukes Deathbike riding through a ring of fire on a wheelie while Luke is firing a submachine gun, yada yada yada]
xxxxxxxxxxxxxxxxxxxxxxxxxxxxxxxxxxxxxxxxxxxxxxxxxxxxxxxxxxxx
There are 3 options for connecting the heat bridge to the stator and side-plate.
1) Long M4 bolts pass from outside the 4mm thick side-plate, through the 15mm heat-bridge and thread into the stock 11mm-deep stator-core threaded holes (25-28mm long bolts?).
2) The heat-bridge is permanently bonded to the stator-core, and 14-16mm length bolts attach the side-plate to the heat-bridge.
3) The heat bridge is permanently bonded to the inside of the flat side-plate, and 18-22mm length bolts hold the stator onto the heat-bridge.
xxxxxxxxxxxxxxxxxxxxxxxxxxxxxxxxxxxxxxxxxxxxxxxxxxxxxxxxxx
Option 1
Carefully make a heat-bridge using the supplied dimensions, set it on the stator and verify the bolts will pass through the full-length 4mm (4.5mm?) diameter holes, and screw into the stock six stator-core threaded holes (checking for alignment and exact placement of holes). Make three short headless M4 studs to screw into the stator threads (ie, cut the heads off of three short M4 bolts), and they will be used to align the heat-bridge when you assemble the motor, and then they will mark where to drill the holes in the side-plate.
Screw-in the three studs, and set the heat-bridge onto them. The stud length should barely insert into the heat-bridge holes, they are only for alignment. Put coil springs from three retractable pens into three of the holes in the heat-bridge. Take three additional headless M4 bolts and set them on the springs so they protrude up.
Prepare to line up the side plate with the motor face-up (remember the drill dimple-spots?). Put some wet dye on the three protruding sprung stud tips, and assemble the side plate (I have used machinists' blue dye for similar jobs). You can assemble the side plate exactly and quickly if you set two 3mm drill bits in two of the rim-holes to guide you when you press it down. The three studs will mark three of the places you need to drill. You can then dis-assemble, drill those holes that have their places marked (using a clamped-on heat-bridge as a guide?), and then bolt the heat-bridge to those three holes. Then you can drill the
other three holes through the heat-bridge (or at the very least, mark their spots, if the drill bit is too short to go all the way through).
An alternative to using dye; another way is to mark the spot the studs will hit on the inside of the side-plate with black felt marker (for visual contrast), and sharpen the stud tips on a grinder so that when the side-plate is pressed down, the sharp points will make a tiny-shiny ding in the black spot on the aluminum. Test-fit the six bolts, and If they don't line up correctly, you can rotate the heat bridge and try one more time, but...too many holes will weaken the side-plate.
xxxxxxxxxxxxxxxxxxxxxxxxxxxxxxxxxxxxxxxxxxxxxxxxxxxxxxxxxx
Option 2
Temporarily bond the heat-bridge ring to the central aluminum stator core (silicone?), once its final precise size and shape are determined. Use the previously described method for making the 6 holes in the side-plate (as in option 1). Bolt the heat bridge to the side-plate, but only finger-tight.
Sand and clean the stator and heat-bridge at the places they will mate. File off the sharp outer-edge where the heat-bridge will insert. Smear some DP-420 between the stator and heat-bridge. Quickly assemble all the parts, and tighten the six bolts, so everything will be in perfect alignment while the epoxy dries.
[insert pic of Thud fixing the space station with only duct tape and baling wire while the college-educated astronauts are befuddled in the background, yada yada yada]
xxxxxxxxxxxxxxxxxxxxxxxxxxxxxxxxxxxxxxxxxxxxxxxxxxxxxxxxxxx
OPTION 3
A third option is to take the aluminum stator-core, and take the six threaded holes in it...and drill them all the way through.
Then use six bolts to attach the heat bridge to the stator...
from the back side:
Drill the six holes on the stator-core to all the way through, entering from the threaded end, using a 3.5mm drill bit as an M4 pilot. Then, temporarily bond the heat-bridge to the stator with a weak adhesive (silicone?). Drill through the stator
from the back into the heat bridge, to 3.5mm dia in all six places. If the bit is too short, you only need a shallow hole on the heat-bridge for spot-location.
http://www.mcmaster.com/#standard-drill-bits/=m7ozl2
Mark the heat-bridge and stator with a chisel/drill-dimple on both of them, so they can be assembled in the same orientation. This is to account for the minor mis-alignment of precise hole locations. Remove the heat-bridge and drill the six pilot-holes in the heat-bridge as deep as you can. Flip the heat-bridge over, and drill each hole to a diameter of 5mm, but...
just a small depth, I mean "just enough" depth that it connects to the pilot hole, perhaps a maximum depth of 5mm. Tap M4 threads into these six 3.5mm holes. The 5mm recesses should face the flat side-plate.
Be cautious and slow, test your
thread-tapping skills on a piece of scrap aluminum first, If you break-off the small tap in the heat bridge hole, it will be a nightmare to fix, and you would still have to buy a new tap to thread the other 5 holes.
Use thread-cutting lubricant, and go
one turn in, then remove the tap to clean the cuttings. Then 2-turns in, remove to clean, 3-turns / clean, etc. If you are tapping large threads into aluminum, it is very forgiving. However, small threads in small diameter holes will require a
great deal of caution.
The tap will be high-carbon steel, which has a very hard skin to hold its sharp edge,
but they are brittle, and the small ones break easily. Don't be lazy, take the extra time, and the tap will last many years of cutting soft aluminum.
After the heat-bridge holes are threaded, you can drill out the six stator-holes to 4mm, then drill a shallow recess on the back end of the hole so the bolt heads will be flush (perhaps 6mm deep?). The stator core is 16mm thick at the center. I recommend six "socket head cap screws". If the bolt-head recess is 8mm dia and 6mm deep, the remaining length is 10mm of stator-core, plus an adequate penetration into the heat-bridge threaded holes (8mm minimum), so look for 18-22mm length bolts.
http://www.homedepot.com/p/M4-7-x-2...Cap-Screw-2-Pack-08368/203538869#.UWBJaKJpzNs
Clean everything up, bolt the heat-bridge onto the stator-core, assemble the ENTIRE motor (except the flat side-plate) to ensure all the parts will align themselves to each other when the epoxy dries.
We must now permanently bond the other end of the heat-bridge to the flat side-plate. To prevent DP-420 from squeezing out into a big drip, and damaging something, smear grease on everything inside the heat bridge, and then tape off everything for two inches around the outside of the heat bridge. Sand and clean the exposed edge of the heat-bridge, and also the inside of the flat side-plate. This will ensure the mating surfaces will be rough and have no oil or grease on them, and this will make a very strong bond.
Smear some DP-420 onto the edge of the heat-bridge, and assemble the flat side plate (make sure the two dimples are aligned first). Snug up all six side plate screws and set the motor flat-side down, with the axle vertical. Wait 24-hours, and then disassemble for a quick inspection, and to clean off any hard epoxy drips. If it's all good, leave the plate off and proceed to the wrap-up...
xxxxxxxxxxxxxxxxxxxxxxxxxxxxxxxxxxxxxxxxxxxxxxxxxxxxxxxxxx
Let's wrap it up!
[insert pic of dogman finishing a diesel/electric hybrid that runs off of soybean oil he grows himself, made from near-free castaways, yada yada yada]
Estimate the best place to put the new large side-plate hole in the flat side of the motor for the wires to exit the motor. Drill an XXX hole in the flat sideplate (1/2-inch dia? 3/4-inch?) for the new fatter phase-wires, hall-wires, and possibly wires for a temp probe. I am considering epoxying a 1/2-inch ID PVC 90-degree elbow onto the hole, and having the wires exiting the flat side-plate, and pointed down to resist rain-drips and puddle-splashes.
Temp sensor that’s too cool not to share
http://endless-sphere.com/forums/viewtopic.php?f=1&t=25502
Installing a temp sensor in a hub motor
https://sites.google.com/site/shelbyelectro/motors/mods/installing-a-temp-sensor-in-a-hub-motor
This is the perfect time to run fatter phase-wires to the motor (hall wires do not need to be upgraded). Although,...in the
new configuration...it's now
easy to do
anytime if you decide you want that later. The motor should run much cooler when you are able to keep it in the upper RPMs (as a non-hub with gears), so the stock wires will likely be adequate at twice the performance, compared to what you had before, with the hub in the normal rear-wheel location.
Trim the mangled stock wire stubs, strip the ends, and solder the new wires onto them. Use heat-shrink insulation on each individual wire, and then put a large diameter section of heat-shrink around the entire bundle. Below is the butt-splice method shown to me by Amberwolf, and it is the best method I have found by far.
The magnet ring is centered by a friction fit of the OD of the central tube section into the ID of the large main central bearing, (on the stator side). On the other side, the central sun-gear (which is solidly attached to the magnet-ring shell) is suspended and
floating in-between the three planet gears. As you may recall, the planet gear-carrier is pinned to the shaft with a circlip and square-key, and this assembly is
aligned-by and
rides-on the two side-plate bearings.
The shaft does not touch the stator or magnet-ring central-tube at all (this is a concern because the stator is (of course) stationary, and the shaft will
now be spinning rapidly). The central hole in the center tube of the magnet-ring is 19mm ID, and the shaft at that point is 17mm OD.
When re-assembling, smear a small amount of NON-conductive thermal paste on every NON-epoxied end of the heat bridge. Here are several selections:
_$8 / 3g tube, Xigmatek PTI-G3606,
_$8 / 3g tube, Tuniq TX-2
_$9 / 4g tube, Arctic Cooling MX-2 Thermal Compound,
Here is a pic comparing the stock 4mm thick flat sideplate, and the "green machine" conversion sideplate with integrated heat-bridge/stator-brace which is 6mm thick in its field and 11mm thick at the reinforced rim.
View attachment 3
xxxxxxxxxxxxxxxxxxxxxxxxxxxxxxxxxxxxxxxxxxxxxxxxxx
For where the wires exit the flat side-plate, one option is to use a $2 plastic conduit elbow, listed as a "water-tight twist-in, 1/2-inch" (
http://www.mcmaster.com/#standard-electrical-conduit/=m9ztvz). The 1/2-inch bore will easily fit three 10-AWG silicone wires along with the stock tiny five hall wires (also readily available in 3/4-inch. The elbow will be pointed down, and the wires will make a U-turn up to form a "drip loop", also the opening will have some silicone sealant in it to add water-proofing that will be easy to remove if needed.
You may need to trim the threads down to a 4mm depth, so they do not protrude into the interior of the motor when you epoxy the elbow onto the side-plate hole. The supplied thin metal nut may not be thin enough (roughly 4mm) to clear the rotor edge or stator (I will check for this when I re-assemble).
Here is a pic of mr.electrics BMC conversion with the wires exiting the side plate.
Another alternative would be to use a round file to make 4 notches (three 12-ga phase wires, and one heat-shrunk bundle of 5 hall-wires) on the edge of the aluminum housing just below where the flat side plate attaches. A dab of silicone sealant on each notch would keep out moisture, and I would recommend these openings be on the lower part of the motor position. This would also allow the wires to exit the case radially (like spokes), instead of protruding from the side-plate. Add a section of large heat-shrink at the point the wire-bundle exits the side-plate and make sure the opening(s) are deburred. A years worth of minor vibration when riding can wear through the wire insulation and short the wires, and filling the exit hole(s) with silicone should help a lot to prevent that.
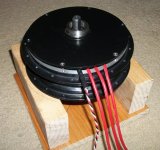