methods
1 GW
I dont know how it happened so fast but we managed to blow through an entire production run of the HVC/LVC/Parallel boards. In my personal fantasy world I had planned on designing V3.0 while we produced V2.0 and ... yea... that did not happen. It is now time to start a new PCB run and I have decided to dedicate 24 hours to integrating some small changes into the design.
V1.0/V2.0 Design thread
V2.0 Sales Thread
Prototype V1.0
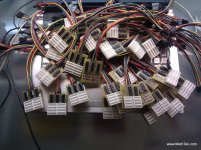
Production V2.0
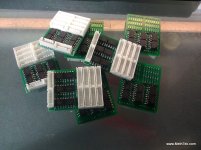
Proposed V3.0
(I will put a picture or two here after I lay it out)
Before anyone gets excited.... from a user perspective these units will be nearly identical to V2.0. The majority of the changes will be production related based on the lessons learned from the first batch. Pricing will remain the same as V2.0
If you are a mildly interested future customer - stop reading now as it is about to get boring
This thread is for dorks - and mostly just to share what I have learned in the spirit of open source design. The aspiring engineer really needs to know that there is a lot more that goes on behind the curtain than just coming up with a napkin sketch and spinning some PCB's
Lessons Learned @ MethTek
*) Hand Assembly is not sustainable. After having assembled hundreds of boards Matthew is now very fast.... but his opportunity cost is increasing. For this version it is paramount that we have a design that is Solder Stencil friendly. The current design has several aspects that were not that friendly...
- Board has parts on both sides - this greatly complicates things as a jig has to be built to elevate the board for the second application of paste - AND - the boards have to go through the oven twice. On the second pass through the oven the parts on the bottom are at risk for shifting. That is bullshit - dont even think about it. As a side note - having parts on both sides of the boards adds a second stage to the conformal coating which doubles the work - more on that later.
+ V2.0 will have parts on only one side of the board. This will be the opposite side as the thru-hole connectors. Boards will be laid flat and all surface mount parts (SIP8 and SOT23-5) will be screened. When the boards come out of the oven we will touch up, then flip over and populate all of the thru-hole JST-XH connectors. In this situation only the back of the board need be conformal coated. The only real risk on the top of the board will be the JST pin to pin spacing... there can still be some electrolysis here if users get the boards real wet but there is really nothing we can do about that. Even if we float silicone under the JST housings the pins will still be exposed on top. Good news is that this is on 100mil spacing and the pins are damn beefy... I am pretty confident that they will be robust.
*) Parts count too high... costs too much, takes too long to assemble, takes too long to inspect, too many possible failure points, takes up too much space, requires double sided board, and all around just pisses me off
- To the casual observer the question might be: "why not just use 16pin 4ch opto's?" This was covered in the original build thread - but long story short the detector I am using puts about 15K inline with the photodiodes.... 3V/15K = 200uA. That is a TINY forward diode current and severely limits the opto coupler that we can use. We not only need a darlington pair.... to meet the full temperature range we need a darlington pair with access to VCC to further increase sensitivity. Long story short - by tapping into throttle 5V, Sig, GND we are able to realize an incredible CTR that makes the circuit work over a huge range of temperature and controller input impedances (big inhale....) Ok - so....
The first round of design was a bit rushed. I added margin on top of margin to absolutely KNOW that my circuit would work. This dictated that we selected a very specific and expensive optocoupler that stood out from the rest. This opto was available only in an 8pin SIP package that is HUGE - and since each channel needed two opto's that put 12 parts on the board
. I think we can cut that in half
I have crunched the numbers a dozen times - inside out - outside in... I rolled in some of the temperature ranges to better match up with Lipo (eh... nobody is going to be running Lipo in -40C....) I also decided to narrow my compatibility range - some folks using poorly designed controller inputs (like the Lyen series that has a 2K pulldown resistor on the input) will have to pay a little more attention to the tuning of the inline throttle resistance. It is possible at the extremes now that instead of pulling the throttle to hard ground there may be only a significant throttle decay.... so maybe a 2V drop. This should be MORE THAN ENOUGH to signal a rider that time is up - and in 99% of cases I believe I will be able to achieve full throttle cut across temperature. ANYWAY......
We are keeping the same 8pin SIP package but now each one will have 2 opto's inside. This is accomplished by sharing VCC and Ground between pairs of channels.
LVC 1,2
LVC 3,4
LVC 5,6
HVC 1,2
HVC 3,4
HVC 5,6
Now we have dropped from 12 parts to 6 parts. These 6 parts that disappear will come off of the connector side of the board. As mentioned above, this will afford us quite a bit:
Single sided surface mount population
Single sided conformal coating
No need to tape off connectors before spraying (previous connector side conformal coating)
Small savings on parts
Large savings on assembly time and ability to move to solder paste methods from hand population
*) Small board changes
There were a bunch of basic lessons learned like not placing ultra-tiny SOT23-5 parts too close to huge 60mil traces. The huge traces sink too much heat while soldering and make it difficult to get consistant results during assembly. We will be spacing out the SOT23-5 parts for sure....
Larger traces... I am going to make the traces as large as possible to help combat corrosion and electrolysis damage. We have yet to lose a board to electrolysis - but it is only a matter of time - and the thicker the traces are the harder it will be for the corrosion to break the circuit. 0.005" traces can be dissolved in a matter of minutes... 0.020 are much harder to eat through
We are going to un-mask the traces between the balance taps to allow faster soldering (drag soldering) as well as the ability to "beef up" the traces. This helps for sinking heat away from the connector interface during heavy load and just makes things easier and better. There is a negative aspect in that shorting becomes "easier" but we plan to battle this with a heavier conformal coating and perhaps a foam pad to protect against abrasion.
4S, 5S, 6S will become standard. We are going to make an effort to keep all three flavors in stock and we will try our best to pass on a little savings for the 4S boards. The hobby king 4S packs are far too popular to ignore - so for those with deep pockets - we will be able to supply them boards. My opinion is that the value is not there.... but to each his own (I think it makes more sense to work with 5S and 6S packs)
*) Epoxy Option
The beta boards were epoxied. This about killed us and forced us to move to a silicone conformal coating. We are going to now re-investigate the epoxy option now that we wont have to F'around with trying to epoxy the connector side of the board. Now we will be able to run a thicker epoxy and just use a simple doughnut mold. If this works out we will be offering an epoxy version of the boards at a premium price.
*) Silk screen
We are going to try and make the silk a little more informative on this run... JST-XH pins will be marked, throttle input and output will be marked, etc
*) Built in throttle retard
We are going to bring the "Retard circuit" on to the PCB. I think we will make this a basic axial resistor slot where folks can grab a resistor off the shelf at radio crack to tune in their throttle response. Anything from 500 ohms to 5kohms - depending on controller and requirements. This will eliminate the 6pin daisy chain that comes off of the end.... we will have 3 holes for the throttle (5V, Sig, Ground) and three holes for the controller throttle input (5V, Sig, Ground). The current limiting resistor will be on the board - so all folks will have to do is cut their throttle and solder into the board. We may or may not offer a pigtail version of this at a premium... but pigtails waste a lot of god damn time... I hate them.... So I will probably charge something like $5 for anyone who wants plug and play pigtails. It should be noted that there may be length issues... the throttle side will be fine but many controllers have a very short throttle input so this may drive the need to build extensions (which we may sell) or to mount the controller closer to the battery pack
*) HVC Breaker evolves into full protection
The original design routed both LVC and HVC out to the HVC breaker. Some users have already shown that they can swap the wires around and use the HVC breaker inline between their pack and controller for true cut-out control. To make this go mainstream we will need to build a small heat sink for the IRFB4110 fets to be able to handle 40A+ controllers. This is on the back burner - but for that reason we will retain the 6 wire connection out to the HVC breaker to keep those options open.
It should be noted that HVC functionality is lost when the HVC Breaker is modified to work as inline LVC for the entire system.
*) Failures in the field
We have had amazingly few failures out in the field. A common theme has shown up where after a user "makes sparkles" buy making a balance tap mistake (i.e. shorting cells 1-6 with cells 7-12) the probability of damaging the detector chips goes up significantly. Symptoms for damage include higher discharge rates, opto's latched open, opto's latched closed. Without going into a long story about how hard I have worked to make this circuit ultra-ultra low power - suffice to say that the tradeoff for low power is an increased vulnerability to customer miss-wiring. The best way to handle a situation where the customer makes bike sparkles is to have them send the board in for testing. I have a really nice test rig that will allow me to test the leakage current of every channel and confirm the LVC and HVC functionality in a system configuration (i.e. every channel powered while one single channel triggers). As a side note - it is extremely important to test in a system configuration due to the high probability of channel cross contamination (i.e. two channels on the board start interacting due to a low impedance path etc)
*) Tented vias
I would like to tent all via's this time to help eliminate possible electrolysis points... I tried to do this on the HVC Breaker and got hosed by PCB Express when they ignored that portion of my file and opened up all of my vias. This may be their procedure or it may have to do with order of operations... but I would really like to keep my vias tented and only expose my pads for this version
*) Number of parallel JST connectors
Clearly 8 JST connectors is overkill for 99% of ebikes. The count of 8 came from the Motorcycle crowd - and I dont have a strong opinion on how to move forward. Clearly I could run fewer for the ebike guys but it does not really buy me much. I would rather have 1 part in stock that works for every application than try to save a few pennies by making multiple versions. That said... I might consider dropping the 8P to 6P and only populate the remaining parts for motorcycle guys. This would save a few cents and maybe a minute... not sure if it is worth it or not....
*) bulk of daisy chain wires
Yea... I know it is a drag hosing 6 wires all around the board. What it boils down to is increasing sensitivity and versatility. By isolating LVC and HVC I guarantee isolation between the throttle and the charge control circuit - which is DAMN IMPORTANT if you ask me - last thing I want is a huge ground loop on the ground of my 50KW race bike
Bringing out VCC is really worth it as it greatly increases sensitivity on the parts. Even though 90% of the time it is just margin.... that one time where someone is riding a bike in freezing weather (or 120F in the desert) I want to be able to guarantee performance.
Ok - I am tired of typing
That is everything I know... or at least everything I could think up in 5 minutes
So I am going to order up some parts and start the new layout. Feedback is more than welcome for those who have followed the design from V1.0
For those just now tuning in who want to make feature requests... please refer to the V1.0 design thread. This design is an ULTRA LOW POWER HARDWARE PROTECTION DESIGN and does not lend itself to bells and whistles. I will NOT be implementing any of the following:
*) No cell balancing
*) No LiFe support (there are a ton of LiFe solutions on the market - this solution is specifically for Hobby King Lipo)
*) No support for high power wiring - i.e. we are not going to make a board for paralleling / serializing the 10awg bullet connectors
-methods
V1.0/V2.0 Design thread
V2.0 Sales Thread
Prototype V1.0
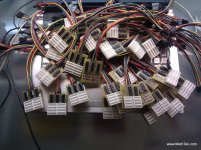
Production V2.0
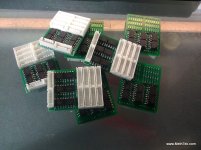
Proposed V3.0
(I will put a picture or two here after I lay it out)
Before anyone gets excited.... from a user perspective these units will be nearly identical to V2.0. The majority of the changes will be production related based on the lessons learned from the first batch. Pricing will remain the same as V2.0
If you are a mildly interested future customer - stop reading now as it is about to get boring

Lessons Learned @ MethTek
*) Hand Assembly is not sustainable. After having assembled hundreds of boards Matthew is now very fast.... but his opportunity cost is increasing. For this version it is paramount that we have a design that is Solder Stencil friendly. The current design has several aspects that were not that friendly...
- Board has parts on both sides - this greatly complicates things as a jig has to be built to elevate the board for the second application of paste - AND - the boards have to go through the oven twice. On the second pass through the oven the parts on the bottom are at risk for shifting. That is bullshit - dont even think about it. As a side note - having parts on both sides of the boards adds a second stage to the conformal coating which doubles the work - more on that later.
+ V2.0 will have parts on only one side of the board. This will be the opposite side as the thru-hole connectors. Boards will be laid flat and all surface mount parts (SIP8 and SOT23-5) will be screened. When the boards come out of the oven we will touch up, then flip over and populate all of the thru-hole JST-XH connectors. In this situation only the back of the board need be conformal coated. The only real risk on the top of the board will be the JST pin to pin spacing... there can still be some electrolysis here if users get the boards real wet but there is really nothing we can do about that. Even if we float silicone under the JST housings the pins will still be exposed on top. Good news is that this is on 100mil spacing and the pins are damn beefy... I am pretty confident that they will be robust.
*) Parts count too high... costs too much, takes too long to assemble, takes too long to inspect, too many possible failure points, takes up too much space, requires double sided board, and all around just pisses me off
- To the casual observer the question might be: "why not just use 16pin 4ch opto's?" This was covered in the original build thread - but long story short the detector I am using puts about 15K inline with the photodiodes.... 3V/15K = 200uA. That is a TINY forward diode current and severely limits the opto coupler that we can use. We not only need a darlington pair.... to meet the full temperature range we need a darlington pair with access to VCC to further increase sensitivity. Long story short - by tapping into throttle 5V, Sig, GND we are able to realize an incredible CTR that makes the circuit work over a huge range of temperature and controller input impedances (big inhale....) Ok - so....
The first round of design was a bit rushed. I added margin on top of margin to absolutely KNOW that my circuit would work. This dictated that we selected a very specific and expensive optocoupler that stood out from the rest. This opto was available only in an 8pin SIP package that is HUGE - and since each channel needed two opto's that put 12 parts on the board

I have crunched the numbers a dozen times - inside out - outside in... I rolled in some of the temperature ranges to better match up with Lipo (eh... nobody is going to be running Lipo in -40C....) I also decided to narrow my compatibility range - some folks using poorly designed controller inputs (like the Lyen series that has a 2K pulldown resistor on the input) will have to pay a little more attention to the tuning of the inline throttle resistance. It is possible at the extremes now that instead of pulling the throttle to hard ground there may be only a significant throttle decay.... so maybe a 2V drop. This should be MORE THAN ENOUGH to signal a rider that time is up - and in 99% of cases I believe I will be able to achieve full throttle cut across temperature. ANYWAY......
We are keeping the same 8pin SIP package but now each one will have 2 opto's inside. This is accomplished by sharing VCC and Ground between pairs of channels.
LVC 1,2
LVC 3,4
LVC 5,6
HVC 1,2
HVC 3,4
HVC 5,6
Now we have dropped from 12 parts to 6 parts. These 6 parts that disappear will come off of the connector side of the board. As mentioned above, this will afford us quite a bit:
Single sided surface mount population
Single sided conformal coating
No need to tape off connectors before spraying (previous connector side conformal coating)
Small savings on parts
Large savings on assembly time and ability to move to solder paste methods from hand population
*) Small board changes
There were a bunch of basic lessons learned like not placing ultra-tiny SOT23-5 parts too close to huge 60mil traces. The huge traces sink too much heat while soldering and make it difficult to get consistant results during assembly. We will be spacing out the SOT23-5 parts for sure....
Larger traces... I am going to make the traces as large as possible to help combat corrosion and electrolysis damage. We have yet to lose a board to electrolysis - but it is only a matter of time - and the thicker the traces are the harder it will be for the corrosion to break the circuit. 0.005" traces can be dissolved in a matter of minutes... 0.020 are much harder to eat through
We are going to un-mask the traces between the balance taps to allow faster soldering (drag soldering) as well as the ability to "beef up" the traces. This helps for sinking heat away from the connector interface during heavy load and just makes things easier and better. There is a negative aspect in that shorting becomes "easier" but we plan to battle this with a heavier conformal coating and perhaps a foam pad to protect against abrasion.
4S, 5S, 6S will become standard. We are going to make an effort to keep all three flavors in stock and we will try our best to pass on a little savings for the 4S boards. The hobby king 4S packs are far too popular to ignore - so for those with deep pockets - we will be able to supply them boards. My opinion is that the value is not there.... but to each his own (I think it makes more sense to work with 5S and 6S packs)
*) Epoxy Option
The beta boards were epoxied. This about killed us and forced us to move to a silicone conformal coating. We are going to now re-investigate the epoxy option now that we wont have to F'around with trying to epoxy the connector side of the board. Now we will be able to run a thicker epoxy and just use a simple doughnut mold. If this works out we will be offering an epoxy version of the boards at a premium price.
*) Silk screen
We are going to try and make the silk a little more informative on this run... JST-XH pins will be marked, throttle input and output will be marked, etc
*) Built in throttle retard
We are going to bring the "Retard circuit" on to the PCB. I think we will make this a basic axial resistor slot where folks can grab a resistor off the shelf at radio crack to tune in their throttle response. Anything from 500 ohms to 5kohms - depending on controller and requirements. This will eliminate the 6pin daisy chain that comes off of the end.... we will have 3 holes for the throttle (5V, Sig, Ground) and three holes for the controller throttle input (5V, Sig, Ground). The current limiting resistor will be on the board - so all folks will have to do is cut their throttle and solder into the board. We may or may not offer a pigtail version of this at a premium... but pigtails waste a lot of god damn time... I hate them.... So I will probably charge something like $5 for anyone who wants plug and play pigtails. It should be noted that there may be length issues... the throttle side will be fine but many controllers have a very short throttle input so this may drive the need to build extensions (which we may sell) or to mount the controller closer to the battery pack
*) HVC Breaker evolves into full protection
The original design routed both LVC and HVC out to the HVC breaker. Some users have already shown that they can swap the wires around and use the HVC breaker inline between their pack and controller for true cut-out control. To make this go mainstream we will need to build a small heat sink for the IRFB4110 fets to be able to handle 40A+ controllers. This is on the back burner - but for that reason we will retain the 6 wire connection out to the HVC breaker to keep those options open.
It should be noted that HVC functionality is lost when the HVC Breaker is modified to work as inline LVC for the entire system.
*) Failures in the field
We have had amazingly few failures out in the field. A common theme has shown up where after a user "makes sparkles" buy making a balance tap mistake (i.e. shorting cells 1-6 with cells 7-12) the probability of damaging the detector chips goes up significantly. Symptoms for damage include higher discharge rates, opto's latched open, opto's latched closed. Without going into a long story about how hard I have worked to make this circuit ultra-ultra low power - suffice to say that the tradeoff for low power is an increased vulnerability to customer miss-wiring. The best way to handle a situation where the customer makes bike sparkles is to have them send the board in for testing. I have a really nice test rig that will allow me to test the leakage current of every channel and confirm the LVC and HVC functionality in a system configuration (i.e. every channel powered while one single channel triggers). As a side note - it is extremely important to test in a system configuration due to the high probability of channel cross contamination (i.e. two channels on the board start interacting due to a low impedance path etc)
*) Tented vias
I would like to tent all via's this time to help eliminate possible electrolysis points... I tried to do this on the HVC Breaker and got hosed by PCB Express when they ignored that portion of my file and opened up all of my vias. This may be their procedure or it may have to do with order of operations... but I would really like to keep my vias tented and only expose my pads for this version
*) Number of parallel JST connectors
Clearly 8 JST connectors is overkill for 99% of ebikes. The count of 8 came from the Motorcycle crowd - and I dont have a strong opinion on how to move forward. Clearly I could run fewer for the ebike guys but it does not really buy me much. I would rather have 1 part in stock that works for every application than try to save a few pennies by making multiple versions. That said... I might consider dropping the 8P to 6P and only populate the remaining parts for motorcycle guys. This would save a few cents and maybe a minute... not sure if it is worth it or not....
*) bulk of daisy chain wires
Yea... I know it is a drag hosing 6 wires all around the board. What it boils down to is increasing sensitivity and versatility. By isolating LVC and HVC I guarantee isolation between the throttle and the charge control circuit - which is DAMN IMPORTANT if you ask me - last thing I want is a huge ground loop on the ground of my 50KW race bike

Ok - I am tired of typing
That is everything I know... or at least everything I could think up in 5 minutes

So I am going to order up some parts and start the new layout. Feedback is more than welcome for those who have followed the design from V1.0
For those just now tuning in who want to make feature requests... please refer to the V1.0 design thread. This design is an ULTRA LOW POWER HARDWARE PROTECTION DESIGN and does not lend itself to bells and whistles. I will NOT be implementing any of the following:
*) No cell balancing
*) No LiFe support (there are a ton of LiFe solutions on the market - this solution is specifically for Hobby King Lipo)
*) No support for high power wiring - i.e. we are not going to make a board for paralleling / serializing the 10awg bullet connectors
-methods